SCANTECH IN MEDICAL
Laser technology in the medical industry is pivotal for enabling precise, sterile, and minimally invasive procedures, both in medical device manufacturing and clinical applications. Its high precision and control make it ideal for creating, enhancing, and modifying medical instruments and implants, as well as for surgical interventions. The ability to work with a diverse range of materials, from metals to biocompatible polymers, underscores the versatility of laser technology in advancing medical treatments and patient care.
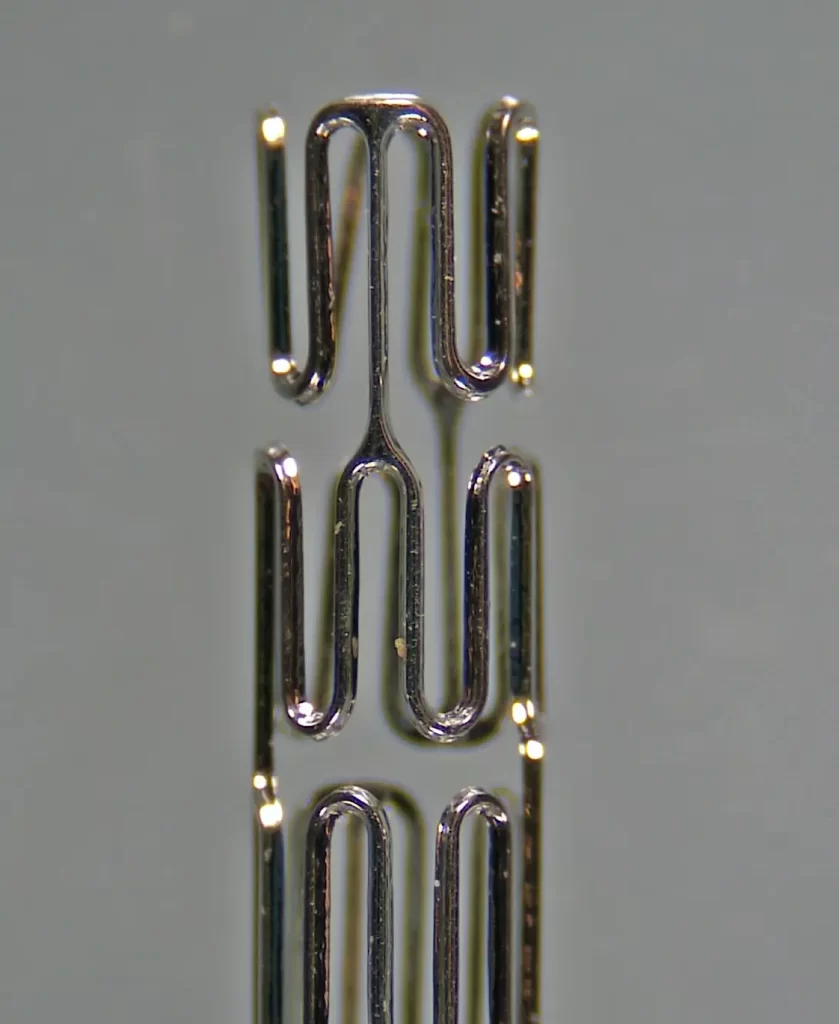
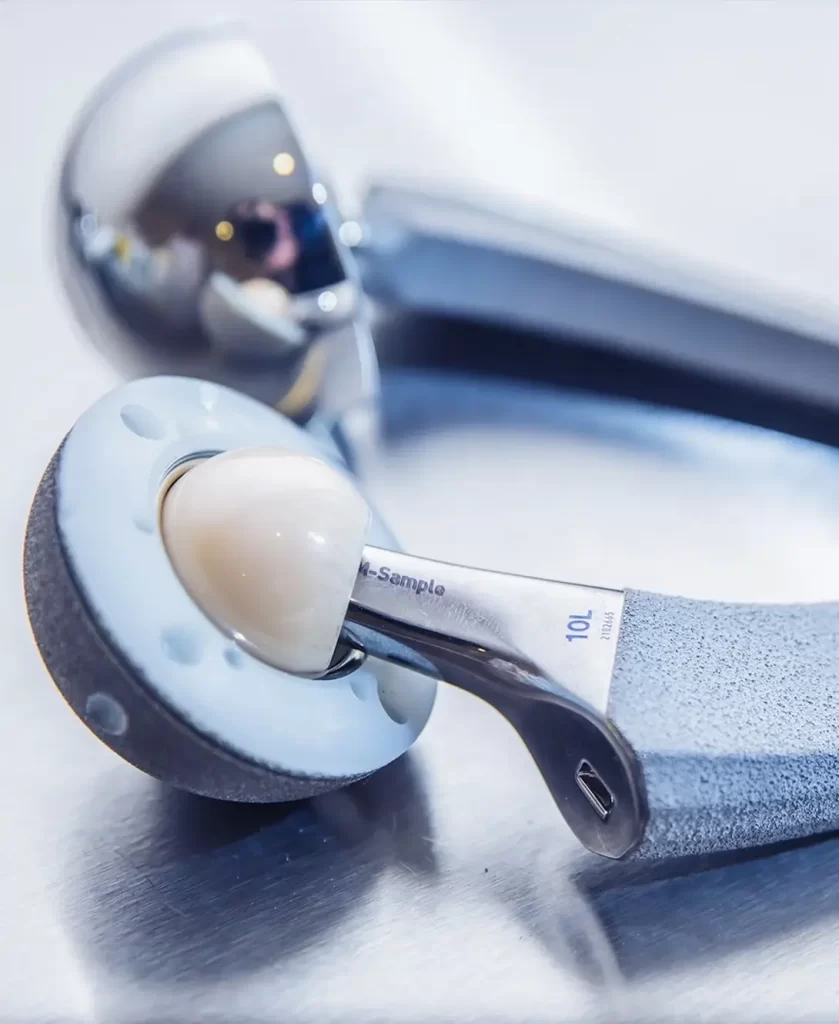
MEDICAL APPLICATIONS
OVERVIEW
Laser welding is a critical technology in the medical industry, offering precision, cleanliness, and the ability to weld delicate and intricate components made from various materials. This non-contact process uses a focused laser beam to fuse materials with minimal heat input, ensuring strong, sterile, and contamination-free welds. Laser welding is particularly valuable in the production of medical devices, implants, and surgical instruments, where precision, biocompatibility, and safety are paramount. The technology is also essential for joining dissimilar materials, which is often required in advanced medical device manufacturing.
APPLICATIONS
Medical Device Manufacturing:
- Application: Laser welding is used to assemble medical devices such as pacemakers, catheter components, stents, and surgical instruments. The precision of laser welding ensures that these devices are assembled to exact specifications, with clean, strong welds that do not compromise the integrity of the device.
- Benefit: Provides reliable, high-quality welds that meet stringent medical industry standards, ensuring the safety and effectiveness of medical devices.
Implantable Devices:
- Application: Laser welding is employed in the fabrication of implantable devices, such as titanium implants, heart valves, and joint replacements. The process allows for the precise joining of materials while maintaining the biocompatibility and strength required for implants.
- Benefit: Ensures that implants are durable, biocompatible, and free from contamination, which is critical for patient safety and long-term success of the implant.
Micro-Welding for Delicate Components:
- Application: Laser welding is ideal for micro-welding applications where tiny, intricate components must be joined with extreme precision, such as in microelectronics for medical devices, guidewires, or sensor assemblies.
- Benefit: Allows for the precise and clean joining of small components without damaging sensitive materials, which is essential for the functionality and reliability of advanced medical devices.
Joining Dissimilar Materials:
- Application: Laser welding is used to join dissimilar materials commonly found in medical devices, such as metals to polymers, or different types of metals. The ability to control heat input precisely makes it possible to create strong, defect-free joints.
- Benefit: Enables the creation of complex medical devices that require the integration of multiple materials, improving device performance and expanding design possibilities.
Sealing of Hermetic Enclosures:
- Application: Laser welding is utilized to seal hermetic enclosures for sensitive electronic components in medical devices, such as implantable sensors and batteries. The airtight seal protects internal components from moisture and other environmental factors.
- Benefit: Ensures the long-term reliability and safety of medical devices by preventing contamination and protecting sensitive electronics.
Surgical Instruments:
- Application: Laser welding is used in the manufacture of surgical instruments, such as forceps, scalpels, and scissors. The process allows for the creation of strong, precise welds on stainless steel and other metals commonly used in surgical tools.
- Benefit: Produces surgical instruments that are durable, easy to sterilize, and capable of withstanding repeated use in demanding surgical environments.
Advantages of Laser Welding in the Medical Industry:
- High Precision and Accuracy: Laser welding offers exceptional precision, which is crucial for assembling small, intricate medical devices and components that must meet exacting standards.
- Minimal Heat-Affected Zone: The focused laser beam minimizes the heat-affected zone, reducing the risk of thermal distortion, warping, or damage to sensitive materials, which is essential for maintaining the integrity of medical devices.
- Sterile and Clean Process: Laser welding is a non-contact process that minimizes contamination risk, making it ideal for applications where sterility is paramount, such as in implantable devices.
- Versatility Across Materials: Laser welding can join a wide range of materials, including metals, polymers, and composites, making it a versatile solution for various medical applications.
- Strong and Reliable Welds: The high-quality welds produced by laser welding enhance the durability and reliability of medical devices, ensuring they perform as intended in critical medical applications.
Use Cases in Automation:
Automated laser welding systems are increasingly used in the medical industry to enhance production efficiency and consistency. These systems can be integrated into cleanroom environments, where they perform precise welding tasks with minimal human intervention. Automation allows for the continuous production of medical devices with high repeatability, reducing the risk of defects and ensuring that each device meets strict quality standards.
In summary, laser welding is a vital technology in the medical industry, offering the precision, cleanliness, and versatility needed to manufacture high-quality medical devices and components. Its ability to produce strong, sterile welds that meet the stringent requirements of the medical field makes it an indispensable tool for advancing medical technology and improving patient outcomes.
OVERVIEW
Laser cutting is a crucial technology in the medical industry, providing unparalleled precision, cleanliness, and efficiency in the production of medical devices, surgical instruments, and implants. This non-contact process uses a highly focused laser beam to cut a wide variety of materials, including metals, polymers, and ceramics, with exceptional accuracy. Laser cutting is particularly valued in the medical field for its ability to produce complex shapes, intricate patterns, and fine details that are essential for the functionality and performance of medical products.
APPLICATIONS
Production of Surgical Instruments:
- Application: Laser cutting is widely used to manufacture surgical instruments such as scalpels, forceps, and scissors. The precision of laser cutting ensures that these instruments have sharp, clean edges, which are essential for effective surgical procedures.
- Benefit: Produces instruments with high precision and sharpness, enhancing their performance and reliability in surgical applications while ensuring they are easy to sterilize.
Manufacturing of Implants:
- Application: Laser cutting is employed to produce intricate components for medical implants, such as stents, orthopedic implants, and dental devices. The ability to cut complex geometries with fine detail is critical for ensuring that implants fit precisely and function correctly.
- Benefit: Enables the production of highly precise and biocompatible implants, improving patient outcomes and reducing the risk of complications.
Cutting of Medical Device Components:
- Application: Laser cutting is used to fabricate components for a wide range of medical devices, including pacemakers, catheter components, and drug delivery systems. The process allows for the precise cutting of materials such as metals, plastics, and composites.
- Benefit: Ensures that medical device components are manufactured to exact specifications, which is critical for their performance and safety in medical applications.
Micro-Machining for Precision Components:
- Application: Laser cutting is ideal for micro-machining small and delicate components used in medical devices, such as microelectromechanical systems (MEMS), microfluidic devices, and sensor assemblies. The precision of laser cutting allows for the creation of tiny features and intricate patterns.
- Benefit: Provides the accuracy needed for micro-scale components, ensuring that they function reliably in complex medical devices.
Cutting of Biocompatible Materials:
- Application: Laser cutting is used to process biocompatible materials such as titanium, cobalt-chrome alloys, and medical-grade polymers. These materials are commonly used in implants and other medical devices that require direct contact with the human body.
- Benefit: Maintains the integrity and biocompatibility of materials during cutting, ensuring that they meet the stringent requirements for use in medical applications.
Creation of Complex Stent Designs:
- Application: Laser cutting is essential in the production of stents, where precise and intricate patterns are cut into tiny metal tubes. These stents must expand and contract without losing structural integrity, making precision cutting crucial.
- Benefit: Allows for the creation of complex, high-precision stents that meet the exacting standards required for cardiovascular and other medical applications.
Advantages of Laser Cutting in the Medical Industry:
- High Precision and Accuracy: Laser cutting provides exceptional precision, enabling the production of complex and intricate designs with tight tolerances, which are critical in medical applications.
- Clean and Sterile Process: Laser cutting is a non-contact process that reduces the risk of contamination, making it ideal for manufacturing sterile medical devices and instruments.
- Versatility Across Materials: Laser cutting can be applied to a wide range of materials used in the medical industry, including metals, polymers, ceramics, and composites, making it a versatile solution for various applications.
- Minimal Thermal Impact: The focused laser beam minimizes the heat-affected zone, reducing the risk of thermal distortion or damage to delicate materials, which is important for maintaining the integrity of medical devices.
- Efficiency and Speed: Laser cutting is a fast and efficient process that can handle high-volume production while maintaining consistent quality, reducing lead times for medical device manufacturing.
Use Cases in Automation:
Automated laser cutting systems are increasingly integrated into the production of medical devices, where they enhance efficiency and ensure consistent quality. These systems can operate in cleanroom environments to meet the stringent cleanliness standards required in the medical industry. Automation also allows for the continuous production of complex components, reducing cycle times and improving overall productivity.
In summary, laser cutting is a vital technology in the medical industry, offering the precision, cleanliness, and versatility needed to manufacture high-quality medical devices, implants, and surgical instruments. Its ability to produce complex shapes and intricate patterns with minimal thermal impact makes it an indispensable tool for advancing medical technology and improving patient care.
OVERVIEW
Laser marking is a crucial technology in the medical industry, offering a precise, clean, and durable method for applying important information directly onto medical devices, surgical instruments, and implants. This non-contact process uses a focused laser beam to create permanent marks, such as serial numbers, barcodes, logos, and other identifiers, on a variety of materials, including metals, plastics, and ceramics. Laser marking is highly valued in the medical field for its ability to produce clear, legible, and durable markings that comply with strict regulatory standards and ensure traceability, safety, and compliance.
APPLICATIONS
Medical Device Identification:
- Application: Laser marking is used to engrave unique identification numbers, batch codes, and manufacturer information onto medical devices, such as pacemakers, catheters, and surgical tools. This ensures traceability and compliance with regulations, such as the FDA’s Unique Device Identification (UDI) system.
- Benefit: Provides a permanent, tamper-proof mark that is essential for tracking devices throughout their lifecycle, improving patient safety and enabling efficient recall management if necessary.
Branding and Logos on Medical Instruments:
- Application: Manufacturers use laser marking to apply logos, brand names, and other branding elements onto medical instruments and devices. This not only reinforces brand identity but also ensures that the instruments are recognized as authentic, high-quality products.
- Benefit: Creates high-contrast, aesthetically pleasing marks that remain legible and visually appealing, even after repeated sterilization and use.
Barcode and QR Code Marking for Inventory Management:
- Application: Laser marking is employed to create barcodes, QR codes, and data matrix codes on medical tools, implants, and packaging. These codes facilitate quick and accurate data retrieval, which is crucial for inventory management, patient records, and supply chain transparency.
- Benefit: Ensures that medical devices and instruments can be efficiently tracked and managed in real-time, enhancing operational efficiency and patient safety.
Sterilization-Resistant Marking:
- Application: Laser marking is used to apply sterilization-resistant marks on surgical instruments and medical tools. These marks must withstand repeated sterilization processes, including autoclaving, without degrading.
- Benefit: Provides durable, long-lasting marks that remain intact and readable even after multiple sterilization cycles, ensuring consistent identification and traceability.
Custom Marking for Patient-Specific Devices:
- Application: Laser marking is employed to customize patient-specific devices, such as custom implants or prosthetics, with relevant patient information or unique identifiers. This ensures that each device is correctly matched to the individual patient.
- Benefit: Enhances patient safety by ensuring that custom devices are correctly identified and matched to the patient, reducing the risk of errors during medical procedures.
Marking on Small and Delicate Components:
- Application: Laser marking is ideal for marking small and delicate components used in medical devices, such as sensors, microelectromechanical systems (MEMS), and tiny implantable devices. The precision of laser marking allows for the creation of clear, detailed marks on even the smallest parts.
- Benefit: Ensures that all components, regardless of size, are accurately marked with necessary information, supporting traceability and quality control in complex medical devices.
Advantages of Laser Marking in the Medical Industry:
- High Precision and Clarity: Laser marking offers exceptional precision, enabling the creation of detailed and high-resolution marks, including small text and intricate logos, which are essential for medical devices.
- Permanent and Durable Marks: The marks produced by laser technology are permanent and resistant to wear, chemicals, and sterilization processes, ensuring that important information remains visible throughout the life of the device.
- Compliance with Regulatory Standards: Laser marking allows manufacturers to comply with strict regulatory requirements, such as the FDA’s UDI system, by providing clear, legible, and durable marks on medical devices.
- Non-Contact Process: As a non-contact method, laser marking does not physically alter or damage the material being marked, preserving the integrity of sensitive medical devices.
- Versatility Across Materials: Laser marking can be applied to a wide variety of materials used in the medical industry, including metals, plastics, ceramics, and composites, making it a versatile solution for various medical applications.
Use Cases in Automation:
Automated laser marking systems are increasingly used in the medical industry to enhance productivity and ensure consistent quality. These systems can be integrated into cleanroom environments, where they perform precise marking tasks with minimal human intervention. Automation allows for the continuous production of marked medical devices, ensuring that each item meets stringent quality standards and regulatory requirements.
In summary, laser marking is a vital technology in the medical industry, offering the precision, durability, and compliance needed to ensure that medical devices, instruments, and implants are correctly identified and traceable. Its ability to produce clear, permanent marks that withstand the rigors of the medical environment makes it an essential tool for advancing medical technology and improving patient care.
OVERVIEW
Laser ablation is a highly precise technology used in the medical industry to remove material from the surface of medical devices and components with minimal thermal impact. This process involves using a focused laser beam to vaporize or remove small amounts of material, creating highly detailed features, fine adjustments, or cleaning surfaces without damaging the underlying material. Laser ablation is particularly valuable in the manufacturing and maintenance of medical devices, where precision, cleanliness, and the ability to work with a variety of materials are essential.
APPLICATIONS
Micro-Patterning of Medical Devices:
- Application: Laser ablation is used to create micro-patterns on the surfaces of medical devices, such as stents, catheters, and implants. These patterns can enhance the performance of the device by improving tissue integration or controlling drug release.
- Benefit: Provides the ability to create intricate, controlled surface patterns that can enhance the functionality of medical devices without compromising their structural integrity.
Surface Texturing for Implants:
- Application: Laser ablation is employed to texture the surfaces of implants, such as orthopedic or dental implants, to promote better osseointegration (the process by which bone tissue integrates with the implant). The laser creates micro-roughness on the implant surface, improving the stability and longevity of the implant.
- Benefit: Enhances the integration of implants with bone or tissue, improving the success rate of implant procedures and patient outcomes.
Deburring and Smoothing of Medical Components:
- Application: Laser ablation is used to remove burrs, rough edges, or unwanted material from medical components, such as small metal parts or polymer-based devices. This process ensures that the components meet the precise specifications required for their application.
- Benefit: Produces smooth, defect-free surfaces on medical components, improving their safety, functionality, and ease of assembly.
Cleaning and Preparation of Medical Device Surfaces:
- Application: Laser ablation is utilized to clean and prepare the surfaces of medical devices before assembly or coating. This includes the removal of contaminants, oxides, or thin films that could interfere with bonding, coating, or other manufacturing processes.
- Benefit: Ensures that medical device surfaces are free from contaminants, leading to improved adhesion of coatings, enhanced device performance, and reduced risk of failure.
Creation of Microfluidic Channels:
- Application: Laser ablation is used to create microfluidic channels in lab-on-a-chip devices and other diagnostic equipment. These channels are critical for guiding fluids through the device for testing, analysis, or drug delivery.
- Benefit: Allows for the precise creation of complex microfluidic systems, enabling the development of advanced diagnostic devices with high accuracy and reliability.
Removing Coatings from Medical Devices:
- Application: Laser ablation is applied to selectively remove coatings or layers from medical devices, such as drug-eluting stents or coated implants, where precise control over the removal process is required.
- Benefit: Provides controlled, selective removal of coatings without damaging the underlying material, ensuring that the device meets the desired specifications and functionality.
Advantages of Laser Ablation in the Medical Industry:
- High Precision and Control: Laser ablation offers exceptional precision, allowing for the removal of very small amounts of material with great accuracy, which is essential for intricate medical device manufacturing.
- Minimal Thermal Impact: The focused laser beam minimizes the heat-affected zone, reducing the risk of thermal damage or distortion to the surrounding material, which is critical for maintaining the integrity of medical devices.
- Versatility Across Materials: Laser ablation can be applied to a wide range of materials used in the medical industry, including metals, polymers, ceramics, and composites, making it a versatile tool for various applications.
- Non-Contact Process: As a non-contact method, laser ablation does not physically stress or damage the material being processed, preserving the structural integrity of delicate medical components.
- Clean and Sterile Process: Laser ablation generates minimal debris and does not require the use of chemicals or solvents, making it an environmentally friendly and clean process that is well-suited to the stringent cleanliness standards of the medical industry.
Use Cases in Automation:
Automated laser ablation systems are increasingly integrated into the production of medical devices, where they enhance efficiency and ensure consistent quality. These systems can be programmed to perform precise ablation tasks on multiple parts in a cleanroom environment, ensuring that each device meets the exacting standards required for medical applications. Automation also allows for the continuous processing of components, reducing cycle times and improving overall productivity.
In summary, laser ablation is a critical technology in the medical industry, offering the precision, cleanliness, and versatility needed for the advanced manufacturing and maintenance of medical devices. Its ability to remove material with minimal thermal impact makes it an essential tool for creating intricate features, improving surface characteristics, and ensuring the high quality and functionality of medical products.
OVERVIEW
Laser drilling is a precise and efficient technology widely used in the medical industry for creating small, accurate holes in a variety of materials. This non-contact process uses a focused laser beam to vaporize or remove material, producing holes with high precision and minimal thermal impact on the surrounding area. Laser drilling is particularly valuable in the manufacturing of medical devices, implants, and diagnostic equipment, where precision and cleanliness are critical. The ability to create micro-holes and complex geometries makes laser drilling an indispensable tool in advancing medical technology.
APPLICATIONS
Micro-Hole Drilling in Medical Devices:
- Application: Laser drilling is used to create micro-holes in components of medical devices, such as catheters, filters, and microfluidic devices. These holes are essential for fluid flow, filtration, and other critical functions in the device.
- Benefit: Provides highly accurate and consistent hole sizes that are crucial for the precise functioning of medical devices, ensuring their reliability and effectiveness.
Precision Drilling for Implants:
- Application: Laser drilling is employed to create precise holes in implants, such as orthopedic screws, dental implants, and hearing aid components. These holes are often used for securing the implant or for allowing the passage of fluids or medication.
- Benefit: Ensures that implants are manufactured to exact specifications, improving their integration with the body and enhancing patient outcomes.
Ventilation and Drug Delivery Holes:
- Application: Laser drilling is used to create ventilation holes in medical devices like inhalers or drug delivery systems. These holes are essential for the controlled release of medication or the proper functioning of the device.
- Benefit: Allows for precise control over hole placement and size, ensuring the proper delivery of medication and the effectiveness of the device.
Creating Holes in Diagnostic Equipment:
- Application: Laser drilling is used in the production of diagnostic equipment, such as lab-on-a-chip devices and blood analysis tools, where micro-holes are necessary for fluid handling and sample analysis.
- Benefit: Enables the creation of complex microfluidic channels and features with high precision, improving the accuracy and reliability of diagnostic tests.
Fabrication of Filters and Meshes:
- Application: Laser drilling is applied to create precise perforations in filters and meshes used in medical devices, such as blood filters, respiratory masks, and dialysis machines. These perforations are critical for the filtering and separation processes.
- Benefit: Provides clean, uniform holes that ensure the effectiveness of filtration and separation processes, which are vital for patient safety and device performance.
Surface Preparation for Enhanced Adhesion:
- Application: Laser drilling can be used to create micro-holes or patterns on the surface of medical components to enhance the adhesion of coatings, adhesives, or other materials. This is particularly useful in the preparation of surfaces for bonding or coating in medical devices.
- Benefit: Improves the bonding strength and durability of coatings and adhesives, ensuring that medical devices perform reliably under various conditions.
Advantages of Laser Drilling in the Medical Industry:
- High Precision and Accuracy: Laser drilling offers exceptional precision, allowing for the creation of small, high-quality holes with tight tolerances, which are essential in medical applications.
- Minimal Thermal Impact: The focused laser beam minimizes the heat-affected zone, reducing the risk of thermal damage or distortion to the surrounding material, which is critical for maintaining the integrity of medical devices.
- Versatility Across Materials: Laser drilling can be applied to a wide range of materials used in the medical industry, including metals, polymers, ceramics, and composites, making it a versatile solution for various applications.
- Non-Contact Process: As a non-contact method, laser drilling does not physically stress or damage the material being processed, preserving the structural integrity of delicate medical components.
- Clean and Contaminant-Free Process: Laser drilling produces minimal debris and does not require the use of chemicals or abrasives, making it a clean process suitable for the stringent cleanliness standards of the medical industry.
Use Cases in Automation:
Automated laser drilling systems are increasingly integrated into the production of medical devices, where they enhance efficiency and ensure consistent quality. These systems can operate in cleanroom environments to meet the stringent cleanliness standards required in the medical industry. Automation also allows for the continuous processing of components, reducing cycle times and improving overall productivity.
In summary, laser drilling is a critical technology in the medical industry, offering the precision, cleanliness, and versatility needed for the advanced manufacturing of medical devices and components. Its ability to create precise, small-diameter holes with minimal thermal impact makes it an indispensable tool for ensuring the high quality and functionality of medical products.
OVERVIEW
Laser cleaning is a highly precise and non-contact technology used in the medical industry for the removal of contaminants, oxides, residues, and other unwanted materials from the surfaces of medical devices, instruments, and components. This method uses a focused laser beam to ablate or vaporize contaminants without damaging the underlying material, making it an ideal solution for maintaining the cleanliness and sterility of medical equipment. Laser cleaning is particularly valued for its ability to clean delicate and intricate parts without the use of harsh chemicals or abrasive methods, ensuring the integrity and functionality of medical devices.
APPLICATIONS
Cleaning of Surgical Instruments and Medical Tools:
- Application: Laser cleaning is used to remove residues, such as blood, tissue, or sterilization chemicals, from surgical instruments and medical tools. This process ensures that the instruments are thoroughly cleaned and ready for sterilization.
- Benefit: Provides a highly effective cleaning solution that preserves the integrity of surgical instruments, ensuring they remain sharp, functional, and free from contaminants.
Preparation of Medical Implants:
- Application: Laser cleaning is employed to prepare the surfaces of medical implants, such as orthopedic screws, dental implants, and cardiovascular stents, by removing any surface oxides or contaminants before coating, bonding, or sterilization.
- Benefit: Ensures that implants are free from contaminants, enhancing the adhesion of coatings and improving biocompatibility, which is crucial for successful implantation.
Cleaning of Medical Device Components:
- Application: Laser cleaning is used to clean and prepare components of medical devices, such as catheters, tubing, and housings, by removing manufacturing residues, oils, or particles that could affect the performance or safety of the device.
- Benefit: Provides a precise and controlled cleaning process that maintains the functionality and reliability of medical devices, ensuring they meet stringent industry standards.
Surface Decontamination of Sterilization Equipment:
- Application: Laser cleaning is utilized to decontaminate surfaces of sterilization equipment, such as autoclaves and sterilization trays, by removing accumulated residues and ensuring that the equipment remains sterile and effective.
- Benefit: Enhances the effectiveness of sterilization processes by ensuring that the equipment used is free from contaminants that could compromise the sterilization cycle.
Preparation of Surfaces for Coating or Bonding:
- Application: Laser cleaning is employed to prepare the surfaces of medical components for coating or bonding by removing contaminants that could interfere with the adhesion process. This is especially important for ensuring the durability and effectiveness of coatings on medical devices.
- Benefit: Improves the quality and longevity of coatings or bonds on medical devices, ensuring that they perform as intended under medical conditions.
Restoration of Delicate Medical Equipment:
- Application: Laser cleaning is used to restore delicate medical equipment, such as endoscopes or diagnostic instruments, by removing buildup or oxidation without damaging sensitive components or coatings.
- Benefit: Extends the life of expensive medical equipment by maintaining its functionality and appearance, reducing the need for frequent replacements.
Advantages of Laser Cleaning in the Medical Industry:
- Non-Destructive Cleaning: Laser cleaning is a non-contact process that effectively removes contaminants without causing any physical damage to the underlying material, preserving the integrity of delicate medical components.
- Precision and Control: Laser cleaning allows for highly precise and controlled cleaning, which is essential for maintaining the quality and performance of intricate medical devices.
- Chemical-Free Process: Laser cleaning does not require the use of harsh chemicals or solvents, making it an environmentally friendly and safe option for cleaning medical equipment, with minimal risk of introducing contaminants.
- Sterile and Clean Process: The process is inherently sterile, as it does not add any foreign materials or residues, ensuring that medical devices remain free from contaminants.
- Versatility Across Materials: Laser cleaning can be applied to a wide range of materials used in the medical industry, including metals, ceramics, and polymers, making it a versatile solution for various cleaning needs.
Use Cases in Automation:
Automated laser cleaning systems are increasingly being adopted in the medical industry to enhance cleaning efficiency and ensure consistent quality. These systems can be integrated into production lines or used in cleanroom environments to perform high-precision cleaning tasks with minimal human intervention. Automation allows for continuous operation, reducing cleaning times and improving throughput while maintaining the stringent cleanliness standards required in the medical field.
In summary, laser cleaning is a critical technology in the medical industry, offering a precise, non-destructive, and environmentally friendly solution for maintaining the cleanliness and sterility of medical devices and equipment. Its ability to remove contaminants without damaging delicate components makes it an essential tool for ensuring the safety, reliability, and longevity of medical products.
OVERVIEW
Laser hardening is a precise and controlled surface treatment process that enhances the hardness and wear resistance of metal components used in medical devices and equipment. This process involves using a focused laser beam to heat the surface of a material rapidly, followed by controlled cooling, resulting in a hardened surface layer with improved mechanical properties. Laser hardening is particularly valuable in the medical industry for extending the lifespan of critical components, ensuring their reliability and performance in demanding environments.
APPLICATIONS
Hardening of Surgical Instrument Edges:
- Application: Laser hardening is used to enhance the edges of surgical instruments, such as scalpels, scissors, and forceps. The process increases the hardness of the cutting edges, making them more resistant to wear and ensuring they remain sharp over extended use.
- Benefit: Extends the lifespan of surgical instruments, reducing the frequency of replacements and maintaining the precision and effectiveness of surgical tools.
Orthopedic Implant Surface Hardening:
- Application: Laser hardening is applied to the surfaces of orthopedic implants, such as joint replacements, screws, and plates. This process improves the wear resistance of the implants, particularly in areas that are subject to high friction and stress.
- Benefit: Enhances the durability of orthopedic implants, reducing the risk of wear-related complications and extending the functional life of the implant.
Dental Tool Hardening:
- Application: Laser hardening is used to treat the surfaces of dental tools, such as drills, probes, and scalers. The process increases the hardness of these tools, making them more resistant to wear and corrosion in the harsh oral environment.
- Benefit: Improves the performance and longevity of dental tools, ensuring consistent results in dental procedures and reducing the need for frequent tool replacement.
Hardening of Wear-Resistant Components in Medical Devices:
- Application: Laser hardening is employed on wear-prone components of medical devices, such as gears, bearings, and shafts in mechanical pumps or surgical robots. This process enhances the wear resistance of these components, ensuring they can withstand continuous operation in medical environments.
- Benefit: Increases the reliability and operational life of critical medical device components, reducing maintenance costs and downtime in healthcare settings.
Surface Hardening for Biocompatible Materials:
- Application: Laser hardening is used on biocompatible metals, such as titanium and stainless steel, which are commonly used in medical implants and devices. The process hardens the surface without compromising the biocompatibility of the material.
- Benefit: Ensures that medical implants and devices are both durable and safe for long-term use in the human body, improving patient outcomes and device longevity.
Precision Hardening of Micro-Components:
- Application: Laser hardening is applied to small, intricate components used in medical devices, such as micro-screws, springs, and connectors. The precision of laser hardening allows for selective treatment of specific areas without affecting the entire component.
- Benefit: Enhances the durability of micro-components, which are essential for the reliable operation of complex medical devices, ensuring they function correctly under various conditions.
Advantages of Laser Hardening in the Medical Industry:
- Precision and Control: Laser hardening offers highly precise control over the area to be hardened, allowing for selective treatment of specific regions without affecting the entire component. This is particularly useful for complex geometries and delicate medical device components.
- Minimal Thermal Distortion: The rapid heating and controlled cooling minimize thermal distortion, preserving the dimensional accuracy of the component and preventing warping or cracking.
- Enhanced Durability: The hardened surface layer significantly increases the wear resistance and lifespan of medical components, reducing the need for frequent replacements and maintenance.
- Compatibility with Biocompatible Materials: Laser hardening can be applied to a wide range of biocompatible materials, ensuring that treated components remain safe for use in medical applications.
- Non-Contact Process: As a non-contact method, laser hardening does not physically alter or stress the material, preserving the integrity of delicate medical components and ensuring consistent results.
Use Cases in Automation:
Automated laser hardening systems are increasingly integrated into the production of medical devices and components, where they enhance efficiency and ensure consistent quality. These systems can be programmed to perform precise hardening operations on multiple parts with high repeatability, reducing human error and increasing productivity. Automation also allows for continuous processing, ensuring that all components meet the stringent quality standards required in the medical industry.
In summary, laser hardening is a critical technology in the medical industry, offering the precision, durability, and reliability needed to enhance the performance and longevity of medical devices and components. Its ability to selectively harden specific areas of a part without causing distortion makes it an indispensable tool for ensuring the high quality and functionality of medical products, ultimately contributing to better patient care and outcomes.
OVERVIEW
Laser Additive Manufacturing (LAM), also known as laser-based 3D printing or selective laser melting (SLM), is an advanced technology that has revolutionized the medical industry. This process involves using a laser to selectively melt and fuse powdered materials layer by layer, creating highly complex and precise components directly from a digital model. LAM is particularly valuable in the medical industry for producing patient-specific implants, complex medical devices, and prototypes with a high degree of accuracy and customization. The ability to produce intricate geometries and use biocompatible materials makes laser additive manufacturing an essential tool for advancing medical technology.
APPLICATIONS
Custom Implants and Prosthetics:
- Application: Laser additive manufacturing is used to produce custom implants, such as cranial, orthopedic, and dental implants, tailored to the specific anatomy of individual patients. The ability to create complex geometries allows for implants that fit perfectly and integrate well with the patient’s body.
- Benefit: Provides highly customized, patient-specific implants that improve surgical outcomes, reduce recovery times, and enhance patient comfort and functionality.
Complex Medical Device Components:
- Application: LAM is employed to manufacture intricate components of medical devices, such as heart valve frames, stent structures, and drug delivery systems. These components often require precise control over geometry and material properties, which LAM can achieve.
- Benefit: Enables the production of high-performance medical devices with complex designs that are difficult or impossible to achieve with traditional manufacturing methods.
Rapid Prototyping for Medical Research and Development:
- Application: Laser additive manufacturing is used for rapid prototyping of medical devices and components, allowing researchers and developers to quickly test and iterate on new designs. This accelerates the development process and brings innovative medical products to market faster.
- Benefit: Reduces development time and costs, enabling faster innovation and improving the ability to respond to emerging medical needs.
Bone and Tissue Scaffolds:
- Application: LAM is used to create bone and tissue scaffolds that support the growth of new tissue in regenerative medicine. These scaffolds are designed with precise porosity and structure to mimic natural bone or tissue, facilitating better integration and healing.
- Benefit: Enhances the effectiveness of regenerative treatments by providing scaffolds that support natural tissue growth and integration, improving patient outcomes.
Manufacturing of Surgical Guides and Templates:
- Application: LAM is employed to produce custom surgical guides and templates that assist surgeons in performing precise and accurate procedures. These guides are often patient-specific, designed based on preoperative imaging data.
- Benefit: Improves the accuracy and safety of surgical procedures by providing tailored guides that ensure precise alignment and positioning during surgery.
Production of Biocompatible Components:
- Application: LAM allows for the production of components made from biocompatible materials such as titanium alloys, cobalt-chrome, and medical-grade polymers. These materials are essential for medical devices that come into contact with the human body, such as implants and wearable devices.
- Benefit: Ensures that medical devices and implants are safe, durable, and compatible with the human body, reducing the risk of adverse reactions and improving the longevity of the products.
Advantages of Laser Additive Manufacturing in the Medical Industry:
- Customization and Personalization: LAM enables the production of patient-specific devices and implants that are tailored to individual anatomical needs, improving the fit, functionality, and comfort of medical products.
- Complex Geometry and Design Freedom: The ability to produce complex geometries and intricate internal structures that are not possible with traditional manufacturing methods allows for the development of innovative medical devices with enhanced performance.
- Material Efficiency and Sustainability: LAM minimizes material waste by using only the material necessary to build the part, making it a more sustainable and cost-effective manufacturing method.
- Rapid Prototyping and Iteration: The ability to quickly produce prototypes allows for faster testing and iteration, accelerating the development process and enabling faster time-to-market for new medical technologies.
- Biocompatibility: LAM can use a wide range of biocompatible materials, ensuring that the final products are safe for use in medical applications and meet the stringent standards required for patient safety.
Use Cases in Automation:
Automated laser additive manufacturing systems are increasingly being integrated into the production of medical devices and implants, where they enhance efficiency and ensure consistent quality. These systems can operate continuously, producing highly detailed and precise components with minimal human intervention. Automation also allows for better control over the manufacturing environment, ensuring that components meet the stringent cleanliness and quality standards required in the medical industry.
In summary, laser additive manufacturing is a transformative technology in the medical industry, offering the ability to produce complex, high-performance components with a high degree of customization and precision. Its applications in custom implants, medical device components, and rapid prototyping make it an essential tool for advancing medical technology and improving patient care.
DEDICATED TO INNOVATION
At Scantech Laser, our commitment to the medical industry goes beyond simply meeting customer needs; it’s about driving innovation and shaping the future of healthcare technology. Recognizing the critical role that the medical sector plays in improving global health, we are focused on delivering tailored laser solutions that address the unique challenges and opportunities within the medical industry. Whether it’s enabling precision in medical device manufacturing, improving patient outcomes with advanced laser treatments, or enhancing the safety and reliability of medical instruments, our goal is to propel the medical industry forward with cutting-edge laser technology.
Advancing Medical Device Manufacturing with Laser Precision
In the critical field of medical device manufacturing, precision, speed, and reliability are paramount. Scantech Laser’s state-of-the-art laser technologies are meticulously crafted to meet these demands, offering solutions that enhance the efficiency and quality of medical production processes. From laser cutting and welding to marking and drilling, our advanced systems deliver unmatched precision and consistency. This ensures that every medical component produced meets the highest standards of quality, supporting the production of reliable and effective medical devices.
Advancing Medical Manufacturing with Laser Precision
Our approach to the medical industry allows us to envision its long-term future while staying focused on current growth and development needs. Whether it’s enhancing device precision through advanced laser cutting techniques, improving safety and durability with precise laser welding, or ensuring product traceability with durable laser marking, Scantech Laser’s solutions are at the forefront of innovation in medical manufacturing.
Transforming the Medical Industry with Laser Solutions
As the medical industry continues to evolve, Scantech Laser remains committed to supporting its growth with innovative, reliable, and efficient laser solutions. We are dedicated to understanding the industry’s unique challenges and providing the technologies that will drive its success in the years to come. Together, we’re not just meeting the needs of today; we’re propelling the medical industry into the future.