SCANTECH IN MACHINE TOOLS
In the machine tools industry, laser technology has become a fundamental tool for enhancing precision, efficiency, and versatility in the manufacturing process. Lasers offer advanced solutions for cutting, welding, marking, and hardening of various machine tool components. This technology enables manufacturers to achieve high precision and quality, essential for the production of complex and durable machine parts.
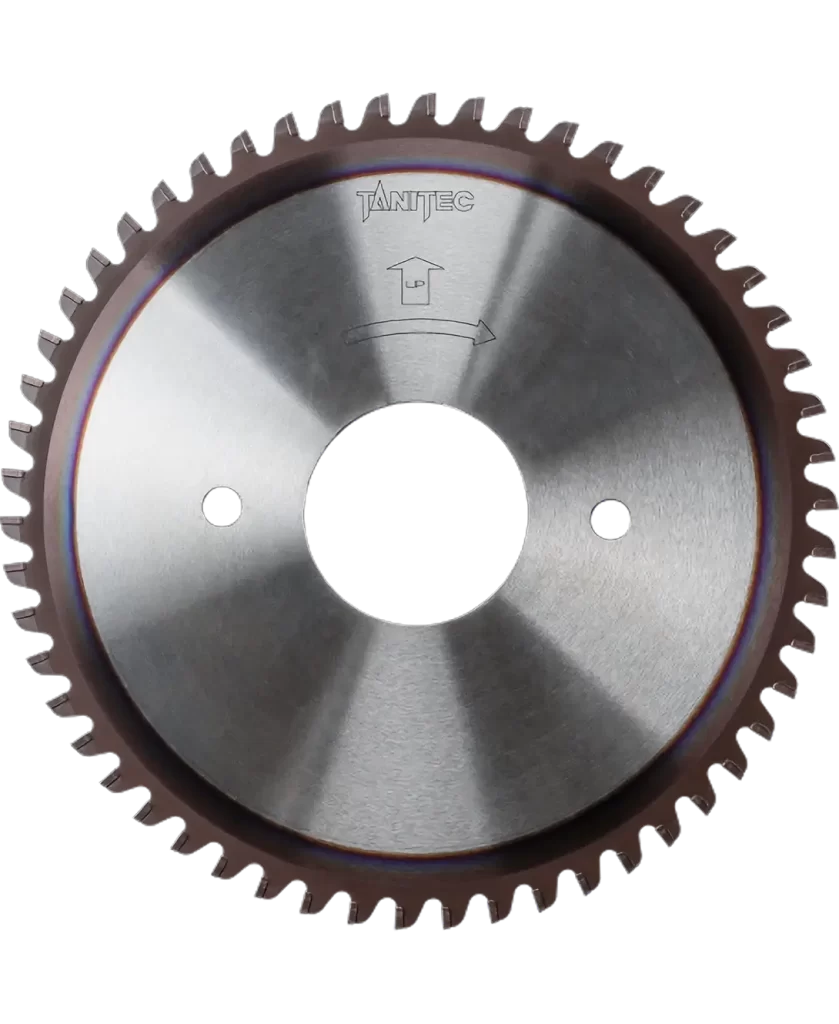
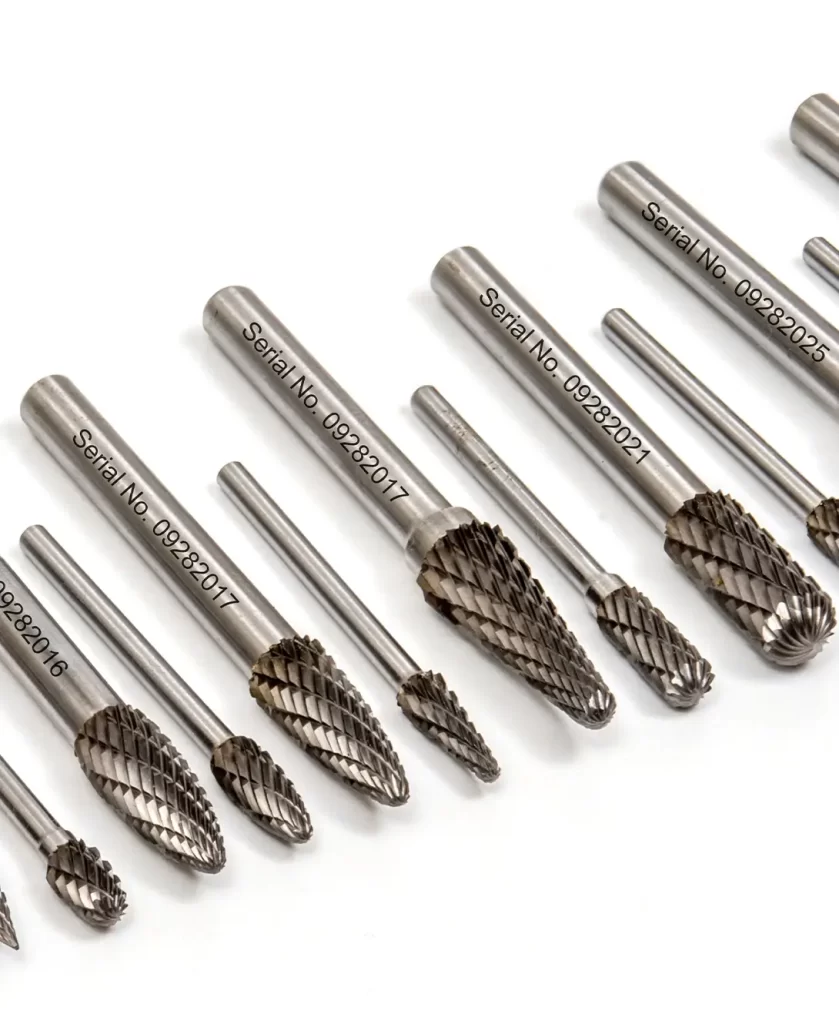
MACHINE TOOLS APPLICATIONS
OVERVIEW
Laser welding has become an essential technology in the machine tools industry, providing precision, strength, and versatility in the joining of components and the repair of machine parts. This non-contact process uses a highly focused laser beam to fuse materials with minimal heat input, resulting in strong, high-quality welds with minimal distortion. Laser welding is particularly valued in the machine tools industry for its ability to weld complex geometries, join dissimilar materials, and perform highly precise repairs, all while maintaining the structural integrity of the components.
APPLICATIONS
Precision Component Welding:
- Application: Laser welding is used to join precision components in machine tools, such as gears, shafts, and housings. The precision of laser welding ensures that the components are securely joined with minimal thermal distortion, which is crucial for maintaining tight tolerances in machine tool assemblies.
- Benefit: Provides strong, durable welds that enhance the reliability and performance of machine tools, ensuring that they operate efficiently and accurately.
Welding of Dissimilar Metals:
- Application: Laser welding is ideal for joining dissimilar metals that are often used in machine tool construction, such as stainless steel to aluminum or copper to steel. The ability to precisely control the heat input allows for successful welding without compromising the properties of the base materials.
- Benefit: Enables the combination of different materials to optimize the performance and cost-effectiveness of machine tool components, leading to more innovative and efficient designs.
Repair and Refurbishment of Machine Parts:
- Application: Laser welding is commonly used to repair and refurbish worn or damaged machine parts, such as turbine blades, mold tools, and cutting tools. The laser can precisely add material to worn areas or fill cracks without affecting the surrounding material.
- Benefit: Extends the life of expensive machine parts, reduces downtime, and lowers maintenance costs by allowing for high-quality repairs that restore the parts to their original specifications.
Micro-Welding for Small Components:
- Application: Laser micro-welding is used for assembling and repairing small, delicate components in machine tools, such as sensors, micro-actuators, and electronic housings. The laser’s precision allows for welding at a microscopic level, where traditional welding methods may not be feasible.
- Benefit: Ensures the integrity and functionality of small components, which are critical for the overall performance of modern, high-precision machine tools.
Joining of Hard-to-Weld Materials:
- Application: Laser welding is effective for welding hard-to-weld materials such as high-strength alloys, tool steels, and heat-resistant superalloys, which are commonly used in the machine tools industry.
- Benefit: Allows for the creation of robust machine components that can withstand extreme operating conditions, enhancing the durability and performance of machine tools.
Automated Welding Systems:
- Application: In high-volume production settings, laser welding is integrated into automated systems for the mass production of machine tool components. Robots equipped with laser welding heads can perform precise and repeatable welds, increasing productivity and reducing labor costs.
- Benefit: Improves production efficiency and consistency, ensuring that each component meets stringent quality standards while reducing production time and costs.
Advantages of Laser Welding in the Machine Tools Industry:
- High Precision and Control: Laser welding offers exceptional precision, making it ideal for applications that require tight tolerances and minimal distortion, which are critical in the manufacturing of machine tools.
- Minimal Heat-Affected Zone: The focused laser beam minimizes the heat-affected zone, reducing the risk of warping or altering the properties of the base materials, especially important for high-precision components.
- Versatility: Laser welding can be applied to a wide range of materials and component sizes, from large structural parts to small, delicate pieces, making it a versatile tool for various applications in the machine tools industry.
- Strong and Reliable Welds: The high-quality welds produced by laser welding enhance the structural integrity and longevity of machine tool components, ensuring reliable operation even under demanding conditions.
- Automation Compatibility: Laser welding is highly compatible with automation, allowing for the integration of robotic welding systems that can improve productivity and ensure consistent quality in high-volume manufacturing.
Use Cases in Automation:
Automated laser welding systems are widely used in the machine tools industry to enhance production efficiency and consistency. These systems can be programmed to perform complex welds on a variety of components with high precision, reducing the need for manual intervention and ensuring repeatable, high-quality results. Automation also allows for the seamless integration of laser welding into existing manufacturing processes, further optimizing production workflows.
In summary, laser welding is a critical technology in the machine tools industry, offering the precision, versatility, and strength needed to manufacture and repair high-performance machine tool components. Its ability to handle a wide range of materials and applications, coupled with its compatibility with automation, makes laser welding an indispensable tool for modern machine tool manufacturing and maintenance.
OVERVIEW
Laser cutting is a highly precise and efficient technology that has become integral to the machine tools industry. This non-contact process uses a focused laser beam to cut through a wide range of materials, including metals, plastics, and composites, with exceptional accuracy. Laser cutting is particularly valued in the machine tools industry for its ability to produce intricate shapes, fine details, and clean edges, all while minimizing material waste and reducing the need for secondary finishing processes. The versatility and precision of laser cutting make it an essential tool for both the manufacturing and maintenance of machine tools.
APPLICATIONS
Manufacturing of Machine Tool Components:
- Application: Laser cutting is used to fabricate precision components for machine tools, such as gears, brackets, housings, and panels. The laser’s precision allows for the production of complex geometries and intricate designs that are essential for high-performance machine tools.
- Benefit: Provides highly accurate cuts with tight tolerances, ensuring that each component meets the exact specifications required for reliable and efficient machine operation.
Sheet Metal Fabrication:
- Application: Laser cutting is widely employed in the fabrication of sheet metal parts used in machine tools, including covers, enclosures, and mounting plates. The ability to cut through various thicknesses of metal with ease makes laser cutting ideal for creating both lightweight and durable components.
- Benefit: Delivers clean, precise cuts with minimal burrs, reducing the need for post-processing and ensuring a high-quality finish that meets industrial standards.
Cutting of Hard-to-Machine Materials:
- Application: Laser cutting is effective for processing hard-to-machine materials commonly used in machine tools, such as stainless steel, titanium, and hardened alloys. These materials are often challenging to cut with traditional methods but can be precisely cut with laser technology.
- Benefit: Enables the efficient production of parts from tough materials without compromising the material properties, which is crucial for the durability and performance of machine tools.
Prototyping and Customization:
- Application: Laser cutting is used for rapid prototyping and the customization of machine tool components. This allows manufacturers to quickly test and refine designs before moving to full-scale production, as well as to produce customized parts tailored to specific needs.
- Benefit: Reduces development time and costs, allowing for faster iteration of designs and the ability to meet specific customer requirements with precision and flexibility.
Repair and Maintenance of Machine Tools:
- Application: Laser cutting is also used in the repair and maintenance of machine tools, particularly for cutting replacement parts or modifying existing components. This is essential for extending the life of machine tools and maintaining their operational efficiency.
- Benefit: Allows for the precise and efficient production of replacement parts, reducing downtime and ensuring that machine tools continue to operate at peak performance.
Creating High-Precision Cutting Tools:
- Application: Laser cutting is employed in the manufacturing of cutting tools, such as saw blades, drill bits, and milling cutters. The laser can create fine tooth patterns and intricate shapes that are required for high-precision cutting tools.
- Benefit: Ensures that cutting tools have sharp, durable edges that enhance their performance and longevity in machining operations.
Advantages of Laser Cutting in the Machine Tools Industry:
- High Precision and Accuracy: Laser cutting offers exceptional precision, allowing for the creation of complex and intricate designs with tight tolerances, which are essential in the machine tools industry.
- Versatility: Laser cutting can be applied to a wide range of materials, from metals to composites, making it a versatile solution for various machine tool components and applications.
- Efficiency and Speed: Laser cutting is a fast process that can handle high-volume production with consistent quality, reducing lead times and increasing overall production efficiency.
- Minimal Material Waste: The precision of laser cutting minimizes material waste, making it a cost-effective solution that maximizes the use of raw materials.
- Clean Edges and Reduced Post-Processing: Laser cutting produces clean edges with minimal burrs, reducing the need for additional finishing processes and ensuring that parts are ready for assembly or use immediately after cutting.
Use Cases in Automation:
Automated laser cutting systems are widely used in the machine tools industry to enhance production efficiency and ensure consistent quality. These systems can be integrated with CAD/CAM software to automate the cutting process, allowing for precise and repeatable production of complex parts. Automation also enables the continuous operation of laser cutting systems, increasing throughput and reducing the need for manual intervention.
In summary, laser cutting is a critical technology in the machine tools industry, offering the precision, versatility, and efficiency needed to manufacture high-quality components and tools. Its ability to handle a wide range of materials and complex designs makes it an indispensable tool for modern machine tool manufacturing and maintenance, helping to drive innovation and improve productivity across the industry.
OVERVIEW
Laser marking has become an essential technology in the machine tools industry, providing a reliable and precise method for applying critical information directly onto machine components and tools. This non-contact process uses a focused laser beam to create permanent marks, such as serial numbers, barcodes, logos, and other identifiers, on various materials including metals, plastics, and composites. Laser marking is highly valued in the machine tools industry for its ability to produce durable, legible marks that are resistant to wear, heat, and corrosion, ensuring that important information remains visible throughout the lifespan of the tool or component.
APPLICATIONS
Serial Number and Part Identification:
- Application: Laser marking is used to engrave serial numbers, part numbers, and other identifiers on machine tool components. This ensures that each part can be accurately identified and traced throughout its lifecycle, which is critical for quality control and inventory management.
- Benefit: Provides a permanent, tamper-proof mark that enhances traceability and accountability in the manufacturing process, helping to prevent errors and improve overall efficiency.
Branding and Logo Marking:
- Application: Manufacturers use laser marking to apply logos, brand names, and other branding elements onto machine tools and components. This not only reinforces brand identity but also serves as a mark of quality and authenticity.
- Benefit: Creates high-contrast, aesthetically pleasing marks that remain legible and visually appealing, even under harsh operating conditions.
Barcode and QR Code Marking:
- Application: Laser marking is employed to create barcodes, QR codes, and data matrix codes on machine tool components. These codes can be scanned for quick and accurate data retrieval, which is essential for tracking parts in automated production environments.
- Benefit: Ensures that machine tools and parts can be efficiently tracked and managed in real-time, reducing downtime and improving supply chain transparency.
Marking for Quality Assurance and Compliance:
- Application: Laser marking is used to apply quality assurance marks, certification symbols, and compliance information directly onto machine tools and components. This is crucial for meeting industry standards and regulatory requirements.
- Benefit: Provides a clear and permanent record of compliance, helping manufacturers avoid costly fines and ensuring that products meet required specifications.
Tool Identification and Customization:
- Application: Machine tools and cutting tools are often laser-marked with identification codes, sizes, and material specifications to ensure proper usage and tool management. Custom markings can also be applied for specific client needs or unique tool requirements.
- Benefit: Enhances tool management and ensures that the correct tool is used for the right application, reducing the risk of errors and improving machining accuracy.
Durable Surface Marking for Harsh Environments:
- Application: In environments where tools and components are exposed to extreme conditions, such as high temperatures or corrosive substances, laser marking is used to create durable marks that withstand these conditions without degrading.
- Benefit: Ensures that critical information remains legible throughout the tool’s life, even in the most demanding industrial environments, contributing to better maintenance and operational efficiency.
Advantages of Laser Marking in the Machine Tools Industry:
- Permanence and Durability: Laser marking produces permanent marks that are resistant to wear, corrosion, and heat, ensuring that important information remains visible and legible throughout the life of the tool or component.
- High Precision and Clarity: The precision of laser marking allows for the creation of detailed and high-resolution marks, including small text and intricate logos, ensuring that all markings are clear and easy to read.
- Non-Contact Process: As a non-contact method, laser marking does not physically alter or damage the material being marked, preserving the integrity of the component or tool.
- Versatility Across Materials: Laser marking can be applied to a wide variety of materials, including metals, plastics, ceramics, and composites, making it a versatile solution for the diverse range of materials used in the machine tools industry.
- Eco-Friendly and Clean: Laser marking does not require inks, chemicals, or other consumables, making it an environmentally friendly option that generates minimal waste.
Use Cases in Automation:
Automated laser marking systems are increasingly used in the machine tools industry to enhance productivity and ensure consistent quality. These systems can be integrated into production lines, where they perform high-speed marking tasks with precision and repeatability. Automated systems can also be linked with databases to automatically generate and apply unique serial numbers or codes, streamlining the process and reducing the risk of human error.
In summary, laser marking is a vital technology in the machine tools industry, offering the precision, durability, and versatility needed to mark tools and components with critical information. Its ability to produce permanent, high-quality marks that withstand harsh environments makes it an indispensable tool for ensuring traceability, quality control, and brand integrity in the manufacturing process.
OVERVIEW
Laser drilling is a high-precision technology used extensively in the machine tools industry to create small, accurate holes in a wide range of materials, including metals, ceramics, and composites. This non-contact process uses a focused laser beam to vaporize material, allowing for the creation of holes with high precision and minimal thermal impact on the surrounding area. Laser drilling is particularly valued in the machine tools industry for its ability to produce consistent, high-quality holes in complex components, contributing to the manufacturing of high-performance tools and parts.
APPLICATIONS
Micro-Hole Drilling for Precision Components:
- Application: Laser drilling is used to create micro-holes in precision components such as fuel injectors, turbine blades, and cooling channels in high-performance tools. The process ensures that each hole is drilled with exacting precision, meeting the tight tolerances required for optimal performance.
- Benefit: Provides consistent, accurate hole sizes that are critical for the functionality and efficiency of precision components, enhancing overall tool performance.
High-Aspect-Ratio Hole Drilling:
- Application: Laser drilling is ideal for producing high-aspect-ratio holes, where the depth of the hole is much greater than its diameter. This is particularly useful in the manufacturing of components like nozzles, where deep, narrow holes are required.
- Benefit: Enables the creation of deep, narrow holes with minimal taper, ensuring that the holes meet the precise specifications needed for specific industrial applications.
Drilling of Hard and Brittle Materials:
- Application: Laser drilling is used to drill hard and brittle materials such as ceramics, tungsten carbide, and superalloys, which are commonly used in the machine tools industry. These materials are often difficult to machine with traditional methods but can be efficiently drilled using lasers.
- Benefit: Allows for the precise and controlled drilling of hard-to-machine materials, reducing the risk of cracking or damage and ensuring the integrity of the component.
Cooling Hole Drilling in Cutting Tools:
- Application: Laser drilling is employed to create cooling holes in cutting tools, such as drills, end mills, and saw blades. These holes allow for the efficient removal of heat during operation, extending the life of the tool and improving cutting performance.
- Benefit: Enhances the thermal management of cutting tools, reducing wear and tear, and improving overall tool efficiency and longevity.
Hole Drilling for Fasteners and Connectors:
- Application: Laser drilling is used to create precise holes for fasteners, connectors, and other assembly components in machine tools. The accuracy of laser drilling ensures that these holes align perfectly with corresponding parts, facilitating easy assembly and secure connections.
- Benefit: Ensures a high level of precision in the drilling of holes for fasteners, reducing the risk of misalignment and improving the structural integrity of assembled components.
Blind Hole Drilling:
- Application: Laser drilling is used to create blind holes, where the hole does not go all the way through the material. This is particularly useful in applications where a controlled depth is required, such as in the manufacturing of molds or dies.
- Benefit: Provides precise control over hole depth, ensuring that blind holes are drilled to exact specifications without damaging the surrounding material.
Advantages of Laser Drilling in the Machine Tools Industry:
- Precision and Accuracy: Laser drilling offers exceptional precision, allowing for the creation of small, high-quality holes with tight tolerances, which are essential in high-performance machine components.
- Minimal Thermal Impact: The focused laser beam minimizes the heat-affected zone, reducing the risk of thermal distortion or damage to the surrounding material, which is especially important when drilling delicate or heat-sensitive components.
- Versatility: Laser drilling can be applied to a wide range of materials, including metals, ceramics, and composites, making it a versatile solution for various drilling needs in the machine tools industry.
- Speed and Efficiency: Laser drilling is a fast process that can produce high volumes of precisely drilled holes in a short amount of time, improving production efficiency and reducing lead times.
- Clean and Consistent Results: Laser drilling produces holes with smooth edges and minimal debris, reducing the need for secondary finishing processes and ensuring that the components are ready for immediate use.
Use Cases in Automation:
Automated laser drilling systems are widely used in the machine tools industry to enhance production efficiency and consistency. These systems can be programmed to drill multiple holes with high precision and repeatability, ensuring uniformity across large production runs. Automation also allows for the integration of laser drilling into complex manufacturing workflows, where multiple drilling operations can be performed in sequence, reducing manual intervention and increasing overall productivity.
In summary, laser drilling is a critical technology in the machine tools industry, offering the precision, versatility, and efficiency needed to produce high-quality holes in a variety of materials and components. Its ability to handle complex drilling tasks with minimal thermal impact makes it an indispensable tool for modern machine tool manufacturing and maintenance, helping to drive innovation and improve performance across the industry.
OVERVIEW
Laser cleaning is a modern and highly efficient technology used in the machine tools industry for removing contaminants, oxides, rust, and other unwanted materials from surfaces. This non-contact process uses a focused laser beam to ablate surface layers, leaving the underlying material clean and intact. Laser cleaning is particularly valued in the machine tools industry for its precision, eco-friendliness, and ability to clean without damaging the substrate. It is an ideal solution for maintaining the performance and longevity of machine tools and components by ensuring they remain free of contaminants that could affect their operation.
APPLICATIONS
Rust and Oxide Removal:
- Application: Laser cleaning is used to remove rust, oxidation, and other surface contaminants from metal components and machine parts. This is crucial for restoring and maintaining the functionality of machine tools, especially those exposed to corrosive environments.
- Benefit: Provides a clean, oxide-free surface that improves the performance and lifespan of machine tools, ensuring they operate efficiently and reliably.
Pre-Welding and Pre-Coating Preparation:
- Application: Before welding or coating machine tool components, laser cleaning is used to remove oils, grease, and other contaminants that could interfere with the quality of the weld or coating. This ensures that the surface is perfectly clean and ready for the next processing step.
- Benefit: Enhances the quality of welds and coatings by providing a clean surface, leading to stronger bonds and better adhesion, which are critical for the durability of machine tools.
Precision Cleaning of Delicate Components:
- Application: Laser cleaning is ideal for precision cleaning of small, delicate machine tool components, such as bearings, gears, and sensors, where traditional cleaning methods might be too abrasive or imprecise.
- Benefit: Ensures that delicate components are thoroughly cleaned without the risk of damage, maintaining their precision and functionality.
Mold and Die Cleaning:
- Application: In the machine tools industry, laser cleaning is used to clean molds and dies, removing residues such as polymers, rubber, and other materials that can accumulate during manufacturing processes.
- Benefit: Extends the lifespan of molds and dies by removing buildup without causing wear or damage, ensuring that they continue to produce high-quality parts.
Surface Preparation for Adhesive Bonding:
- Application: Laser cleaning is employed to prepare surfaces for adhesive bonding by removing contaminants that could weaken the bond. This is particularly important in the assembly of machine tools, where strong, reliable bonds are required.
- Benefit: Improves the strength and reliability of adhesive bonds by ensuring that surfaces are perfectly clean and ready for bonding, leading to better overall assembly quality.
Maintenance and Restoration of Machine Tools:
- Application: Laser cleaning is used for the maintenance and restoration of machine tools, removing dirt, old coatings, and other contaminants that accumulate over time. This helps in refurbishing and restoring tools to their original condition.
- Benefit: Reduces the need for costly replacements by extending the life of machine tools through effective cleaning and maintenance, improving their performance and reducing downtime.
Advantages of Laser Cleaning in the Machine Tools Industry:
- Non-Destructive Cleaning: Laser cleaning is a non-contact process that removes contaminants without causing any physical or chemical damage to the underlying material, preserving the integrity of the machine tools and components.
- Precision and Control: Laser cleaning allows for precise control over the cleaning process, enabling the removal of specific contaminants from targeted areas without affecting the surrounding material.
- Environmentally Friendly: Laser cleaning is an eco-friendly alternative to traditional cleaning methods, as it does not require the use of chemicals, solvents, or abrasive materials, reducing environmental impact and eliminating hazardous waste.
- Versatility: Laser cleaning can be applied to a wide range of materials, including metals, ceramics, and composites, making it suitable for various cleaning tasks in the machine tools industry.
- Efficiency and Speed: Laser cleaning is a fast and efficient process that can be easily integrated into maintenance routines, reducing downtime and increasing the productivity of machine tools.
Use Cases in Automation:
Automated laser cleaning systems are increasingly used in the machine tools industry to enhance cleaning efficiency and consistency. These systems can be integrated into automated production lines or maintenance setups, where they perform high-speed, precise cleaning tasks with minimal human intervention. Automation allows for continuous operation, ensuring that machine tools and components are cleaned regularly and consistently, thereby maintaining optimal performance.
In summary, laser cleaning is a critical technology in the machine tools industry, offering a precise, efficient, and environmentally friendly solution for removing contaminants and maintaining the cleanliness of machine tools and components. Its ability to clean without damaging the underlying material makes it an essential tool for ensuring the longevity and reliability of machine tools, ultimately contributing to improved productivity and reduced maintenance costs.
OVERVIEW
Laser hardening is an advanced surface treatment technology used in the machine tools industry to enhance the wear resistance, durability, and lifespan of metal components. This process involves using a focused laser beam to rapidly heat the surface of the metal, followed by controlled cooling, which results in a hardened layer. Unlike traditional hardening methods, laser hardening offers precise control over the treatment area, minimizing thermal distortion and maintaining the material’s original properties. This makes laser hardening particularly valuable for extending the life of critical machine tool components subjected to high levels of stress and wear.
APPLICATIONS
Tool Surface Hardening:
- Application: Laser hardening is widely used to harden the surfaces of cutting tools, such as drills, milling cutters, and saw blades. The process enhances the wear resistance of these tools, extending their lifespan and maintaining sharpness over longer periods.
- Benefit: Increases the durability and performance of cutting tools, reducing tool replacement frequency and improving machining efficiency.
Gear and Spline Hardening:
- Application: Laser hardening is employed to selectively harden the teeth of gears and splines in machine tools. This localized hardening improves the wear resistance of the contact surfaces, enhancing the longevity and reliability of the gears under heavy loads.
- Benefit: Provides precise hardening of gear teeth, reducing wear and tear and extending the service life of gears, which is critical for the smooth operation of machine tools.
Bearing Surface Hardening:
- Application: Laser hardening is used to treat the surfaces of bearing races and other rolling elements to improve their wear resistance. This is essential for maintaining the performance and reliability of bearings in high-load, high-speed applications.
- Benefit: Enhances the wear resistance and fatigue life of bearings, reducing maintenance requirements and ensuring consistent performance in demanding environments.
Hardening of Machine Tool Guides and Rails:
- Application: The guideways, rails, and slides of machine tools are often laser hardened to increase their resistance to wear and deformation. This ensures the precision and accuracy of machine tool movements over time.
- Benefit: Improves the longevity and precision of machine tools by reducing wear on critical guide surfaces, maintaining the accuracy of machining processes.
Mold and Die Surface Hardening:
- Application: Laser hardening is used to harden the surfaces of molds and dies, which are subjected to high levels of wear during the forming process. This application is crucial for extending the life of these expensive tools and maintaining the quality of the parts they produce.
- Benefit: Increases the durability of molds and dies, reducing the frequency of costly replacements and ensuring consistent production quality.
Hardening of Hydraulic and Pneumatic Cylinder Rods:
- Application: Laser hardening is applied to the surfaces of hydraulic and pneumatic cylinder rods to improve their wear and corrosion resistance. This is important for maintaining the efficiency and reliability of hydraulic systems in machine tools.
- Benefit: Enhances the surface hardness and durability of cylinder rods, reducing the risk of wear and corrosion, and improving the overall performance of hydraulic systems.
Advantages of Laser Hardening in the Machine Tools Industry:
- Precision and Control: Laser hardening allows for highly precise control over the area to be hardened, enabling selective hardening of specific regions without affecting the entire component. This is particularly useful for complex geometries and areas requiring localized treatment.
- Minimal Distortion: The rapid heating and controlled cooling of laser hardening minimize thermal distortion and reduce the risk of cracking or warping, preserving the dimensional accuracy of the component.
- Consistency and Repeatability: Laser hardening provides consistent and repeatable results, ensuring that each treated component meets the required hardness specifications, which is critical for maintaining the performance of machine tools.
- Versatility Across Materials: Laser hardening can be applied to a wide range of materials commonly used in machine tools, including various steels and cast irons, making it a versatile solution for enhancing wear resistance in different components.
- Reduced Post-Treatment Requirements: The precision of laser hardening often eliminates the need for extensive post-treatment processing, such as grinding or finishing, saving time and reducing production costs.
Use Cases in Automation:
Automated laser hardening systems are increasingly being used in the machine tools industry to improve efficiency and consistency in surface treatment processes. These systems can be integrated into automated production lines, where they perform precise hardening operations on multiple components with high repeatability. Automation allows for the continuous processing of parts, reducing cycle times and ensuring consistent quality across large production runs.
In summary, laser hardening is a vital technology in the machine tools industry, offering a precise, efficient, and effective solution for enhancing the wear resistance and durability of critical components. Its ability to selectively harden specific areas of a part without causing distortion makes it an indispensable tool for modern manufacturing, helping to extend the life of machine tools and improve overall productivity.
OVERVIEW
Laser Additive Manufacturing (LAM), also known as laser-based 3D printing or laser metal deposition (LMD), is an advanced manufacturing technology that has significantly impacted the machine tools industry. This process involves using a laser to melt and fuse powdered or wire-fed material layer by layer, creating highly complex and precise components directly from a digital model. LAM offers the ability to produce parts with intricate geometries, repair damaged components, and customize tools and machine parts, all while reducing material waste and production time.
APPLICATIONS
Production of Complex Components:
- Application: Laser Additive Manufacturing is used to create complex components that are difficult or impossible to produce using traditional manufacturing methods. This includes parts with internal channels, lattice structures, and complex geometries that are critical for advanced machine tool designs.
- Benefit: Enables the production of highly intricate and optimized parts, improving the performance and functionality of machine tools while reducing material usage and weight.
Tool and Die Manufacturing:
- Application: LAM is employed in the production of customized tools, dies, and molds used in machine tools. The technology allows for the rapid prototyping and manufacturing of these components with high precision, enabling quick iterations and design optimizations.
- Benefit: Reduces lead times and costs associated with tooling, while providing the flexibility to create complex and durable tools tailored to specific applications.
Repair and Refurbishment of Machine Components:
- Application: Laser Additive Manufacturing is ideal for repairing and refurbishing worn or damaged machine tool components, such as turbine blades, shafts, and gears. LAM can add material precisely where needed, restoring parts to their original specifications or even enhancing them.
- Benefit: Extends the life of expensive components, reduces downtime, and minimizes the need for replacements, leading to significant cost savings and improved operational efficiency.
Customization and Small Batch Production:
- Application: LAM is used for the customization of machine tool components and the production of small batches of parts. This is particularly useful in situations where unique or specialized parts are required, or where production volumes do not justify the cost of traditional tooling.
- Benefit: Provides the ability to produce custom parts on-demand, reducing inventory costs and enabling rapid response to specific customer needs or market changes.
Hybrid Manufacturing:
- Application: Laser Additive Manufacturing is often combined with traditional subtractive manufacturing methods (such as CNC machining) to create hybrid manufacturing processes. In this approach, LAM is used to build up material or add features, and then CNC machining is used for final finishing.
- Benefit: Combines the advantages of additive and subtractive manufacturing, allowing for greater design flexibility, improved material properties, and more efficient production processes.
Production of Lightweight Structures:
- Application: LAM is employed to produce lightweight structures with optimized material distribution, such as lattice structures and thin-walled components. These parts are used in machine tools where reducing weight is essential for improving performance and energy efficiency.
- Benefit: Reduces the overall weight of machine tool components, leading to increased efficiency, reduced energy consumption, and improved performance in dynamic applications.
Advantages of Laser Additive Manufacturing in the Machine Tools Industry:
- Design Freedom: LAM allows for the creation of highly complex and optimized geometries that are not possible with traditional manufacturing methods, enabling innovative designs that enhance machine tool performance.
- Material Efficiency: The layer-by-layer deposition process minimizes material waste, making LAM a more sustainable manufacturing option, especially when working with expensive materials.
- Rapid Prototyping and Production: LAM enables quick prototyping and short production runs, allowing for faster design iterations and time-to-market for new products and components.
- Customization: LAM offers unparalleled customization capabilities, enabling the production of unique or tailored parts that meet specific requirements without the need for costly tooling changes.
- Enhanced Part Properties: The ability to control material deposition and build direction allows for the production of parts with tailored mechanical properties, such as improved strength, wear resistance, or heat dissipation.
Use Cases in Automation:
Automated laser additive manufacturing systems are increasingly being integrated into production lines in the machine tools industry. These systems can operate continuously, building complex components with minimal human intervention. Automation also allows for the integration of LAM with other manufacturing processes, such as CNC machining or inspection, to create seamless, end-to-end production workflows that maximize efficiency and ensure consistent quality.
In summary, Laser Additive Manufacturing is a transformative technology in the machine tools industry, offering the ability to produce complex, high-performance components with greater design freedom, material efficiency, and speed. Its applications in the production, repair, and customization of machine tool components make it an essential tool for advancing manufacturing capabilities and driving innovation in the industry.
DEDICATED TO INNOVATION
At Scantech Laser, our commitment to the machine tools industry goes beyond merely meeting customer needs; it’s about driving innovation and shaping the future of manufacturing. Recognizing the essential role that the machine tools sector plays in the global economy, we are focused on delivering tailored laser solutions that address the unique challenges and opportunities within this industry. Whether it’s enhancing precision in component fabrication, improving durability with advanced laser welding, or streamlining production processes, our goal is to propel the machine tools industry forward with cutting-edge laser technology.
Enhancing Machine Tools Manufacturing with Laser Precision
In the demanding realm of machine tools manufacturing, precision, speed, and reliability are crucial. Scantech Laser’s cutting-edge laser technologies are expertly designed to meet these challenges, offering solutions that significantly improve the efficiency and quality of machine tool production processes. From laser cutting and welding to marking and drilling, our advanced systems deliver unmatched precision and consistency. This ensures that every component produced meets the highest standards of quality, optimizing performance and reliability in the machine tools industry.
Revolutionizing Machine Tools Manufacturing with Laser Solutions
Our approach to the machine tools industry allows us to envision its long-term future while staying focused on current growth and development needs. Whether it’s enhancing tool precision through advanced laser cutting techniques, increasing durability with precise laser welding, or improving traceability with durable laser marking, Scantech Laser’s solutions are at the forefront of innovation in machine tools manufacturing.
Driving Innovation in Machine Tools with Laser Solutions
As the machine tools industry continues to evolve, Scantech Laser remains committed to supporting its growth with innovative, reliable, and efficient laser solutions. We are dedicated to understanding the industry’s unique challenges and providing the technologies that will drive its success in the years to come. Together, we’re not just meeting the needs of today; we’re propelling the machine tools industry into the future.