Laser cleaning technology
advantages of laser cleaning
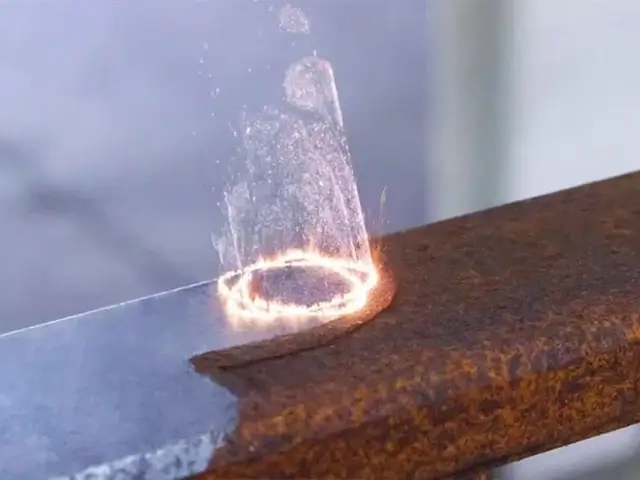
Non-Contact Process
Laser cleaning is a non-contact method, meaning it does not physically touch or wear down the material being cleaned. This prevents any damage or mechanical wear, making it ideal for delicate or sensitive surfaces.
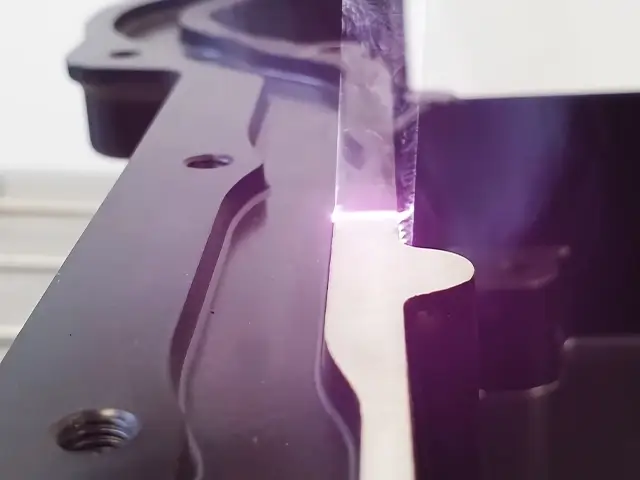
Precision and Control
Laser cleaning allows for highly controlled and localized cleaning, enabling precise removal of contaminants without affecting the surrounding material. This is especially useful in high-precision industries like aerospace and electronics.
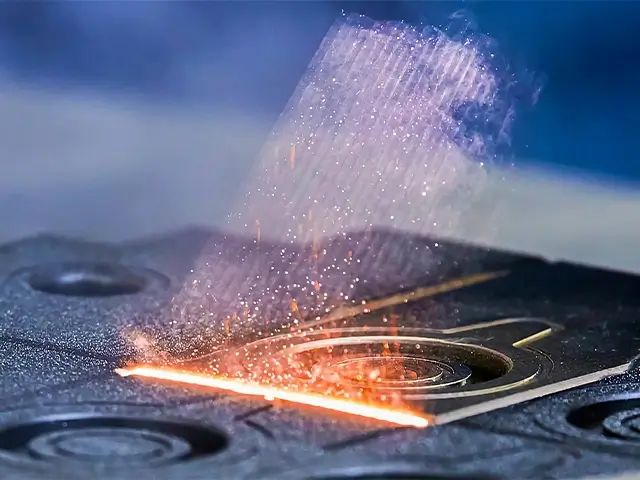
Versatility
Laser cleaning eliminates the need for harmful chemicals, abrasives, or solvents, making it an eco-friendly alternative to traditional cleaning methods. It also generates minimal waste, as contaminants are vaporized or removed as small particles.
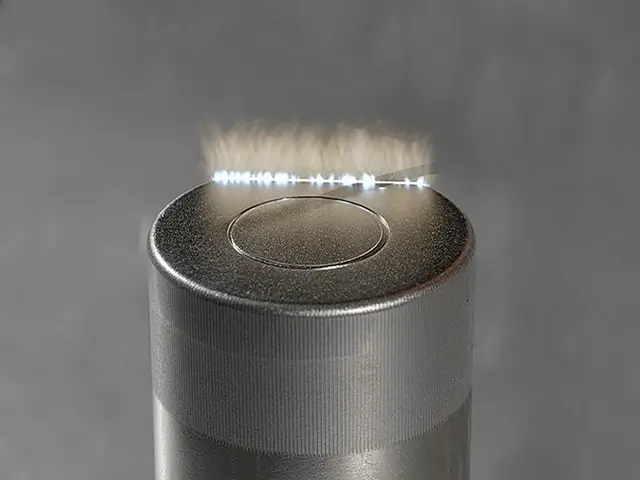
Environmentally Friendly
Laser cleaning can be used on a wide range of materials, including metals, plastics, ceramics, and even organic materials. It is effective for removing rust, paint, oil, and other contaminants from industrial surfaces without damaging the base material.
types of laser cleaning
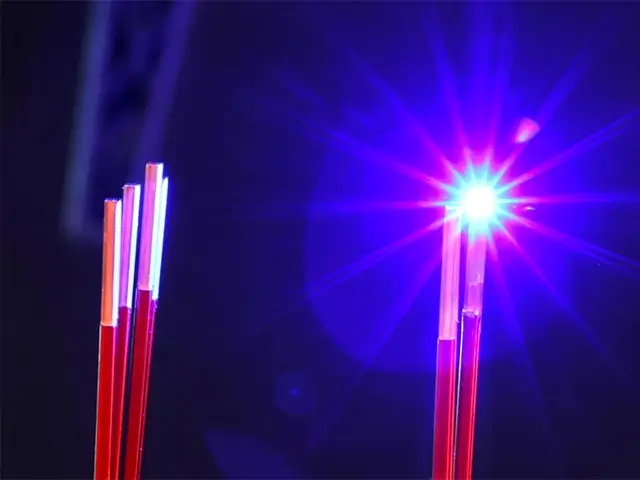
Vaporization cleaning
In this process, the laser beam heats the contaminants, such as rust, paint, or oil, to the point where they vaporize. The material is either evaporated or sublimated, leaving the underlying surface clean. This method is highly effective for removing coatings, oxides, and other surface contaminants.
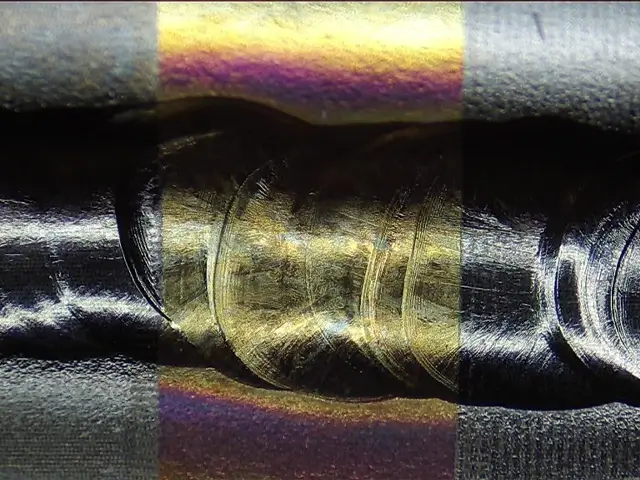
Thermal Decomposition
The laser beam is used to break down contaminants by heating them at controlled energy levels. Instead of vaporizing the material, the laser energy alters the chemical structure of the contaminants, making them easy to remove without damaging the base material. This process is often used for organic compounds like grease and oil.
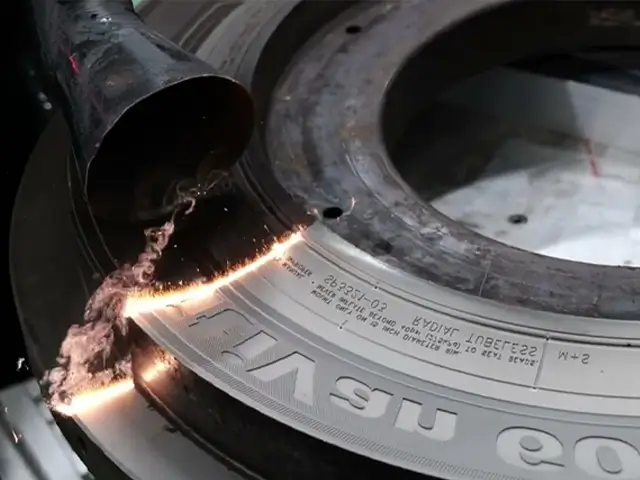
Shockwave Removal
A high-intensity laser beam creates a micro-explosion on the surface, generating shockwaves that dislodge contaminants like rust, corrosion, or dust. The shockwave forces the contaminants to break free from the substrate. This process is effective for tough layers of dirt or corrosion, such as on industrial machinery or ship hulls.
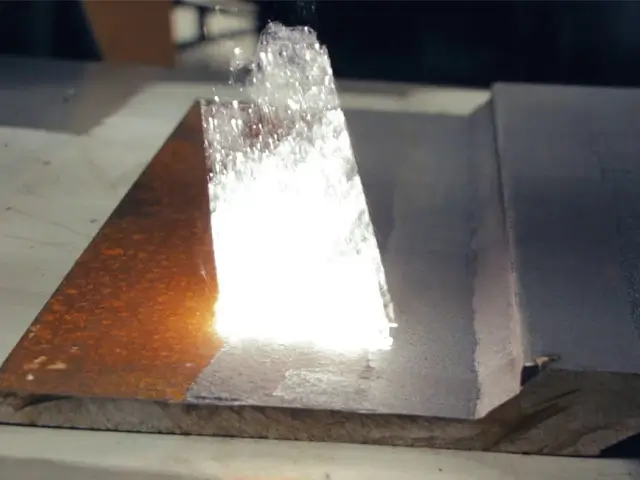
Plasma Blasting
In this method, the laser beam ionizes the material at the surface, creating a plasma plume. The energy from the plasma physically pushes contaminants away from the substrate. Plasma blasting is used in applications requiring high-intensity cleaning, such as heavy rust removal.
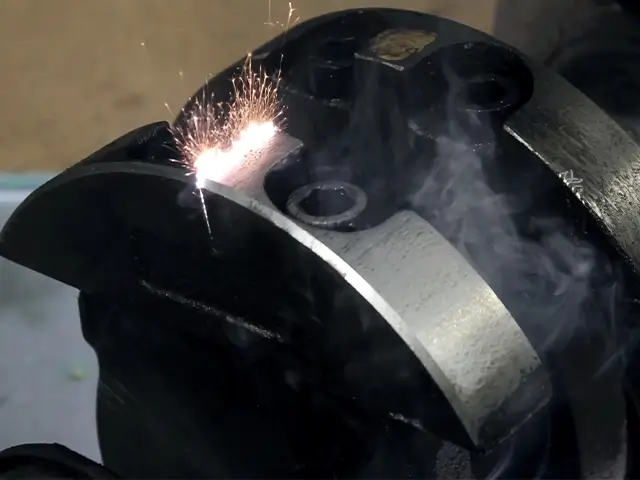
Selective Removal
This process involves using the laser to target specific contaminants while leaving the underlying material untouched. The laser’s wavelength is chosen based on the absorption properties of the contaminants versus the substrate. This method is useful for delicate applications like removing coatings from electronics or cleaning surfaces with complex geometries.
laser vs alternate
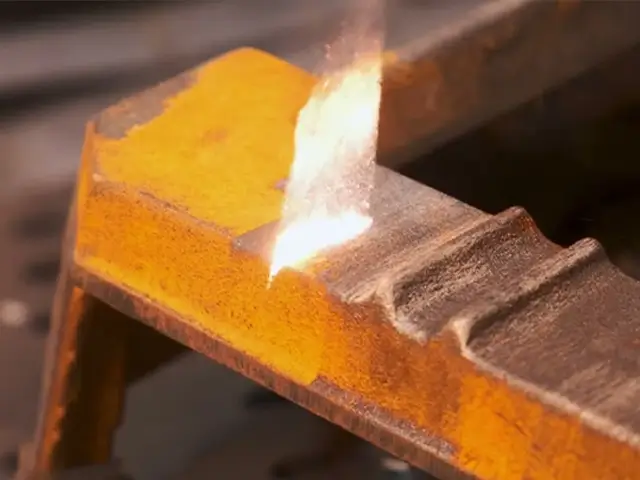
laser cleaning
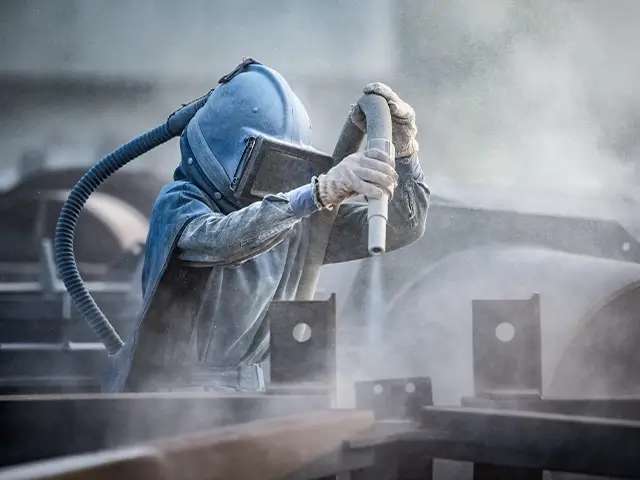
shot blasting
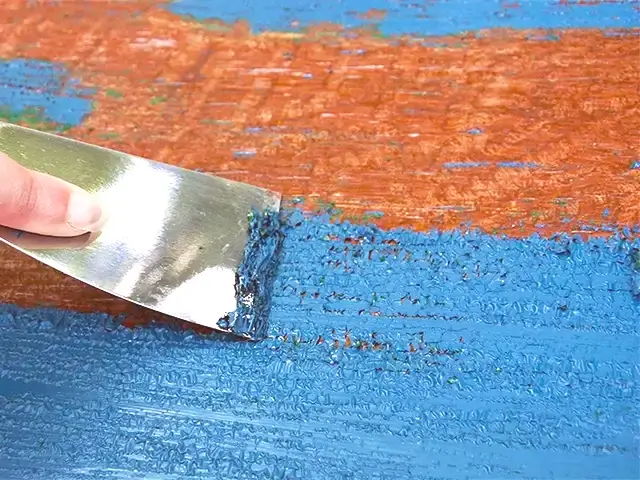
Chemical Cleaning
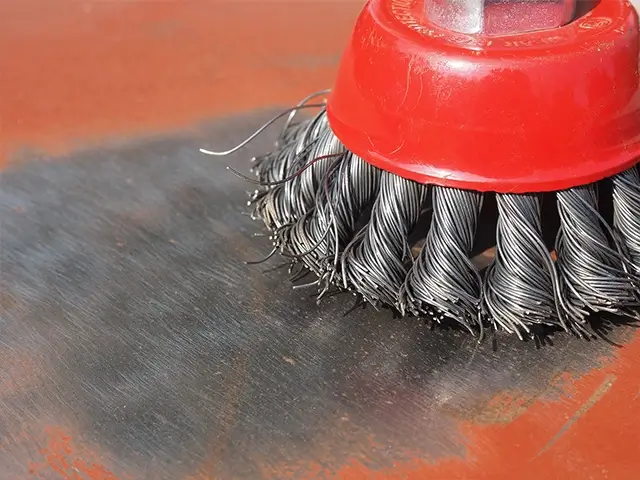