Scantech in Auto sector
Scantech Laser has established a strategic business development unit within its marketing department to focus on the automotive industry. Leveraging state-of-the-art laser cutting and welding technologies, Scantech Laser delivers precise and high-quality solutions tailored to the automotive sector’s unique needs. Our innovative approaches and advanced equipment support automotive manufacturers in enhancing production efficiency, achieving superior quality standards, and driving technological advancements. By integrating cutting-edge laser solutions, Scantech Laser plays a pivotal role in shaping the future of automotive manufacturing and ensuring that our clients stay ahead in a competitive market.
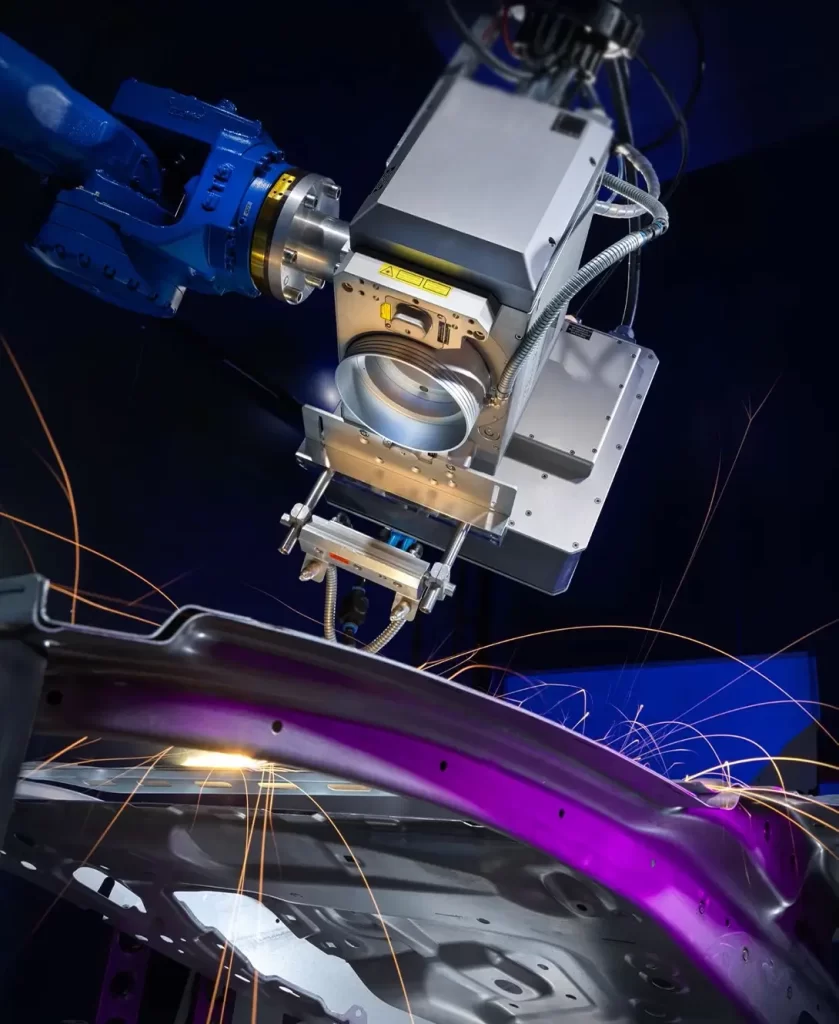
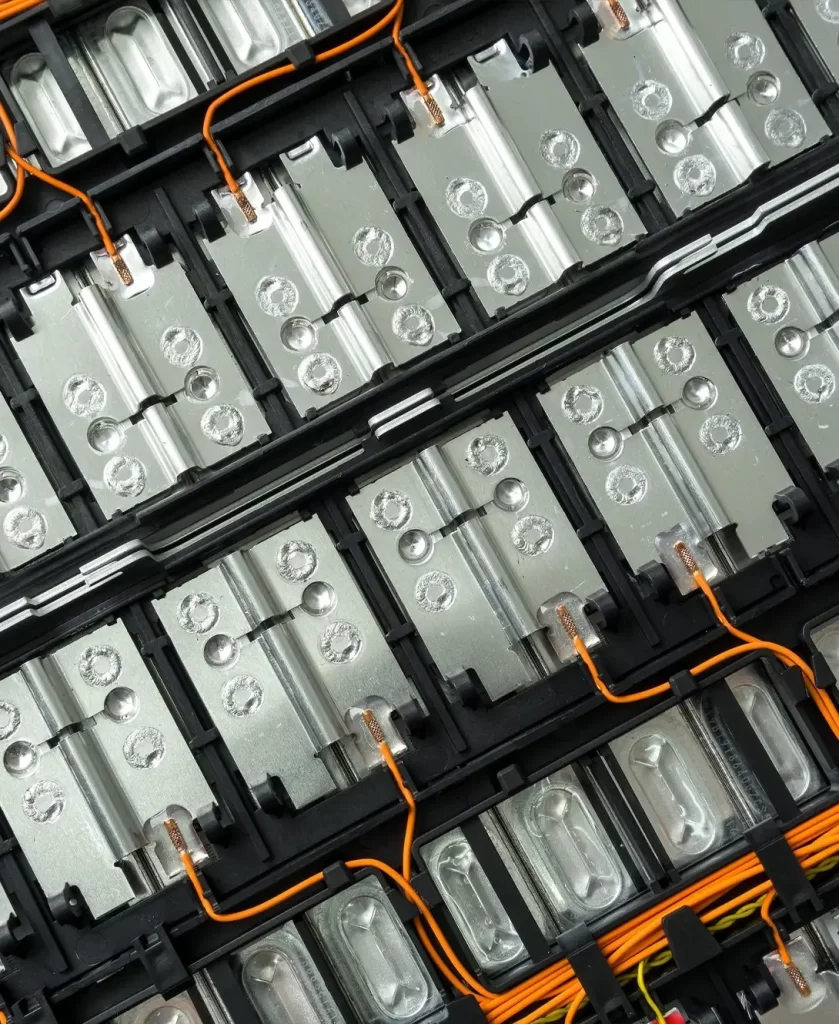
AUTOMOTIVE APPLICATIONS
OVERVIEW
Laser welding is a pivotal technology in the automotive industry, renowned for its ability to join metals with unmatched precision. By creating strong and durable welds with minimal heat-affected zones, this process is particularly suited for working with high-strength steel and aluminum—the materials essential for modern vehicle construction. Laser welding enables deep penetration with narrow seams, making it possible to join dissimilar materials and thin components without sacrificing structural integrity. This capability is crucial in the production of lightweight vehicles, as it ensures that while reducing weight for improved efficiency, the highest safety standards are maintained. The precision and efficiency of laser welding support the automotive industry’s push towards more advanced, resilient, and eco-friendly vehicle designs.
APPLICATIONS
Body-in-White (BIW) Assembly: Laser welding is extensively used in the Body-in-White stage, where various components of a vehicle’s body shell are welded together. This includes the joining of roof panels, door panels, and structural reinforcements. The precision of laser welding ensures minimal distortion and a clean, strong seam, which is critical for the vehicle’s overall structural integrity.
Battery Pack Welding: In electric vehicles (EVs), laser welding is crucial for assembling battery packs. The process is used to weld the cells together and connect them to the battery management system. The high precision and low heat input of laser welding are vital to avoid damaging sensitive battery components and ensuring reliable connections.
Tailored Blanks Welding: Tailored blanks, which are sheet metal blanks of varying thicknesses and materials, are commonly used in automotive manufacturing. Laser welding joins these blanks with precision, enabling the production of lightweight yet strong components that contribute to overall vehicle weight reduction and fuel efficiency.
Exhaust Systems: The assembly of exhaust systems requires welding materials like stainless steel, which can be challenging due to their reflective surfaces. Laser welding’s ability to create deep, high-quality welds with minimal heat input makes it ideal for this application, ensuring the durability and performance of exhaust components.
Airbag Housing: Laser welding is used to fabricate airbag housing components, where the precision and strength of the weld are critical for the safety and reliability of the airbag system. The process ensures a secure seal that can withstand the deployment forces of the airbag.
Seat Frame Welding: The welding of seat frames demands high-strength joints to ensure passenger safety in the event of a collision. Laser welding provides the necessary strength and precision, enabling the production of lightweight, yet robust seat frames.
Transmission Components: In the transmission assembly, laser welding is used to join gears, clutches, and other components. The process’s precision ensures that the welded parts maintain the exacting tolerances required for smooth and efficient power transfer within the transmission system.
Automotive Lighting Systems: The manufacturing of headlamps and tail lamps involves laser welding of plastic components. This application benefits from laser welding’s ability to create strong, airtight seals without damaging the surrounding materials.
Use Cases in Automation:
Laser welding in the automotive industry is often integrated with robotic systems, enabling fully automated production lines. Robots equipped with laser welding heads can perform complex welds with high repeatability and accuracy, which is essential for mass production. Automated laser welding systems are used in applications like BIW assembly, battery pack production, and component welding, improving efficiency and reducing manufacturing costs while maintaining high quality. The automation of laser welding also allows for greater flexibility in production, enabling manufacturers to switch between different vehicle models with minimal downtime.
overview
Laser cutting is a transformative technology in the automotive industry, celebrated for its ability to cut metals and other materials with exceptional precision and speed. This process is ideal for creating complex shapes and components from high-strength steel, aluminum, and other materials essential for modern vehicles. Laser cutting delivers clean edges with minimal burr, reducing the need for additional finishing and enabling the production of intricate parts with tight tolerances. This capability is vital for manufacturing lightweight and aerodynamically efficient vehicles, ensuring that while improving efficiency, the highest standards of performance and safety are maintained. The efficiency and versatility of laser cutting support the automotive industry’s ongoing pursuit of innovation and sustainability.
APPLICATIONS
Body Panels and Structural Components: Laser cutting is extensively used in shaping and sizing body panels and structural components. The process allows for precise cutting of materials like high-strength steel and aluminum, ensuring that each part fits perfectly into the vehicle assembly. This precision is crucial for maintaining the integrity and safety of the vehicle’s overall structure.
Interior and Exterior Trim: Automotive interior and exterior trim components often require intricate designs and high-quality finishes. Laser cutting is ideal for producing these components, offering the ability to cut complex shapes with smooth edges. This process is used to create dashboard panels, door trims, and other decorative elements that contribute to the vehicle’s aesthetic appeal.
Tailored Blanks Preparation: Tailored blanks, which are pre-cut metal sheets of varying thicknesses, are used to optimize material usage in automotive manufacturing. Laser cutting allows for the precise cutting of these blanks, enabling the creation of parts that are both lightweight and strong. This process supports the automotive industry’s goals of reducing vehicle weight while maintaining safety and performance.
Exhaust Systems: The manufacturing of exhaust systems involves cutting and shaping pipes and other components made from materials like stainless steel. Laser cutting’s ability to produce clean, precise cuts with minimal heat input makes it ideal for this application, ensuring that the exhaust system components meet strict performance standards.
Battery Enclosures and Components: In electric vehicles (EVs), laser cutting is used to create battery enclosures and other related components. The process ensures that each part is cut to exact specifications, which is crucial for the safe and efficient assembly of battery packs. Laser cutting also allows for the creation of complex shapes needed to house and protect sensitive battery components.
Airbag Components: Laser cutting is used to manufacture various components of airbag systems, including the fabric used for the airbag itself. The precision of laser cutting ensures that the fabric pieces are cut accurately, which is essential for the proper deployment and functionality of the airbag in the event of a collision.
Seat Components: The production of automotive seats involves cutting various materials, including foam, fabric, and metal. Laser cutting offers the precision needed to create components that fit together seamlessly, ensuring both comfort and safety for the vehicle’s occupants.
Transmission and Powertrain Components: Laser cutting is employed in the production of transmission and powertrain components, where precision is critical. The process allows for the accurate cutting of gears, shafts, and other parts, ensuring that they meet the exacting tolerances required for efficient power transfer and smooth operation.
Use Cases in Automation:
Laser cutting in the automotive industry is often integrated with automated systems to enhance production efficiency and consistency. Robotic arms equipped with laser cutting heads can perform complex cuts with high precision and speed, making them ideal for mass production. Automated laser cutting systems are used in applications such as body panel preparation, tailored blank cutting, and component shaping, reducing production time and costs while maintaining high-quality standards. The flexibility of automated laser cutting also allows manufacturers to quickly adapt to new designs and model variations, ensuring that production lines remain agile and responsive to market demands.
OVERVIEW
Laser marking is a precise and permanent method used to label automotive components with information such as serial numbers, barcodes, and logos. The process is ideal for marking a wide range of materials, including metals, plastics, and glass, ensuring traceability and compliance with industry regulations. Laser marking is highly valued in the automotive industry for its speed, accuracy, and ability to produce marks that are resistant to wear, heat, and corrosion, contributing to the longevity and reliability of marked components.
APPLICATIONS
Component Identification and Traceability: Laser marking is widely used to mark automotive parts with unique identifiers, such as serial numbers or QR codes. These marks are essential for tracking parts throughout the manufacturing process and ensuring traceability in case of recalls or quality control issues.
Safety and Compliance Labels: Safety-related components, like airbags and seatbelt mechanisms, often require clear, durable labeling to meet regulatory standards. Laser marking provides the precision needed to produce labels that remain legible even under harsh conditions.
Branding and Aesthetics: Automotive manufacturers use laser marking to engrave logos and other branding elements on various parts, including engine covers and interior trim pieces. This process allows for the creation of intricate designs that enhance the vehicle’s aesthetic appeal.
Switchgear and Control Panels: Laser marking is used to label buttons, switches, and control panels in the vehicle’s interior. The process ensures that markings are clear and resistant to wear, improving user experience and safety.
Use Cases in Automation:
Laser marking systems are often integrated into automated production lines, where robotic arms can position parts precisely for marking. This automation ensures high throughput and consistent quality, particularly in applications requiring high volumes of marked parts, such as component identification and branding.
OVERVIEW
Laser scribing is a method used to create precise grooves or marks on the surface of automotive components, often as part of a manufacturing process that requires subsequent breaking or bending along the scribed lines. This process is particularly valuable in the production of electronic components and other delicate parts where high precision is required.
APPLICATIONS
Laser scribing is a precise technique used to create fine grooves or markings on automotive components, facilitating processes that require controlled breaking or bending. This method is particularly valuable in the production of delicate parts and electronic components where accuracy is crucial.
PCB Scribing: In automotive electronics, laser scribing is employed to create fine grooves in printed circuit boards (PCBs). These grooves are crucial for easy separation or breaking of the PCBs during assembly, enabling the production of compact and efficient electronic modules.
Thin Film Scribing: Laser scribing is used in the production of thin-film solar cells and other thin-film materials used in automotive applications. The precision of the laser ensures accurate scribing without damaging the fragile material, allowing for high-quality production of these components.
Glass Scribing: Laser scribing is also applied to automotive glass components, such as windshields and mirrors. The process creates controlled fractures, enabling the production of custom shapes and sizes while minimizing material waste.
Connecting Rod (Conrod) Scribing or Grooving: In the automotive industry, laser scribing is used to create precise grooves on connecting rods (conrods). This scribing helps in reducing weight and optimizing performance, while ensuring that the parts maintain structural integrity under high-stress conditions.
Airbag Scoring: Laser scribing is used to score airbag components to facilitate controlled deployment. The scoring ensures that the airbag can inflate reliably and rapidly during deployment, contributing to overall vehicle safety.
Use Cases in Automation:
Automated laser scribing systems are widely utilized in high-volume automotive production environments. These systems often feature robotic handling to accurately position and process components, ensuring consistent quality and efficiency. The automation of laser scribing enhances production speed and precision, making it ideal for applications requiring high accuracy and repeatability.
OVERVIEW
Laser drilling is a precise method for creating small, high-quality holes in a variety of materials used in automotive manufacturing. The process is particularly useful for applications that require fine, clean holes with minimal material removal and high repeatability.
APPLICATIONS
Fuel Injector Nozzles: Laser drilling is used to create the precise, small-diameter holes required in fuel injector nozzles. These holes must be perfectly shaped to ensure accurate fuel delivery and optimal engine performance.
Cooling Holes in Turbine Blades: In automotive turbochargers and other high-performance components, laser drilling is used to create cooling holes in turbine blades. These holes help manage heat, ensuring the components operate efficiently under extreme conditions.
Airbag Deployment Systems: Laser drilling is also used in the manufacturing of airbag deployment systems, where precise holes are needed for the controlled release of gases during deployment. The accuracy of laser drilling ensures the reliability and safety of these critical systems.
Use Cases in Automation:
Automated laser drilling systems are employed in the automotive industry to achieve high-speed, high-precision drilling in mass production. These systems are integrated with robotic handling and positioning tools to ensure consistent hole quality and placement across large volumes of parts.
OVERVIEW
Laser cleaning is an environmentally friendly process used to remove contaminants, such as rust, paint, and oil, from metal surfaces without damaging the underlying material. This process is increasingly adopted in the automotive industry for its efficiency, precision, and minimal environmental impact.
APPLICATIONS
Rust and Paint Removal: Laser cleaning is used to remove rust and paint from metal surfaces, preparing them for welding, bonding, or coating. This process is faster and more precise than traditional methods, reducing preparation time and improving the quality of the final product.
Mold Cleaning: In the manufacturing of automotive components, laser cleaning is used to clean molds without damaging their surfaces. This process extends the lifespan of the molds and ensures the production of high-quality parts.
Surface Preparation for Bonding: Laser cleaning is also used to prepare surfaces for adhesive bonding or coating by removing contaminants that could interfere with the bonding process. The precision of laser cleaning ensures that only the unwanted material is removed, preserving the integrity of the base material.
Use Cases in Automation:
Automated laser cleaning systems are integrated into production lines to clean components at various stages of manufacturing. These systems are often combined with robotic arms for precise and efficient cleaning, ensuring consistent quality across large volumes of parts.
OVERVIEW
Laser hardening is a surface treatment process that increases the hardness and wear resistance of metal components by heating them with a laser beam. This process is essential for enhancing the durability of critical automotive parts that are subject to high levels of stress and wear, such as gears, camshafts, and crankshafts.
APPLICATIONS
Gear Hardening: Laser hardening is commonly used to treat the surface of gears, improving their resistance to wear and fatigue. The process enhances the lifespan of the gears, ensuring reliable performance in the vehicle’s drivetrain.
Camshaft and Crankshaft Hardening: Laser hardening is applied to camshafts and crankshafts to increase their durability and resistance to surface wear. The process provides a hardened surface layer while maintaining the toughness of the underlying material.
Valve Seats and Rocker Arms: In engine components such as valve seats and rocker arms, laser hardening improves wear resistance and extends the service life of these critical parts, which are constantly subjected to high loads and friction.
- Turbocharger Components: Laser hardening is applied to turbocharger components, including turbine blades, to improve their heat resistance and durability. This enhances the performance and reliability of the turbocharger under extreme conditions.
Use Cases in Automation:
Automated laser hardening systems are used in automotive manufacturing to apply precise, localized hardening to specific areas of components. The integration of robotics and laser technology allows for consistent and repeatable treatment, ensuring high-quality results in mass production.
OVERVIEW
Additive manufacturing, often referred to as 3D printing, is a transformative technology in the automotive industry, allowing for the production of complex, lightweight components with reduced material waste. Laser-based additive manufacturing processes, such as Direct Metal Laser Sintering (DMLS), enable the creation of parts with intricate geometries that are difficult or impossible to achieve with traditional manufacturing methods.
APPLICATIONS
Prototyping and Rapid Tooling: Additive manufacturing is widely used for prototyping in the automotive industry, allowing engineers to quickly produce and test parts with complex designs. This process accelerates product development and reduces time to market.
Lightweight Components: Laser-based additive manufacturing is used to produce lightweight components, such as brackets and structural supports, that contribute to overall vehicle weight reduction. The ability to create complex internal structures allows for the design of parts that are both strong and lightweight.
Custom and Low-Volume Production: Additive manufacturing is ideal for producing custom or low-volume parts, such as bespoke interior components or replacement parts for classic cars. The flexibility of the process allows for the creation of unique designs without the need for expensive tooling.
Use Cases in Automation:
Automated additive manufacturing systems in the automotive industry are used for both prototyping and production. These systems often include robotic handling and post-processing capabilities, enabling the seamless integration of 3D printing into the manufacturing workflow. The automation of additive manufacturing allows for efficient, high-quality production of complex parts with minimal manual intervention.
DEDICATED TO INNOVATION
At Scantech Laser, our commitment to the automotive industry goes beyond simply meeting customer needs; it’s about driving innovation and shaping the future of the industry. Recognizing the pivotal role that the automotive sector plays in the global economy, we are focused on delivering tailored laser solutions that address the unique challenges and opportunities within the automotive industry.
Pioneering Laser Technology for Automotive Excellence
In the fast-paced world of automotive manufacturing, precision, speed, and reliability are paramount. Scantech Laser’s state-of-the-art laser technologies are designed to meet these demands, providing solutions that enhance the efficiency and quality of automotive production processes. From laser cutting and welding to marking and drilling, our advanced systems deliver unmatched precision and consistency, ensuring that every component meets the highest standards of quality.
Comprehensive Solutions for a Dynamic Industry
Our approach to the automotive sector allows us to envision its long-term future while staying focused on current growth and development needs. Whether it’s lightweighting vehicles through advanced laser cutting techniques, enhancing safety features with precise laser welding, or improving traceability with durable laser marking, Scantech Laser’s solutions are at the forefront of automotive innovation.
Driving the Future of Automotive Manufacturing
As the automotive industry continues to evolve, Scantech Laser remains committed to supporting its growth with innovative, reliable, and efficient laser solutions. We are dedicated to understanding the industry’s unique challenges and providing the technologies that will drive its success in the years to come. Together, we’re not just meeting the needs of today; we’re propelling the automotive industry into the future.