SCANTECH IN ELECTRONICS
In the fast-paced electronics industry, laser technology is integral for achieving precision, miniaturization, and complexity in the manufacturing of components and assemblies. Lasers provide a non-contact, highly accurate method for cutting, marking, and structuring electronic parts, which minimizes material waste and damage. This technology is particularly valuable for processing sensitive materials and intricate designs required in modern electronic devices.
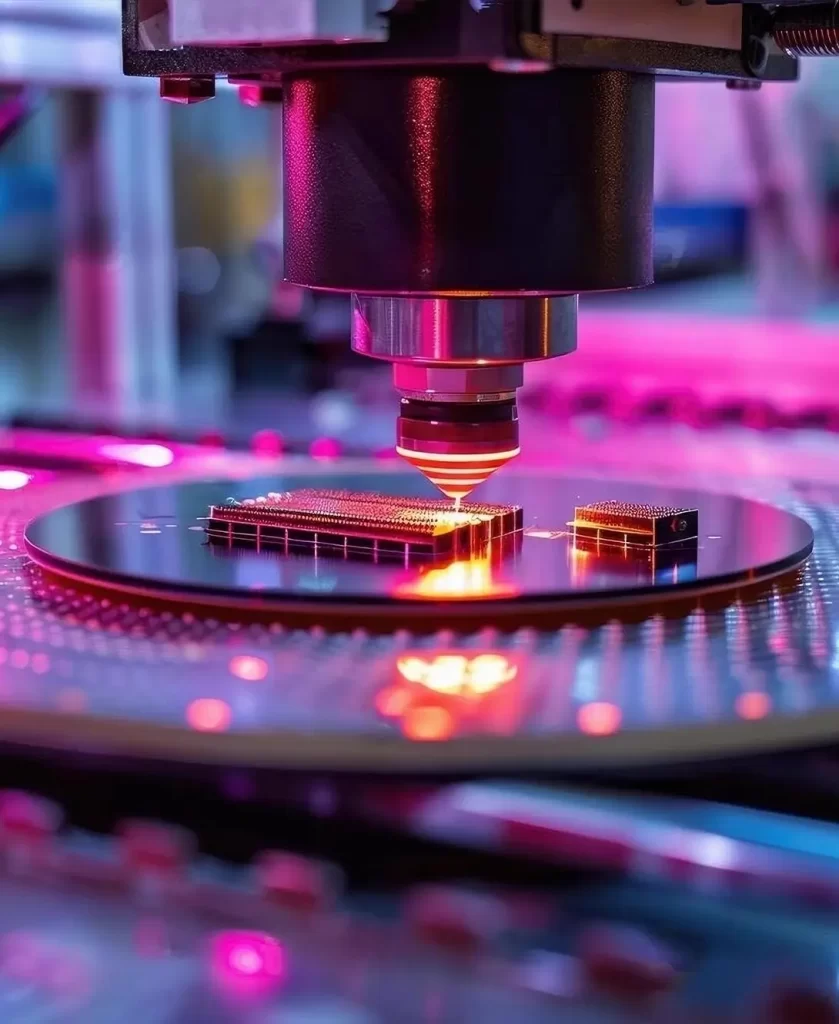
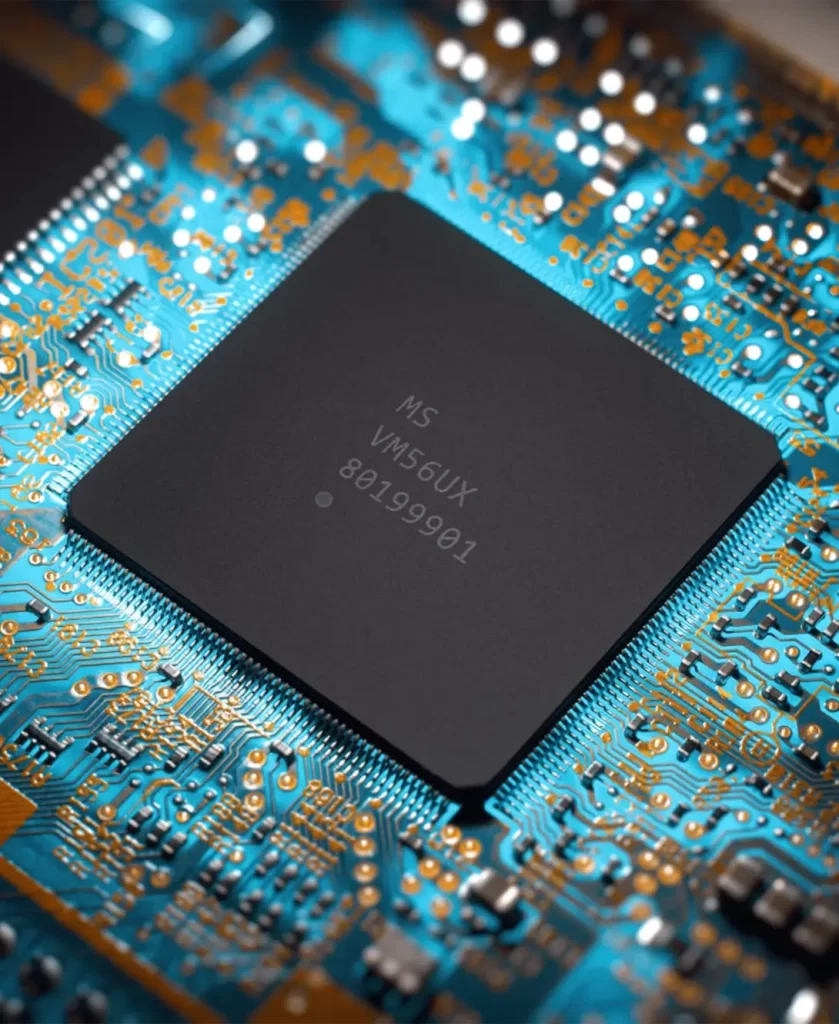
ELECTRONICS APPLICATIONS
OVERVIEW
Laser welding is a crucial technology in the electronics industry, offering precision, speed, and the ability to join delicate components with minimal thermal impact. This non-contact process uses a highly focused laser beam to fuse materials together, creating strong, clean welds that are essential for the integrity and reliability of electronic devices. Laser welding is particularly valued for its ability to join small, intricate parts made from a variety of materials, including metals and alloys commonly used in electronics manufacturing.
APPLICATIONS
Battery Pack Welding:
- Application: Laser welding is widely used in the assembly of battery packs, particularly for consumer electronics and electric vehicles. The process is used to weld tabs and connectors within lithium-ion battery cells, ensuring a strong and reliable connection.
- Benefit: Provides a precise, low-heat solution that prevents damage to sensitive battery cells while ensuring strong, consistent welds, which are critical for battery performance and safety.
Welding of Sensor Components:
- Application: Laser welding is used to assemble sensor components, such as pressure sensors, temperature sensors, and MEMS devices. These components often involve intricate metal parts that require precise, low-distortion welding.
- Benefit: Ensures that sensor components are welded with high precision, maintaining their sensitivity and accuracy, which is essential for their proper function in electronic systems.
Micro-Welding for Connectors and Terminals:
- Application: Laser welding is ideal for micro-welding small connectors, terminals, and leads used in electronic circuits. This process ensures that electrical connections are made with minimal resistance and without damaging surrounding materials.
- Benefit: Provides strong, reliable connections that are crucial for the electrical performance and durability of electronic devices, especially in high-density circuit boards.
Welding of Shielding Cans:
- Application: Laser welding is used to attach electromagnetic shielding cans to printed circuit boards (PCBs) and electronic modules. This ensures that sensitive electronic components are protected from electromagnetic interference (EMI).
- Benefit: Creates a precise, airtight weld that enhances the performance of the shielding, ensuring the device’s electromagnetic compatibility (EMC) and protecting it from external interference.
Welding of Enclosures and Housings:
- Application: Laser welding is employed to join the metal and alloy housings of electronic devices, such as smartphones, tablets, and wearables. The process provides a seamless, durable bond that enhances the aesthetic and structural integrity of the device.
- Benefit: Ensures a strong, clean weld that is both functional and visually appealing, contributing to the overall durability and design of the device.
Joining of Dissimilar Materials:
- Application: Laser welding is used to join dissimilar materials, such as copper to aluminum or stainless steel to nickel, which are common in electronic devices. The ability to control heat input precisely allows for successful welding without compromising the properties of the materials.
- Benefit: Enables the creation of complex electronic components that require the integration of different materials, improving the versatility and performance of the final product.
Advantages of Laser Welding in the Electronics Industry:
- High Precision and Control: Laser welding offers exceptional precision, making it ideal for joining small, delicate components where tight tolerances are required.
- Minimal Thermal Impact: The focused laser beam minimizes the heat-affected zone, reducing the risk of thermal distortion or damage to sensitive electronic components and materials.
- Clean and Contaminant-Free Process: Laser welding produces clean welds without the need for fluxes or filler materials, reducing the risk of contamination and ensuring the purity of the welds.
- Versatility Across Materials: Laser welding can join a wide range of materials, including metals, alloys, and dissimilar materials, making it a versatile solution for various electronic applications.
- Strength and Durability: The welds produced by laser welding are strong and durable, ensuring the long-term reliability of electronic devices, even in harsh environments.
Use Cases in Automation:
Automated laser welding systems are increasingly used in the electronics industry to enhance production efficiency and ensure consistent quality. These systems can be integrated with robotic arms and precision positioning systems to perform complex welds on small components with high repeatability. Automation allows for continuous operation, reducing cycle times and increasing throughput, which is essential for meeting the high demand in electronics manufacturing.
In summary, laser welding is a vital technology in the electronics industry, offering the precision, cleanliness, and versatility needed to manufacture high-quality electronic components and devices. Its ability to produce strong, precise welds with minimal thermal impact makes it an indispensable tool for advancing electronics technology and improving product performance.
OVERVIEW
Laser cutting is a critical technology in the electronics industry, providing unparalleled precision and efficiency for manufacturing and prototyping a wide range of electronic components and devices. This non-contact process uses a highly focused laser beam to cut materials with exceptional accuracy, making it ideal for working with the delicate and intricate parts that are common in electronics. Laser cutting is especially valued for its ability to produce clean edges, fine details, and complex geometries in various materials, including metals, plastics, and ceramics.
APPLICATIONS
PCB (Printed Circuit Board) Manufacturing:
- Application: Laser cutting is widely used in the production of PCBs to cut, drill, and depanelize circuit boards with high precision. The laser can cut complex shapes and small vias without causing damage to the board or surrounding components.
- Benefit: Enables the production of high-density, compact PCBs with precise geometries, which are essential for modern electronics, ensuring reliability and performance in electronic devices.
Cutting of Thin and Flexible Materials:
- Application: Laser cutting is employed to process thin and flexible materials such as foils, films, and flexible circuits. These materials are often used in sensors, displays, and other electronic components.
- Benefit: Provides a clean, burr-free cut that does not damage delicate materials, allowing for the production of high-quality, flexible electronic components.
Micro-Cutting for Semiconductor Components:
- Application: Laser cutting is used to create micro-features and patterns on semiconductor wafers, including scribing, dicing, and cutting of semiconductor chips. This precision cutting is crucial for the production of integrated circuits and microelectromechanical systems (MEMS).
- Benefit: Ensures precise and clean cuts at the micro-scale, which are necessary for the functionality and performance of semiconductor devices.
Production of LED Components:
- Application: Laser cutting is utilized in the manufacturing of LED components, where precise cutting of substrates, reflective materials, and encapsulation layers is required. The technology is also used for shaping and trimming LED modules.
- Benefit: Enhances the quality and efficiency of LED production, resulting in more reliable and higher-performing lighting solutions.
Prototyping and Customization of Electronic Enclosures:
- Application: Laser cutting is used to create customized enclosures and housings for electronic devices, including cutting openings for connectors, displays, and buttons. This is particularly useful for rapid prototyping and small-batch production.
- Benefit: Enables the fast and accurate production of custom enclosures, allowing designers to iterate quickly and bring new electronic products to market faster.
Cutting of Ceramic Substrates:
- Application: Laser cutting is applied to process ceramic substrates used in electronic components, such as resistors, capacitors, and hybrid circuits. The laser can cut intricate shapes and patterns in these hard materials with high precision.
- Benefit: Provides clean, precise cuts in brittle ceramic materials, reducing the risk of cracking or damage and ensuring high-quality electronic components.
Advantages of Laser Cutting in the Electronics Industry:
- High Precision and Accuracy: Laser cutting offers exceptional precision, enabling the production of intricate designs and small features with tight tolerances, which are essential in electronics manufacturing.
- Minimal Thermal Impact: The focused laser beam minimizes the heat-affected zone, reducing the risk of thermal distortion or damage to delicate electronic components and materials.
- Versatility Across Materials: Laser cutting can be applied to a wide range of materials used in the electronics industry, including metals, polymers, ceramics, and composites, making it a versatile solution for various applications.
- Clean and Contaminant-Free Process: Laser cutting produces minimal debris and does not require the use of chemicals or abrasives, making it a clean and environmentally friendly process suitable for the stringent cleanliness standards in electronics manufacturing.
- Rapid Prototyping and Production: Laser cutting is a fast and efficient process that can handle high-volume production while maintaining consistent quality, making it ideal for both prototyping and mass production in the electronics industry.
Use Cases in Automation:
Automated laser cutting systems are increasingly used in the electronics industry to enhance production efficiency and ensure consistent quality. These systems can be integrated with CAD/CAM software to automate the cutting process, allowing for precise and repeatable production of complex parts. Automation also allows for continuous operation, reducing cycle times and increasing throughput, which is essential for meeting the high demand in electronics manufacturing.
In summary, laser cutting is a vital technology in the electronics industry, offering the precision, cleanliness, and versatility needed to manufacture high-quality electronic components and devices. Its ability to produce complex shapes and intricate patterns with minimal thermal impact makes it an indispensable tool for advancing electronics technology and improving product performance.
OVERVIEW
Laser marking is an essential technology in the electronics industry, providing a precise, durable, and efficient method for applying information directly onto electronic components, circuit boards, and devices. This non-contact process uses a focused laser beam to create permanent marks, such as serial numbers, logos, QR codes, and other identifiers, on a variety of materials, including metals, plastics, and ceramics. Laser marking is particularly valued for its ability to produce high-resolution, legible marks that are crucial for traceability, branding, and compliance in the fast-paced electronics industry.
APPLICATIONS
PCB (Printed Circuit Board) Marking:
- Application: Laser marking is widely used to mark PCBs with critical information, such as serial numbers, barcodes, and date codes. These marks are essential for tracking and identifying boards throughout the manufacturing process and during the product’s lifecycle.
- Benefit: Provides high-precision, permanent marks that do not interfere with the functionality of the PCB, ensuring reliable traceability and compliance with industry standards.
Component Identification:
- Application: Laser marking is employed to mark individual electronic components, such as resistors, capacitors, and IC chips, with identification numbers, part codes, and manufacturer logos. This is crucial for quality control and inventory management.
- Benefit: Ensures clear, legible marks that remain readable even in high-density, miniaturized components, aiding in accurate identification and assembly.
Branding and Logos on Electronic Devices:
- Application: Manufacturers use laser marking to apply branding elements, such as logos, model numbers, and certification marks, onto the housings and enclosures of electronic devices, including smartphones, laptops, and consumer electronics.
- Benefit: Creates high-contrast, aesthetically pleasing marks that enhance brand identity and ensure compliance with regulatory requirements, while withstanding wear and environmental conditions.
QR Codes and Data Matrix Marking:
- Application: Laser marking is used to create QR codes and data matrix codes on electronic components and devices. These codes can store detailed information, such as manufacturing data, which can be scanned and retrieved for traceability, quality control, and inventory management.
- Benefit: Enables fast and accurate data retrieval, improving process efficiency and product traceability, which is essential for meeting industry and regulatory standards.
Marking on Flexible and Thin Materials:
- Application: Laser marking is applied to flexible and thin materials used in electronic applications, such as flexible circuits, labels, and tags. The precision of laser marking ensures that even delicate materials are marked without damage.
- Benefit: Provides a non-invasive marking solution that does not compromise the integrity of thin or flexible materials, ensuring the durability and legibility of marks.
Traceability for Semiconductor Components:
- Application: Laser marking is critical for marking semiconductor components with traceability information, such as batch numbers and manufacturing codes. These marks help track the components through the supply chain and into final products.
- Benefit: Ensures that each component can be accurately traced back to its origin, reducing the risk of counterfeit parts and improving overall product quality and safety.
Advantages of Laser Marking in the Electronics Industry:
- High Precision and Resolution: Laser marking offers exceptional precision, allowing for the creation of fine, detailed marks on small and intricate components, which are essential in the electronics industry.
- Permanent and Durable Marks: The marks produced by laser technology are permanent and resistant to wear, chemicals, and environmental factors, ensuring that important information remains legible throughout the product’s life.
- Non-Contact Process: As a non-contact method, laser marking does not physically alter or damage the material being marked, preserving the integrity of sensitive electronic components.
- Versatility Across Materials: Laser marking can be applied to a wide range of materials used in electronics, including metals, plastics, ceramics, and composites, making it a versatile solution for various applications.
- Fast and Efficient: Laser marking is a rapid process that can be easily integrated into high-speed production lines, improving manufacturing efficiency and reducing lead times.
Use Cases in Automation:
Automated laser marking systems are increasingly used in the electronics industry to enhance production efficiency and ensure consistent quality. These systems can be integrated with robotic arms or conveyor systems to perform high-speed marking on multiple parts with high repeatability. Automation allows for seamless integration into existing production workflows, enabling continuous operation and reducing manual intervention.
In summary, laser marking is a vital technology in the electronics industry, offering the precision, durability, and versatility needed to ensure that electronic components and devices are correctly identified and traceable. Its ability to produce permanent, high-quality marks that withstand the rigors of the electronics manufacturing environment makes it an essential tool for advancing electronics technology and improving product quality.
OVERVIEW
Laser structuring is an advanced technology used in the electronics industry to create intricate patterns, microstructures, and textures on the surfaces of electronic components and substrates. This non-contact process uses a focused laser beam to precisely modify the surface of materials, enabling the creation of features that are essential for the performance, functionality, and miniaturization of electronic devices. Laser structuring is particularly valued for its ability to produce highly detailed and complex designs with minimal material waste, making it an indispensable tool in modern electronics manufacturing.
APPLICATIONS
Creation of Microchannels and Patterns in PCBs:
- Application: Laser structuring is used to create microchannels, grooves, and intricate patterns on printed circuit boards (PCBs). These features are essential for guiding electrical connections, managing heat, or integrating microfluidic systems in advanced electronics.
- Benefit: Enables the production of high-density, compact PCBs with precise control over electrical pathways, improving the performance and reliability of electronic devices.
Surface Texturing for Enhanced Adhesion:
- Application: Laser structuring is applied to texture the surfaces of electronic components or substrates to enhance the adhesion of coatings, adhesives, or other layers. This is crucial for ensuring the durability and performance of multi-layered electronic assemblies.
- Benefit: Provides consistent and controlled surface textures that improve the bonding strength of subsequent layers, reducing the risk of delamination and improving the longevity of the product.
Fabrication of Antennas and RF Components:
- Application: Laser structuring is employed to create precise patterns for antennas and radio frequency (RF) components on various substrates, including ceramics and polymers. This process is critical for the miniaturization of communication devices.
- Benefit: Allows for the production of highly efficient and compact antennas with complex geometries, essential for modern wireless communication technologies.
Selective Material Removal for Circuit Integration:
- Application: Laser structuring is used to selectively remove material from electronic substrates, enabling the integration of circuits, sensors, or other components directly into the substrate. This process is vital for the development of flexible electronics and integrated circuits.
- Benefit: Facilitates the production of lightweight, flexible, and integrated electronic devices, expanding the possibilities for wearable technology and other advanced applications.
Enhancement of Surface Properties for Optical Components:
- Application: Laser structuring is applied to create microstructures on the surfaces of optical components, such as lenses or waveguides, used in electronic devices. These structures can manipulate light in specific ways to enhance the performance of optical systems.
- Benefit: Improves the efficiency and functionality of optical components in electronic devices, leading to better performance in applications such as displays, sensors, and communication systems.
Creation of 3D Structures for Microelectromechanical Systems (MEMS):
- Application: Laser structuring is used to fabricate 3D microstructures for MEMS devices, which are critical in sensors, actuators, and other miniaturized electronic systems. The process allows for precise control over the dimensions and shapes of these tiny structures.
- Benefit: Enables the production of complex MEMS devices with high precision and repeatability, essential for applications in automotive, aerospace, and consumer electronics.
Advantages of Laser Structuring in the Electronics Industry:
- High Precision and Resolution: Laser structuring offers exceptional precision, allowing for the creation of fine, intricate patterns and microstructures that are essential for advanced electronic devices.
- Versatility Across Materials: Laser structuring can be applied to a wide range of materials used in electronics, including metals, polymers, ceramics, and semiconductors, making it a versatile solution for various applications.
- Minimal Material Waste: The process is highly efficient, removing only the material necessary to create the desired structure, reducing waste and lowering production costs.
- Non-Contact Process: As a non-contact method, laser structuring does not physically alter or damage the underlying material, preserving the integrity of delicate electronic components.
- Enhanced Design Flexibility: The ability to create complex and precise structures opens up new possibilities for the design and functionality of electronic devices, enabling innovation and the development of next-generation technologies.
Use Cases in Automation:
Automated laser structuring systems are increasingly being integrated into electronics manufacturing to enhance production efficiency and ensure consistent quality. These systems can be programmed to perform complex structuring tasks with high repeatability, reducing human error and increasing throughput. Automation also allows for the seamless integration of laser structuring with other manufacturing processes, such as deposition or assembly, enabling a more streamlined and efficient production workflow.
In summary, laser structuring is a vital technology in the electronics industry, offering the precision, versatility, and efficiency needed to create advanced electronic components and devices. Its ability to produce intricate patterns, microstructures, and textures with minimal material waste makes it an essential tool for advancing electronics technology and improving product performance.
OVERVIEW
Laser drilling is a highly precise and efficient technology that plays a crucial role in the electronics industry. This non-contact process uses a focused laser beam to create small, accurate holes in various materials, including metals, ceramics, and polymers. Laser drilling is particularly valued for its ability to produce high-density arrays of micro-holes, complex geometries, and precise vias, which are essential for the functionality of modern electronic devices. The minimal thermal impact and high repeatability of laser drilling make it an ideal solution for the miniaturization and reliability of electronic components.
APPLICATIONS
Via Drilling in Printed Circuit Boards (PCBs):
- Application: Laser drilling is widely used to create vias (vertical interconnect accesses) in PCBs, which connect different layers of the circuit board. These microvias are critical for the electrical performance and miniaturization of advanced electronic devices.
- Benefit: Provides precise and clean drilling of microvias with minimal thermal impact, ensuring reliable electrical connections and high-density PCB designs.
Micro-Hole Drilling for Semiconductor Components:
- Application: Laser drilling is employed to create micro-holes in semiconductor wafers and components, such as sensors, microelectromechanical systems (MEMS), and integrated circuits (ICs). These holes are essential for functionalities like fluid flow, heat dissipation, and signal transmission.
- Benefit: Ensures high precision and repeatability in drilling micro-holes, which are critical for the performance and reliability of semiconductor devices.
Heat Dissipation Holes in Electronic Housings:
- Application: Laser drilling is used to create ventilation and heat dissipation holes in electronic housings and enclosures. These holes help manage heat within devices, improving their performance and longevity.
- Benefit: Provides accurate and clean drilling of holes that enhance thermal management in electronic devices, reducing the risk of overheating and extending the device’s lifespan.
Drilling of Flexible Circuits:
- Application: Laser drilling is ideal for creating holes in flexible circuits and substrates, which are used in various portable and wearable electronics. The process ensures that the delicate materials are not damaged during drilling.
- Benefit: Enables the production of flexible electronics with precise hole placement and size, ensuring the integrity and functionality of the circuits.
Creation of Microfluidic Channels:
- Application: In the fabrication of lab-on-a-chip devices and other microfluidic systems, laser drilling is used to create tiny channels and holes that guide fluids through the device. These are crucial for applications in diagnostics and biosensing.
- Benefit: Provides precise control over the size and shape of microfluidic channels, ensuring accurate fluid handling and reliable device performance.
Connector and Terminal Drilling:
- Application: Laser drilling is used to create holes in connectors, terminals, and other interconnect components in electronic devices. These holes are vital for ensuring secure and reliable electrical connections.
- Benefit: Ensures the precision and quality of drilled holes, which are critical for maintaining the integrity of electrical connections in high-density electronic assemblies.
Advantages of Laser Drilling in the Electronics Industry:
- High Precision and Accuracy: Laser drilling offers exceptional precision, allowing for the creation of small, high-quality holes with tight tolerances, which are essential in electronics manufacturing.
- Minimal Thermal Impact: The focused laser beam minimizes the heat-affected zone, reducing the risk of thermal distortion or damage to sensitive electronic components and materials.
- Versatility Across Materials: Laser drilling can be applied to a wide range of materials used in the electronics industry, including metals, polymers, ceramics, and composites, making it a versatile solution for various applications.
- Clean and Contaminant-Free Process: Laser drilling produces minimal debris and does not require the use of chemicals or abrasives, making it a clean and environmentally friendly process suitable for the stringent cleanliness standards in electronics manufacturing.
- Speed and Efficiency: Laser drilling is a fast and efficient process that can handle high-volume production while maintaining consistent quality, reducing lead times for electronics manufacturing.
Use Cases in Automation:
Automated laser drilling systems are increasingly used in the electronics industry to enhance production efficiency and ensure consistent quality. These systems can be integrated with precision positioning systems and robotics to perform complex drilling tasks with high repeatability. Automation allows for continuous operation, reducing cycle times and increasing throughput, which is essential for meeting the high demand in electronics manufacturing.
In summary, laser drilling is a vital technology in the electronics industry, offering the precision, cleanliness, and versatility needed to manufacture high-quality electronic components and devices. Its ability to produce precise, small-diameter holes with minimal thermal impact makes it an indispensable tool for advancing electronics technology and improving product performance.
OVERVIEW
Laser cleaning is an advanced, non-contact technology used in the electronics industry to remove contaminants, oxides, residues, and other unwanted materials from the surfaces of electronic components, PCBs, and semiconductor wafers. This process utilizes a highly focused laser beam to ablate or vaporize contaminants without damaging the underlying material. Laser cleaning is particularly valued for its precision, efficiency, and ability to clean delicate and intricate parts without the use of chemicals or abrasive methods. This makes it an ideal solution for maintaining the cleanliness and performance of electronic devices.
APPLICATIONS
Surface Preparation of PCBs:
- Application: Laser cleaning is used to prepare the surfaces of printed circuit boards (PCBs) before soldering or coating. This process removes oxides, dust, and residues that could interfere with the electrical connections or the adhesion of coatings.
- Benefit: Ensures a clean and contamination-free surface, improving the reliability and quality of solder joints and coatings, which is critical for the performance of electronic devices.
Removal of Oxides from Semiconductor Wafers:
- Application: Laser cleaning is employed to remove oxides and thin layers of contaminants from semiconductor wafers during the manufacturing process. This is crucial for maintaining the integrity of the wafer surface and ensuring the proper function of the semiconductor components.
- Benefit: Provides precise and controlled removal of contaminants, ensuring that the wafers meet stringent cleanliness standards, which is essential for high-performance semiconductor devices.
Cleaning of Delicate Components:
- Application: Laser cleaning is ideal for cleaning delicate and intricate electronic components, such as connectors, contacts, and microchips. The process removes residues and contaminants without causing physical damage or altering the properties of the components.
- Benefit: Preserves the functionality and integrity of sensitive electronic components, ensuring they perform reliably in their applications.
Deposition Mask Cleaning:
- Application: In the electronics industry, masks used for deposition processes can accumulate contaminants that affect the quality of the deposition. Laser cleaning is used to remove these contaminants without damaging the mask, allowing for consistent, high-quality deposition processes.
- Benefit: Extends the life of deposition masks and ensures consistent process quality, reducing the risk of defects in the manufactured electronic devices.
Restoration of Electronic Equipment:
- Application: Laser cleaning is utilized to restore electronic equipment by removing corrosion, oxidation, and accumulated residues from surfaces and contacts. This is particularly useful for maintaining or refurbishing older equipment.
- Benefit: Revives the performance of electronic equipment by ensuring that all contact points and surfaces are clean and free from contaminants, extending the equipment’s operational life.
Preparation for Wire Bonding:
- Application: Laser cleaning is used to prepare the surfaces of semiconductor devices and substrates before wire bonding. This ensures that the bonding surfaces are free from contaminants that could affect the bond strength and reliability.
- Benefit: Improves the quality and strength of wire bonds, which is crucial for the durability and performance of electronic assemblies.
Advantages of Laser Cleaning in the Electronics Industry:
- Non-Destructive Cleaning: Laser cleaning is a non-contact process that effectively removes contaminants without causing any physical damage to the underlying material, preserving the integrity of delicate electronic components.
- Precision and Control: Laser cleaning allows for highly precise and controlled cleaning, which is essential for maintaining the quality and performance of intricate electronic devices.
- Chemical-Free Process: Laser cleaning does not require the use of harsh chemicals or solvents, making it an environmentally friendly and safe option for cleaning electronic components, with minimal risk of introducing contaminants.
- Versatility Across Materials: Laser cleaning can be applied to a wide range of materials used in electronics, including metals, ceramics, and polymers, making it a versatile solution for various cleaning needs.
- Efficiency and Speed: Laser cleaning is a fast and efficient process that can be easily integrated into manufacturing and maintenance routines, reducing downtime and increasing productivity.
Use Cases in Automation:
Automated laser cleaning systems are increasingly being adopted in the electronics industry to enhance cleaning efficiency and ensure consistent quality. These systems can be integrated into production lines or cleanroom environments to perform high-precision cleaning tasks with minimal human intervention. Automation allows for continuous operation, reducing cleaning times and improving throughput while maintaining the stringent cleanliness standards required in the electronics industry.
In summary, laser cleaning is a critical technology in the electronics industry, offering a precise, non-destructive, and environmentally friendly solution for maintaining the cleanliness and performance of electronic components and devices. Its ability to remove contaminants without damaging delicate components makes it an essential tool for ensuring the reliability and longevity of electronic products.
DEDICATED TO INNOVATION
At Scantech Laser, our commitment to the electronics industry extends beyond just meeting customer needs; it’s about driving innovation and shaping the future of electronics manufacturing. Acknowledging the critical role the electronics sector plays in advancing global technology, we are focused on delivering tailored laser solutions that address the unique challenges and opportunities within the industry. Whether it’s enabling precision cutting for microelectronics, improving efficiency with high-accuracy marking, or enhancing the production of delicate components, our focus is on propelling the electronics industry forward with advanced laser technology.
Elevating Electronics Manufacturing with Laser Precision
In the dynamic electronics industry, precision, speed, and reliability are crucial. Scantech Laser’s advanced laser technologies are expertly designed to meet these essential requirements, providing solutions that significantly enhance the efficiency and quality of electronics production processes. From laser cutting and welding to marking and drilling, our state-of-the-art systems deliver unmatched precision and consistency. This ensures that every electronic component produced meets the highest standards of quality, optimizing performance and reliability in the rapidly evolving electronics sector.
Driving Electronics Innovation with Laser Solutions
Our approach to the electronics industry enables us to envision its long-term future while focusing on current growth and development needs. Whether it’s optimizing component design through advanced laser cutting techniques, enhancing product reliability with precise laser welding, or improving traceability with durable laser marking, Scantech Laser’s solutions are at the forefront of electronics innovation.
Advancing the Electronics Industry with Laser Solutions
As the electronics industry continues to evolve, Scantech Laser remains committed to supporting its growth with innovative, reliable, and efficient laser solutions. We are dedicated to understanding the industry’s unique challenges and providing the technologies that will drive its success in the years to come. Together, we’re not just meeting the needs of today; we’re propelling the electronics industry into the future.