Laser Welding Technology
advantages of laser Welding
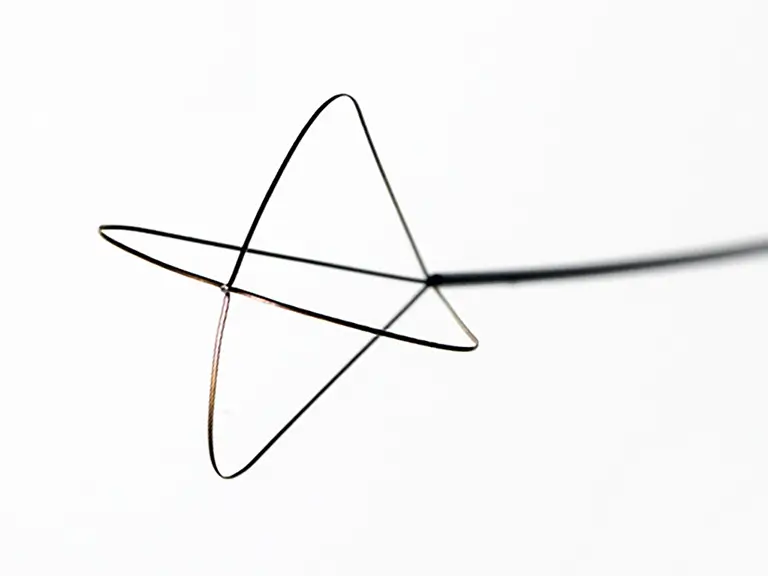
High Precision and Minimal Distortion
Laser welding provides highly accurate welds with minimal heat-affected zones (HAZ), reducing thermal distortion and ensuring precise joining of materials, especially in delicate or complex parts.
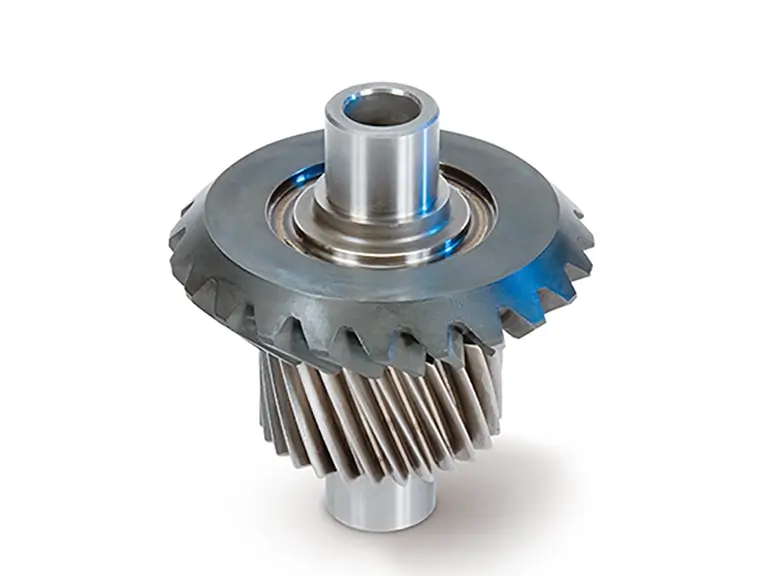
Strong and High-Quality Welds
Laser welding produces deep penetration, high-strength welds that are cleaner and more durable compared to traditional methods, with fewer defects and less post-weld processing required.
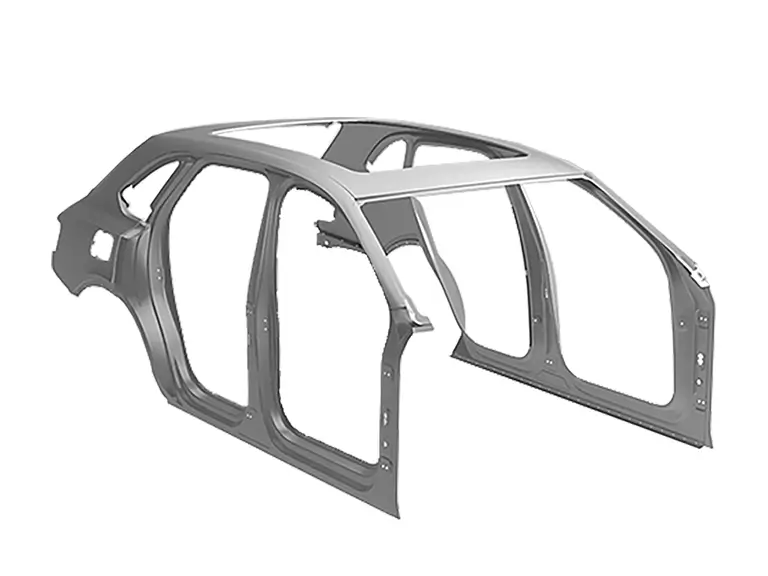
Ability to Weld Dissimilar Materials
Laser welding can effectively join dissimilar materials, such as metals with different melting points or properties (e.g., aluminum to steel), making it highly versatile for specialized applications.
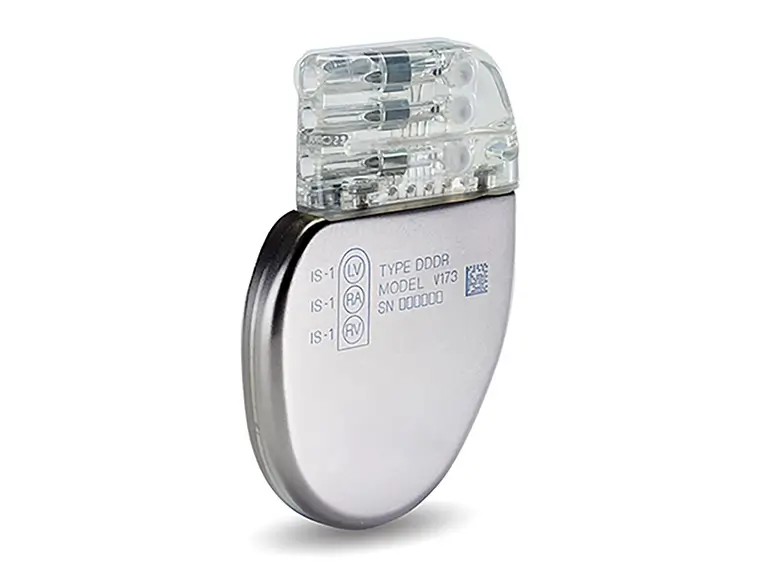
High-Speed and Automated Welding
The process can be easily automated, enabling high-speed production with consistent quality, making it ideal for large-scale manufacturing in industries like automotive, aerospace, and electronics.
types of laser Welding

Keyhole Laser Welding
A high-energy beam creates a deep, narrow penetration in the material, producing strong welds with deep penetration and minimal distortion. It is commonly used for welding thick materials and high-strength joints in industries like automotive and aerospace.
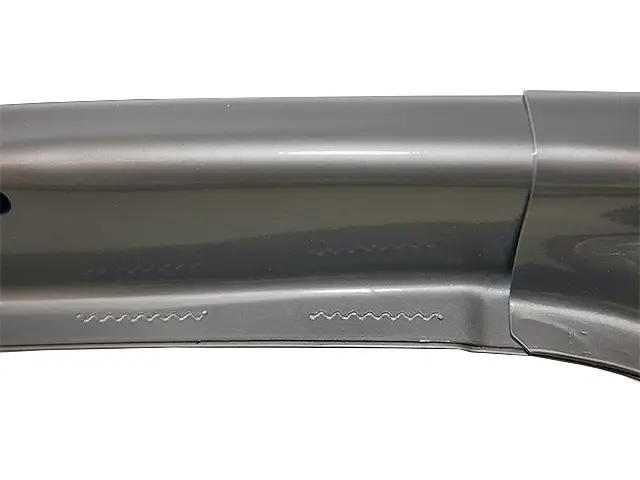
Conduction Laser Welding
The laser heats the material without melting it all the way through, resulting in shallow, wider welds. This method is used for thin materials and applications where precise control over heat input is required.
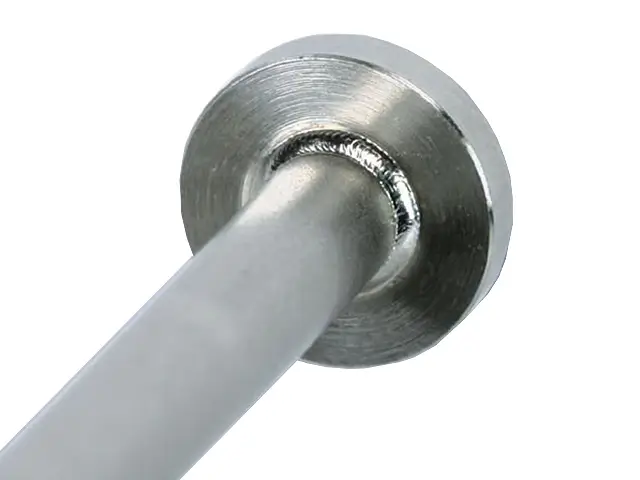
Laser Spot Welding
Involves focusing the laser beam on a small area to create localized weld points. It is used for applications that require joining small parts or thin materials, such as electronics or medical devices.
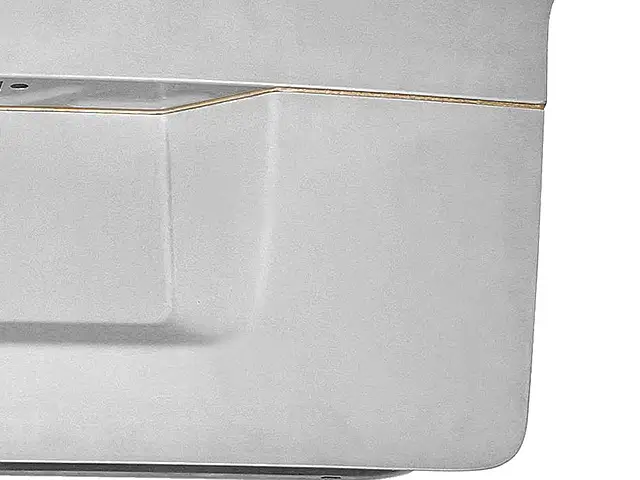
Laser Seam Welding
Continuous welding where the laser moves along the seam of the workpiece, creating a strong, uniform weld. This method is ideal for joining materials over long distances, such as in the automotive or manufacturing industries.
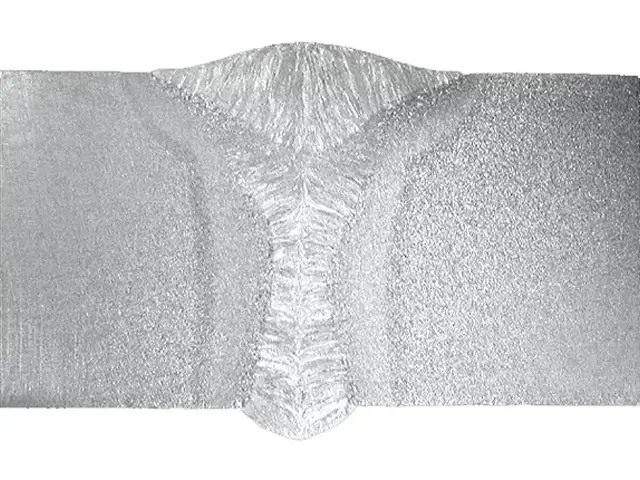
Hybrid Laser Welding
Combines laser welding with another welding process, such as MIG or TIG, to improve weld quality and increase speed. This type is ideal for joining thick materials while benefiting from the precision of laser welding.
laser vs alternate
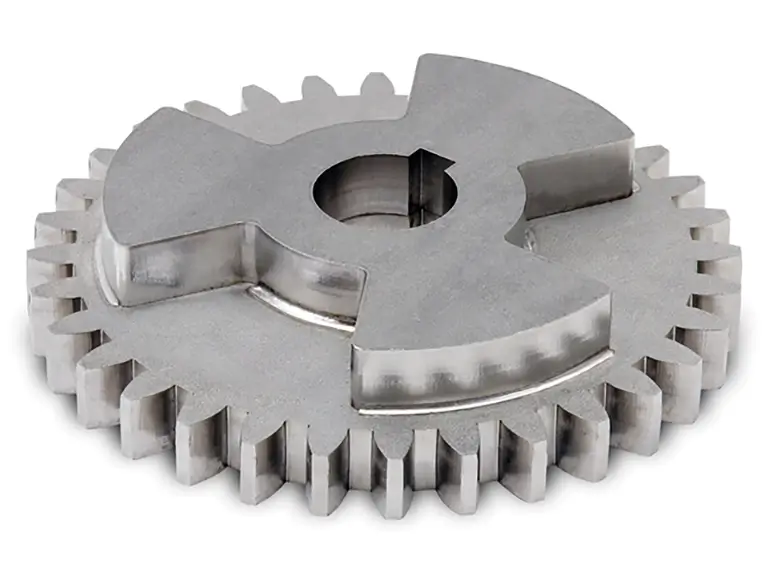
laser Welding
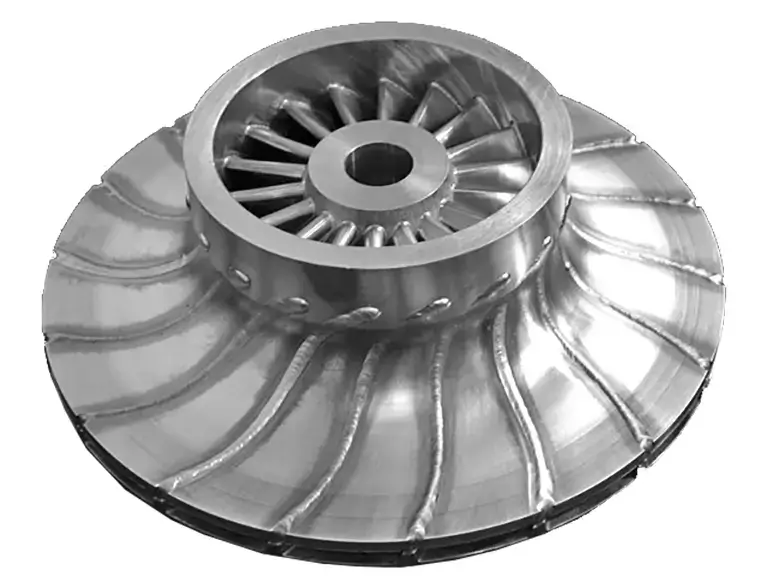
Tig/MIG Welding
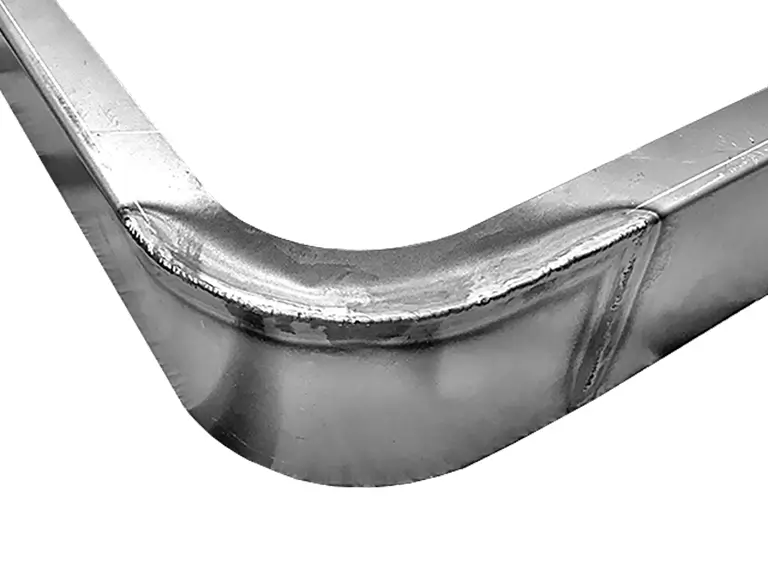
arc welding
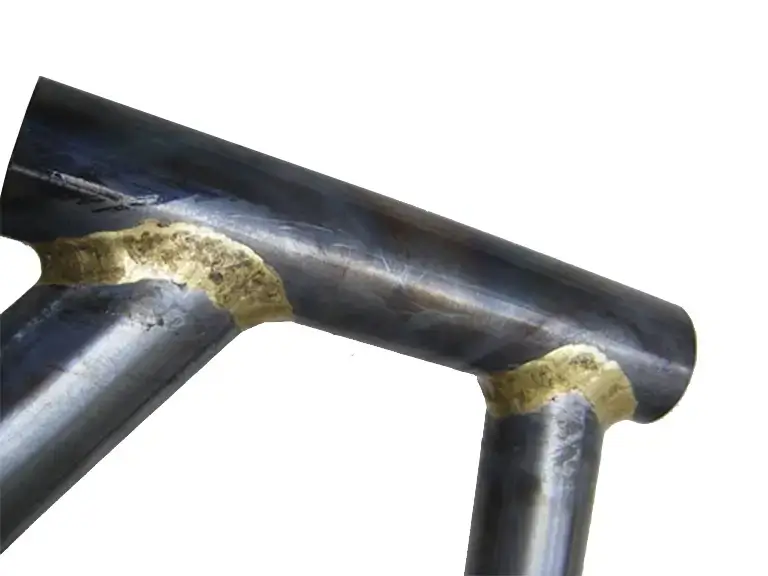