SCANTECH IN PACKAGING
In the packaging industry, laser technology has revolutionized the way products are labeled, coded, and cut. Lasers provide a highly precise, efficient, and versatile method for handling various packaging materials, ranging from paper and cardboard to plastics and foils. This technology supports the industry’s needs for speed, accuracy, and sustainability, offering solutions that reduce waste and enhance production workflows.

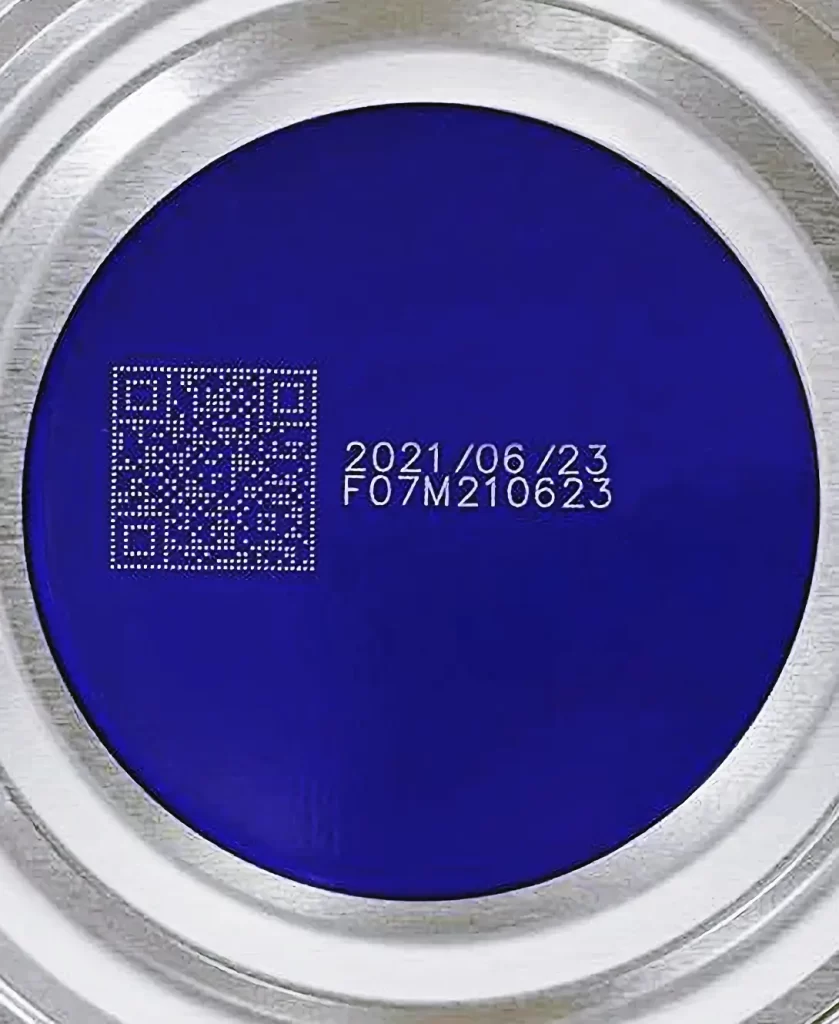
PACKAGING APPLICATIONS
OVERVIEW
Laser welding is increasingly becoming a key technology in the packaging industry, offering precision, speed, and reliability across various applications. As packaging demands become more sophisticated, laser welding provides innovative solutions that enhance the quality, durability, and functionality of packaging materials. Whether it’s sealing, joining, or creating tamper-evident features, laser welding delivers consistent, high-quality results that meet the rigorous standards of modern packaging requirements.
APPLICATIONS
Sealing of Flexible Packaging:
- Application: Laser welding is used to create airtight and secure seals in flexible packaging materials such as pouches, bags, and wrappers. This ensures the integrity and freshness of the packaged products, especially in the food and pharmaceutical industries.
- Benefit: Provides a clean, strong seal that prevents contamination, extends shelf life, and enhances product safety.
Blister Pack Welding:
- Application: In the pharmaceutical and consumer goods industries, laser welding is used to seal blister packs. The precision of laser welding ensures that the blister packs are securely sealed, protecting the contents from environmental factors.
- Benefit: Delivers a tamper-evident seal, enhancing product security and consumer confidence.
Plastic Welding for Rigid Containers:
- Application: Laser welding is employed in joining plastic components of rigid containers, such as caps, closures, and bottles. This method is particularly effective for materials that are difficult to bond using traditional techniques.
- Benefit: Creates strong, leak-proof joints that are aesthetically pleasing and durable, improving the overall quality and functionality of the packaging.
Packaging Film Welding:
- Application: For multi-layered films used in packaging, laser welding is used to join layers together with high precision, ensuring that the final product meets specific mechanical and barrier properties.
- Benefit: Enhances the structural integrity of the packaging, making it suitable for heavy-duty or specialized applications.
Tamper-Evident Seals:
- Application: Laser welding is ideal for creating tamper-evident features in packaging, such as seals that change color or pattern when opened or disturbed.
- Benefit: Improves product security by providing clear evidence of tampering, helping to protect consumers and maintain brand integrity.
Micro-Welding for Delicate Packaging Components:
- Application: In the packaging of delicate or small items, such as electronic components, laser micro-welding is used to join tiny parts with precision without damaging the surrounding material.
- Benefit: Ensures that packaging remains intact and functional, even for the smallest and most sensitive components.
Advantages of Laser Welding in Packaging:
- Precision and Control: Laser welding offers unmatched precision, enabling the creation of high-quality seals and joints that meet exact specifications. This is particularly important in industries like food, pharmaceuticals, and electronics, where the integrity of the packaging is critical.
- Speed and Efficiency: Laser welding is a fast process that can be easily integrated into automated production lines, improving overall manufacturing efficiency and reducing production costs.
- Minimal Thermal Impact: The localized heat generated by laser welding minimizes the risk of damaging heat-sensitive materials, making it ideal for packaging applications that require careful thermal management.
- Versatility: Laser welding can be used with a wide range of packaging materials, including plastics, films, and composites, making it a versatile solution for diverse packaging needs.
- Aesthetic Quality: Laser welding produces clean, smooth seams without the need for additional finishing, ensuring that packaging looks professional and meets consumer expectations.
Use Cases in Automation:
Laser welding systems in the packaging industry are often integrated with automated production lines, where they can perform precise welding tasks at high speeds. Robotic arms or conveyors position packaging materials under laser welding heads, ensuring consistent and accurate welds. Automated inspection systems are frequently employed alongside laser welding to verify the quality of each weld, ensuring that only products meeting strict quality standards proceed to packaging and distribution.
In summary, laser welding offers robust, reliable solutions for the packaging industry, enhancing the quality, security, and functionality of packaging materials across various applications. As the packaging industry continues to evolve, laser welding technology will remain a critical tool in meeting the challenges of modern packaging demands.
overview
Laser cutting has emerged as a transformative technology in the packaging industry, providing unparalleled precision, versatility, and efficiency in the creation of packaging materials. From intricate designs to functional features, laser cutting enables manufacturers to achieve high-quality results that meet the diverse needs of modern packaging. The ability to cut through various materials with extreme accuracy makes laser cutting an essential tool in producing innovative and visually appealing packaging solutions.
APPLICATIONS
Custom Shape Cutting:
- Application: Laser cutting is widely used to create custom shapes and designs in packaging materials, including cardboard, paper, plastics, and films. This is particularly useful for producing unique packaging that stands out on the shelf.
- Benefit: Enables the creation of intricate designs and complex shapes that are difficult to achieve with traditional cutting methods, enhancing brand differentiation and consumer appeal.
Flexible Packaging Conversion:
- Application: In flexible packaging, laser cutting is used to precisely cut and shape materials such as films and foils. This includes creating easy-peel lids and custom shapes for flexible pouches and bags.
- Benefit: Enhances the functionality and aesthetic appeal of flexible packaging, making it more versatile and user-friendly.
Label Cutting:
- Application: Laser cutting is used to create custom labels with intricate designs, precision cuts, and fine details. It is especially beneficial for short-run label production and custom labeling needs.
- Benefit: Provides high accuracy and clean edges, resulting in professional-looking labels that enhance brand presentation and product identification.
Prototyping and Short Runs:
- Application: Laser cutting is ideal for prototyping new packaging designs and producing short runs of custom packaging. This allows companies to quickly test and refine their packaging concepts before full-scale production.
- Benefit: Reduces development time and costs, enabling faster time-to-market for new products and packaging innovations.
Tamper-Evident Features:
- Application: Laser cutting is used to create tamper-evident features such as intricate seals or micro-cuts in packaging materials. These features indicate whether the packaging has been opened or altered.
- Benefit: Enhances product security by providing a clear visual indication of tampering, protecting both the consumer and the brand.
Advantages of Laser Cutting in Packaging:
- Precision and Accuracy: Laser cutting provides exceptional precision, allowing for intricate cuts and designs that are consistent across large production runs.
- Versatility: This technology can cut through a wide range of materials, including paper, cardboard, plastic, and metal foils, making it suitable for various packaging types.
- Speed and Efficiency: Laser cutting is a fast process that can be easily integrated into automated production lines, significantly reducing turnaround times for packaging production.
- Minimal Waste: The precision of laser cutting minimizes material waste, making it a more sustainable option compared to traditional cutting methods.
- Customization: Laser cutting allows for easy customization, making it ideal for creating personalized or limited-edition packaging that meets specific marketing needs.
Use Cases in Automation:
Laser cutting systems in the packaging industry are often integrated into automated production workflows, where they perform high-speed cutting tasks with consistent precision. Automated feeding and positioning systems ensure that materials are correctly aligned for cutting, while vision systems and sensors monitor the quality of the cuts in real-time. This automation enhances productivity and ensures that each packaging piece meets exacting quality standards, reducing the risk of defects and improving overall production efficiency.
In summary, laser cutting offers significant advantages in the packaging industry, providing the tools needed to create high-quality, innovative packaging solutions. Its precision, versatility, and efficiency make it an indispensable technology for manufacturers looking to stay competitive in a rapidly evolving market.
OVERVIEW
Laser marking is a crucial technology in the packaging industry, offering a reliable, precise, and versatile method for applying critical information directly onto packaging materials. This non-contact process uses a focused laser beam to create permanent marks, such as text, logos, barcodes, and other identifiers, without compromising the integrity of the packaging. Laser marking provides high-resolution, durable markings that are essential for product identification, traceability, and branding, making it an indispensable tool in modern packaging solutions.
APPLICATIONS
Product Identification and Serialization:
- Application: Laser marking is used to apply unique identification codes, batch numbers, and serial numbers to packaging, ensuring traceability throughout the supply chain. This is particularly important for pharmaceuticals, food, and beverages, where accurate product identification is critical.
- Benefit: Enables efficient tracking of products from production to consumer, enhancing supply chain transparency and aiding in recall management if necessary.
Branding and Logo Marking:
- Application: High-quality logos, brand names, and promotional designs can be laser marked onto packaging materials, including cardboard, plastic, metal, and glass. This enhances the visual appeal of the packaging and strengthens brand identity.
- Benefit: Provides sharp, permanent marks that maintain their appearance throughout the product’s lifecycle, even under harsh environmental conditions.
Barcode and QR Code Marking:
- Application: Laser marking is used to generate and apply barcodes and QR codes on packaging, which are essential for inventory management, point-of-sale scanning, and consumer engagement.
- Benefit: Produces highly accurate, scannable codes that are resistant to wear, ensuring reliable data capture and access to product information.
Expiry Dates and Batch Codes:
- Application: Laser marking is employed to mark expiration dates, manufacturing dates, and batch codes on packaging, particularly in the food, beverage, and pharmaceutical industries.
- Benefit: Delivers clear, legible markings that are critical for consumer safety and regulatory compliance, ensuring that products are used within their safe consumption or use period.
Anti-Counterfeiting Measures:
- Application: Laser marking is used to create intricate, tamper-evident marks, holograms, or micro-text that are difficult to replicate, providing a robust solution against counterfeiting.
- Benefit: Enhances product security by making it easier to verify authenticity, thereby protecting both the brand and the consumer from counterfeit products.
Environmental and Sustainability Marks:
- Application: Packaging materials can be laser marked with eco-friendly symbols, recycling instructions, or other sustainability-related information, helping brands communicate their environmental commitments.
- Benefit: Supports sustainable packaging initiatives by providing clear, permanent markings that encourage responsible disposal and recycling.
Advantages of Laser Marking in Packaging:
- Permanent and Durable Marks: Laser marking creates permanent marks that are resistant to abrasion, heat, and chemicals, ensuring that the information remains legible throughout the product’s lifecycle.
- High Precision and Clarity: Laser marking delivers high-resolution, detailed markings that are essential for small or intricate designs, such as barcodes or micro-text.
- Versatility Across Materials: Laser marking can be applied to a wide range of materials, including plastics, glass, metals, paper, and composites, making it a versatile solution for diverse packaging needs.
- Eco-Friendly: Laser marking is a clean process that does not require inks, solvents, or other consumables, reducing environmental impact and contributing to sustainable packaging practices.
- Cost-Effective: Over time, laser marking can be more cost-effective than traditional printing methods, as it eliminates the need for consumables and reduces maintenance requirements.
Use Cases in Automation:
Laser marking systems are commonly integrated into automated packaging lines, where they can apply markings at high speeds without slowing down production. Automated systems ensure precise positioning of packaging under the laser head, maintaining consistent quality across large production runs. Vision systems are often paired with laser marking to verify the accuracy and quality of the marks, ensuring that each package meets the required standards before it proceeds to the next stage of the production process.
In summary, laser marking is an essential technology in the packaging industry, offering unparalleled precision, durability, and versatility. Its ability to apply critical information directly onto packaging materials helps ensure product safety, traceability, and brand integrity, making it a key component in the modern packaging landscape.
OVERVIEW
Laser engraving is a highly precise and versatile technology used in the packaging industry to create permanent, detailed designs and textures directly on packaging materials. Unlike laser marking, which primarily focuses on applying information such as text or codes, laser engraving is used to add depth and texture to packaging surfaces, enhancing both aesthetics and functionality. This non-contact process allows for the creation of intricate patterns, embossing effects, and custom textures that contribute to the visual appeal and tactile experience of the packaging.
APPLICATIONS
Custom Texturing and Embossing:
- Application: Laser engraving is employed to create custom textures and embossing on packaging materials, such as cardboard, metal, or plastic. This can include raised patterns, tactile finishes, or intricate designs that add a premium feel to the packaging.
- Benefit: Enhances the tactile experience and visual appeal of the packaging, making it more attractive and engaging to consumers.
High-End Branding and Decorative Elements:
- Application: Laser engraving is used to create detailed decorative elements and high-end branding features on luxury packaging, such as wine boxes, cosmetic cases, or premium product containers.
- Benefit: Adds a sophisticated and elegant touch to the packaging, helping to differentiate high-end products and reinforce brand identity.
Functional Surface Modification:
- Application: Laser engraving can modify the surface of packaging materials to improve functionality, such as creating anti-slip textures on handles or lids, or adding grooves for better grip.
- Benefit: Enhances the usability and practicality of the packaging, contributing to a better consumer experience.
Personalization and Customization:
- Application: Laser engraving allows for the customization of packaging with personalized messages, names, or designs, particularly for limited-edition or special occasion products.
- Benefit: Provides a unique and personalized touch that can increase customer engagement and loyalty, making the product more memorable.
Security Features:
- Application: Laser engraving can be used to create complex security features, such as micro-engraved patterns or intricate designs that are difficult to replicate. These features can be used to verify the authenticity of the packaging.
- Benefit: Enhances product security by making it harder for counterfeiters to replicate the packaging, protecting both the brand and consumers.
Die and Mold Creation for Packaging:
- Application: Laser engraving is also used in the creation of dies and molds for packaging production. The engraved dies are used to stamp or shape packaging materials, ensuring precise and consistent results.
- Benefit: Ensures high-quality production of packaging components with intricate details, contributing to the overall quality and consistency of the packaging.
Advantages of Laser Engraving in Packaging:
- High Precision and Detail: Laser engraving allows for the creation of highly detailed and intricate designs, making it ideal for applications that require fine lines, textures, and patterns.
- Durability and Permanence: The engraved designs are permanent and resistant to wear, ensuring that the aesthetic and functional features remain intact throughout the product’s lifecycle.
- Versatility Across Materials: Laser engraving can be applied to a wide range of materials, including wood, metal, glass, plastics, and leather, making it suitable for diverse packaging applications.
- Enhanced Aesthetic Appeal: Engraving adds depth and dimension to packaging, creating a premium look and feel that can enhance the perceived value of the product.
- Non-Contact Process: As a non-contact process, laser engraving does not damage or alter the structural integrity of the packaging material, ensuring that the packaging remains functional and intact.
Use Cases in Automation:
Laser engraving systems can be integrated into automated production lines, particularly in high-end or customized packaging manufacturing. Automated positioning systems ensure that each package is precisely aligned under the engraving laser, allowing for consistent and accurate results. This automation supports high-volume production while maintaining the intricate details required for luxury or specialized packaging, thereby enhancing both efficiency and quality.
In summary, laser engraving offers unique advantages in the packaging industry, providing the ability to add intricate designs, textures, and functional enhancements to packaging materials. Its precision, versatility, and ability to create both aesthetic and functional features make it a valuable tool in producing high-quality, distinctive packaging that stands out in a competitive market.
OVERVIEW
Laser scoring is a precise and efficient technology used in the packaging industry to create controlled, partial cuts in packaging materials, allowing for easy folding, bending, or tearing. This non-contact process uses a laser beam to weaken specific areas of the material without cutting through it entirely, ensuring that the packaging can be opened or manipulated with minimal effort. Laser scoring is widely used in the production of consumer-friendly packaging, enhancing both functionality and user experience.
APPLICATIONS
Easy-Open Packaging:
- Application: Laser scoring is commonly used to create tear lines or easy-open features on packaging such as snack bags, pouches, and other flexible materials. The laser precisely weakens the material along a designated path, allowing consumers to easily open the package without the need for additional tools.
- Benefit: Improves consumer convenience by providing a reliable and easy method for opening packaging, while maintaining the integrity of the seal until it is intended to be opened.
Folding Cartons:
- Application: In folding carton production, laser scoring is used to create precise crease lines that enable clean and accurate folds. This is particularly important for complex packaging designs or materials that are difficult to fold manually.
- Benefit: Ensures sharp, clean folds that enhance the overall appearance and functionality of the packaging, reducing material waste and improving assembly efficiency.
Perforated Tear Strips:
- Application: Laser scoring is employed to create perforated tear strips on various types of packaging, such as cardboard boxes, envelopes, and overwraps. These strips allow consumers to easily access the contents of the package by pulling along the perforated line.
- Benefit: Enhances the user experience by providing a convenient way to open packages without damaging the contents, while also maintaining product security until opened.
Microwaveable Packaging:
- Application: Laser scoring is used to create venting or steam-release features in microwaveable packaging. The laser scores the material in a way that allows it to open or vent when heated, ensuring that food products cook evenly and safely in the microwave.
- Benefit: Improves the functionality of microwaveable packaging, ensuring consistent cooking results and reducing the risk of packaging failure during heating.
Luxury and Specialty Packaging:
- Application: In high-end or specialty packaging, laser scoring is used to create intricate designs or patterns that add an element of sophistication and functionality, such as easy-to-open gift boxes or unique folding designs.
- Benefit: Enhances the aesthetic appeal and functionality of luxury packaging, making it more engaging and user-friendly for consumers.
Cigarette and Tobacco Packaging:
- Application: Laser scoring is used in the production of cigarette and tobacco packaging to create tear lines for easy access to the product, as well as to facilitate the folding of intricate packaging designs.
- Benefit: Provides a precise and controlled way to create easy-open features and folding lines, contributing to the overall quality and presentation of the packaging.
Advantages of Laser Scoring in Packaging:
- Precision and Consistency: Laser scoring provides highly precise and consistent results, ensuring that every package is easy to open or fold as intended.
- Customization: Laser scoring can be tailored to create specific patterns, depths, and lengths of scores, allowing for customization according to the needs of the packaging design.
- Non-Contact Process: The non-contact nature of laser scoring minimizes the risk of damaging or weakening the material beyond the scored area, preserving the overall strength and integrity of the packaging.
- Efficiency: Laser scoring can be integrated into high-speed production lines, improving manufacturing efficiency while maintaining quality.
- Sustainability: By enabling precise and controlled material weakening, laser scoring reduces waste and supports the use of lighter, more sustainable packaging materials.
Use Cases in Automation:
Laser scoring systems are often integrated into automated packaging lines, where they provide high-speed, consistent scoring of materials such as paper, cardboard, plastic films, and laminates. Automated systems ensure that the material is accurately positioned for scoring, allowing for continuous production with minimal downtime. Vision and inspection systems may also be used to monitor the quality of the scores in real-time, ensuring that each package meets the required specifications.
In summary, laser scoring is a valuable technology in the packaging industry, offering precise, customizable, and efficient solutions for creating easy-open features, folding lines, and other functional elements. Its ability to enhance both the functionality and user experience of packaging makes it an essential tool for modern packaging design and production.
OVERVIEW
Laser perforation is a cutting-edge technology used in the packaging industry to create precise, controlled holes or patterns of holes in packaging materials. This non-contact process uses a laser beam to puncture the material, creating perforations that serve various functional purposes, such as improving breathability, enhancing product freshness, or enabling controlled gas exchange. Laser perforation is particularly valued for its precision, flexibility, and ability to be tailored to specific packaging requirements, making it a versatile solution across multiple packaging applications.
APPLICATIONS
Breathable Packaging for Fresh Produce:
- Application: Laser perforation is widely used to create micro-perforations in packaging films for fresh fruits, vegetables, and other perishable goods. These perforations allow the package to “breathe,” helping to regulate moisture and gas exchange, which extends the shelf life of the produce.
- Benefit: Enhances product freshness by reducing spoilage and maintaining the quality of fresh produce during transportation and storage.
Modified Atmosphere Packaging (MAP):
- Application: In Modified Atmosphere Packaging, laser perforation is used to control the permeability of the packaging material, allowing for the optimal exchange of gases such as oxygen and carbon dioxide. This is crucial for maintaining the freshness of products like meats, cheeses, and bakery items.
- Benefit: Helps preserve the product’s quality and extends shelf life by creating the ideal environment within the package.
Ventilation for Microwaveable Packaging:
- Application: Laser perforation is employed to create controlled vent holes in microwaveable packaging, allowing steam to escape during heating. This ensures even cooking and prevents the packaging from bursting due to pressure build-up.
- Benefit: Enhances the safety and functionality of microwaveable packaging, ensuring consistent cooking results and reducing the risk of packaging failure.
Tobacco Packaging:
- Application: In the tobacco industry, laser perforation is used to create tiny holes in cigarette filters or packaging materials. These perforations control the airflow and burning rate of the cigarette, affecting the smoking experience.
- Benefit: Allows manufacturers to precisely control product characteristics and meet specific regulatory requirements for tobacco products.
Controlled Release Packaging:
- Application: Laser perforation is used in packaging where controlled release of gases, moisture, or aromas is needed, such as in certain pharmaceutical or agricultural products. The perforations can be designed to release contents at a controlled rate.
- Benefit: Provides a tailored solution for products that require specific environmental conditions within the package, enhancing product performance and shelf life.
Advantages of Laser Perforation in Packaging:
- Precision and Control: Laser perforation allows for highly precise control over the size, shape, and distribution of perforations, enabling customization according to the specific needs of the product and packaging.
- Non-Contact Process: As a non-contact method, laser perforation minimizes the risk of contamination and damage to the packaging material, ensuring consistent quality.
- Versatility Across Materials: Laser perforation can be applied to a wide range of packaging materials, including plastic films, paper, foils, and laminates, making it a versatile solution for various packaging types.
- Efficiency and Speed: Laser perforation systems can be integrated into high-speed production lines, providing consistent, high-quality results with minimal downtime.
- Enhanced Product Performance: By enabling precise control over gas exchange, moisture levels, and shelf life, laser perforation directly contributes to improved product quality, extended shelf life, and enhanced consumer satisfaction.
Use Cases in Automation:
Laser perforation systems are typically integrated into automated packaging lines, where they perform high-speed perforation tasks with precision. Automated feeding and positioning systems ensure that the material is accurately aligned for perforation, and vision systems are often employed to monitor the quality of the perforations in real-time. This integration enhances production efficiency, reduces waste, and ensures that every package meets the required specifications for functionality and quality.
In summary, laser perforation offers significant advantages in the packaging industry, providing a versatile, precise, and efficient solution for creating functional and user-friendly packaging. Its applications range from extending product shelf life to enhancing the functionality of packaging, making it an essential technology in modern packaging design and production.
DEDICATED TO INNOVATION
At Scantech Laser, our commitment to the packaging industry goes beyond simply fulfilling customer requirements; it’s about fostering innovation and shaping the future of packaging. Understanding the essential role that the packaging sector plays in global commerce and consumer satisfaction, we are dedicated to providing tailored laser solutions that address the unique challenges and opportunities within the packaging industry. Whether it’s enhancing precision in cutting and engraving, improving sustainability through material efficiency, or increasing production speeds, our focus is on driving the evolution of packaging with advanced laser technology.
Elevating Packaging Standards with Laser Technology
In the dynamic packaging industry, precision, speed, and reliability are key. Scantech Laser’s cutting-edge laser technologies are tailored to meet these essential demands, providing innovative solutions that boost the efficiency and quality of packaging processes. From precise laser cutting and perforating to accurate marking and engraving, our advanced systems ensure unmatched precision and consistency. This guarantees that every packaging component produced meets the highest standards of quality, optimizing packaging performance across various sectors.
Innovating Packaging Solutions with Laser Technology
Our approach to the packaging industry allows us to envision its long-term future while addressing current growth and development needs. Whether it’s optimizing material use through advanced laser cutting techniques, enhancing package integrity with precise laser sealing, or improving product traceability with durable laser marking, Scantech Laser’s solutions are at the forefront of packaging innovation.
Shaping the Future of Packaging with Laser Solutions
As the packaging industry continues to evolve, Scantech Laser remains committed to supporting its growth with innovative, reliable, and efficient laser solutions. We are dedicated to understanding the industry’s unique challenges and providing the technologies that will drive its success in the years to come. Together, we’re not just meeting the needs of today; we’re propelling the packaging industry into the future.