Scantech in Pharma Sector
Laser technology plays a crucial role in the pharmaceutical industry, offering precision, efficiency, and reliability in various processes. From tablet marking to packaging, lasers are essential for ensuring product quality, traceability, and compliance with industry standards. The non-contact nature of laser processes minimizes contamination risks, making them ideal for sensitive pharmaceutical applications. Laser solutions are integrated with automation systems to enhance productivity and maintain consistency across large-scale production, ensuring that the pharmaceutical industry can meet the growing demand for safe and effective medications.
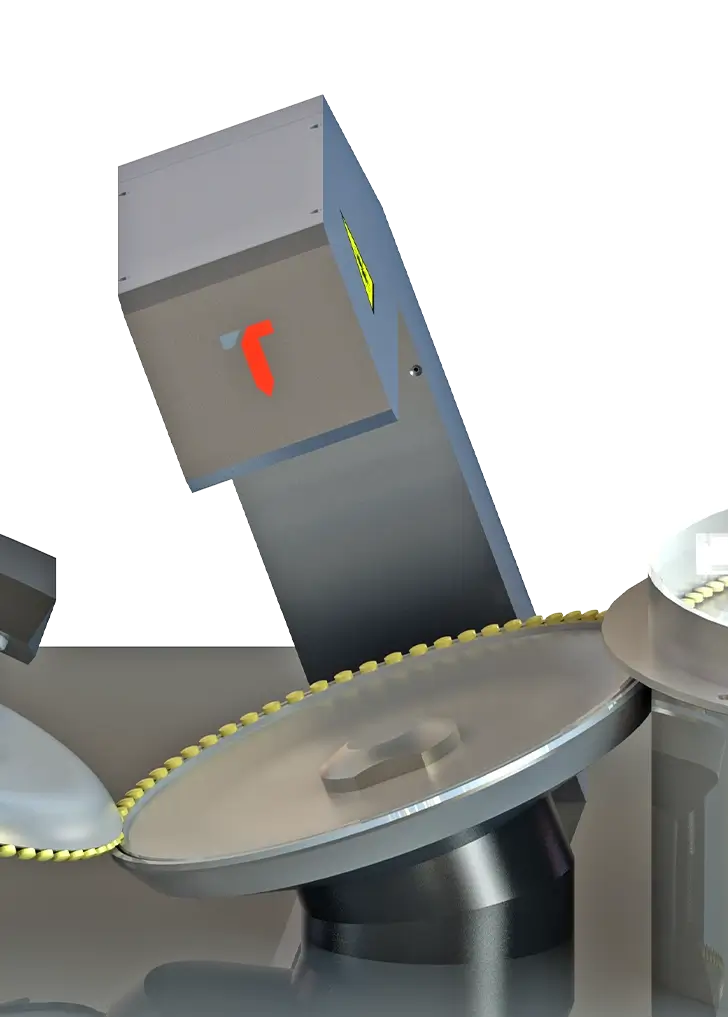
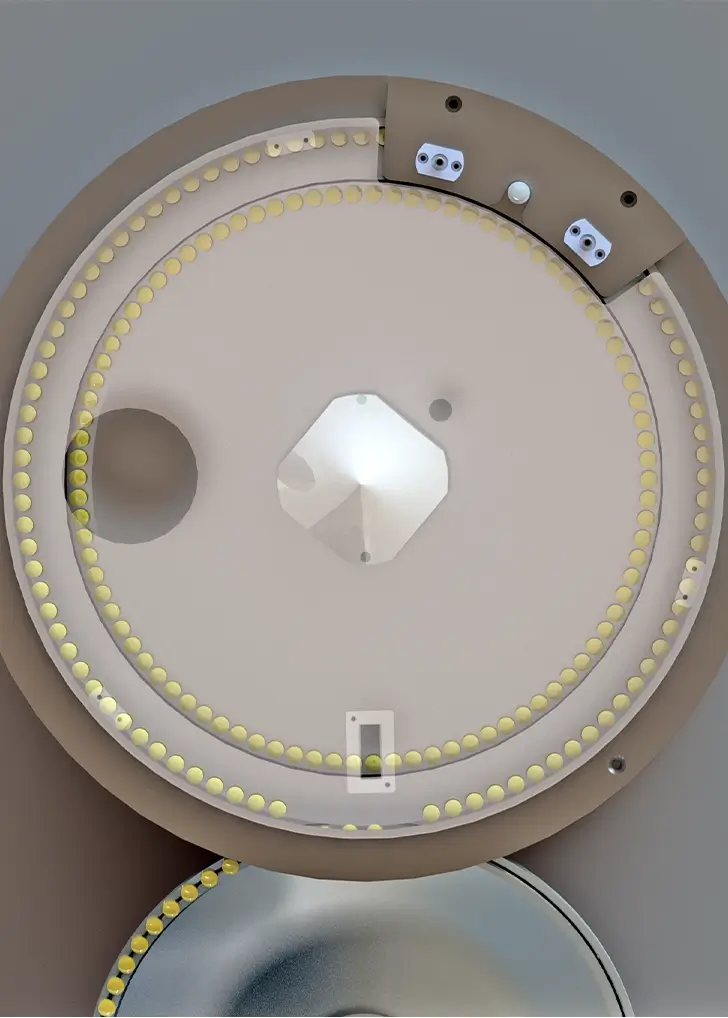
PHARMACEUTICAL APPLICATIONS
OVERVIEW
Tablet laser drilling is a specialized process used in the pharmaceutical industry to create precise micro-holes in tablet coatings. This technology is essential for the production of controlled-release and extended-release drug delivery systems, where the rate of drug release is managed by the size and location of the drilled holes. The laser drilling process is highly accurate, allowing for the creation of consistent and uniform apertures without compromising the tablet’s structural integrity. This precision is critical in ensuring that each tablet releases the correct dosage of medication over a specified period.
APPLICATIONS
Controlled-Release Systems:
- Application: Laser drilling is primarily used in the manufacturing of controlled-release tablets, such as those using the Osmotic-controlled Release Oral delivery System (OROS). In these systems, the laser-drilled holes allow for the regulated release of the active pharmaceutical ingredient (API) through osmotic pressure, ensuring a steady therapeutic effect over time.
- Benefit: The precision of laser drilling ensures uniform drug release, enhancing the efficacy and safety of the medication.
Extended-Release Tablets:
- Application: Extended-release tablets, designed to dissolve slowly and release a drug over an extended period, utilize laser drilling to control the dissolution rate. The size and number of laser-drilled holes can be adjusted to achieve the desired release profile, providing consistent drug delivery.
- Benefit: This technology helps maintain therapeutic drug levels in the bloodstream, reducing the need for frequent dosing and improving patient compliance.
Multi-Layered Tablets:
- Application: For multi-layered tablets, where different layers may contain different drugs or release mechanisms, laser drilling is used to create targeted apertures in specific layers. This allows for the sequential or simultaneous release of multiple drugs from a single tablet.
- Benefit: Enhances the versatility of combination therapies, offering more complex and tailored treatment options for patients.
Enteric-Coated Tablets:
- Application: In enteric-coated tablets, which are designed to bypass the stomach and dissolve in the intestines, laser drilling can be used to create precise release channels that activate only under specific pH conditions. This ensures that the drug is released in the desired part of the gastrointestinal tract.
- Benefit: Protects sensitive drugs from stomach acid and targets delivery to the intestine, improving drug absorption and efficacy.
Importance of Laser Drilling in Pharmaceutical Manufacturing:
- Precision: Laser drilling provides unmatched precision, ensuring that each tablet has uniform hole size and placement, which is critical for consistent drug delivery.
- Non-Contact Process: The non-contact nature of laser drilling minimizes the risk of contamination, making it ideal for pharmaceutical applications where hygiene is paramount.
- Customization: Laser parameters can be easily adjusted to accommodate different tablet designs, coatings, and drug release profiles, offering manufacturers flexibility in product development.
- Quality Control: Laser drilling systems are often integrated with automated inspection technologies, ensuring that only tablets meeting strict quality criteria are released for distribution.
In summary, tablet laser drilling is a vital technology in the pharmaceutical industry, enabling the production of sophisticated drug delivery systems that improve patient outcomes through precise, controlled medication release.
overview
Tablet printing and serialization are crucial processes in the pharmaceutical industry, used for branding, identification, and ensuring the traceability of each tablet. Laser printing is the most advanced and reliable method for these applications, offering high precision, permanence, and flexibility in the printing process. Unlike traditional ink-based methods, laser printing does not require consumables and produces indelible marks that are resistant to wear and environmental factors. Serialization, on the other hand, involves assigning a unique identifier to each tablet, enabling full traceability throughout the supply chain. This is vital for combating counterfeit drugs and ensuring patient safety.
APPLICATIONS
Branding and Logo Printing:
- Application: Laser printing is widely used to imprint logos, brand names, or other identifying marks on tablets. This not only aids in brand recognition but also helps distinguish products from those of competitors.
- Benefit: The permanence and clarity of laser-printed marks ensure that the branding remains legible throughout the tablet’s shelf life, enhancing both consumer trust and brand integrity.
Dosage and Identification Marking:
- Application: Tablets often need to have dosage information or other identifiers, such as batch numbers, printed directly onto them. Laser printing can produce this information with high accuracy, even on small or complex surfaces.
- Benefit: Ensures that healthcare providers and patients can easily identify the correct dosage and type of medication, reducing the risk of errors in medication administration.
Anti-Counterfeiting Measures:
- Application: Serialization allows each tablet to be marked with a unique code or identifier that can be tracked through the supply chain. Laser printing is used to apply these codes directly to the tablet surface, making it extremely difficult for counterfeiters to replicate.
- Benefit: Enhances drug safety by providing a robust method for verifying the authenticity of pharmaceutical products, thereby protecting consumers from counterfeit drugs.
Regulatory Compliance:
- Application: Serialization and laser printing help pharmaceutical companies comply with stringent regulations that require traceability and accountability for each tablet produced. This includes marking tablets with expiration dates, manufacturing codes, and other regulatory information.
- Benefit: Ensures that pharmaceutical companies meet international standards for drug safety and traceability, reducing the risk of recalls and legal liabilities.
Patient-Specific Medication:
- Application: In personalized medicine, where medications are tailored to individual patients, laser printing allows for the customization of tablets with patient-specific information. This could include the patient’s name, specific dosage instructions, or other relevant data.
- Benefit: Improves patient adherence to prescribed treatment regimens by providing clear, personalized instructions directly on the tablet, reducing the likelihood of medication errors.
Importance of Tablet Printing and Serialization:
- Precision and Clarity: Laser printing offers unmatched precision, producing clear and legible markings that are essential for patient safety and regulatory compliance.
- Durability: Laser marks are permanent and resistant to abrasion, moisture, and chemicals, ensuring that critical information remains intact throughout the tablet’s lifecycle.
- Customization: The flexibility of laser printing allows for easy customization of markings, making it suitable for a wide range of tablet sizes, shapes, and materials.
- Traceability: Serialization provides a comprehensive system for tracking each tablet from production to end-use, crucial for maintaining the integrity of the pharmaceutical supply chain and protecting against counterfeiting.
Use Cases in Automation:
Tablet printing and serialization are often integrated into automated production lines. These systems use robotic arms and conveyor systems to position tablets for laser printing, ensuring high throughput and consistency. Automated inspection systems are also employed to verify the accuracy and quality of each print, rejecting any tablets that do not meet specified criteria. This integration of laser printing with automation enhances production efficiency, reduces human error, and ensures that each tablet is correctly marked and serialized.
In summary, tablet printing and serialization are essential processes in the pharmaceutical industry, ensuring that tablets are properly branded, identified, and traceable. Laser technology plays a critical role in these processes, offering precision, durability, and flexibility that are vital for maintaining the safety, integrity, and compliance of pharmaceutical products.
overview
Softgel laser printing is a specialized process used to mark soft gelatin capsules (softgels) with logos, brand names, dosage information, or other identifiers. This technique leverages the precision of laser technology to create clear, legible, and permanent marks on the surface of softgels without damaging the delicate capsule material. Unlike traditional ink-based printing methods, laser printing does not involve direct contact with the softgel, ensuring that the structural integrity of the capsule is maintained. This process is highly valued in the pharmaceutical and nutraceutical industries for its ability to enhance product identification, brand recognition, and regulatory compliance.
APPLICATIONS
- Branding and Logo Marking:
- Application: Laser printing is used to imprint company logos, product names, or other branding elements directly onto the softgel surface. This helps in differentiating products in a competitive market.
- Benefit: The precision of laser printing ensures that the branding is clear and durable, even on the curved surface of a softgel, thereby enhancing brand visibility and consumer trust.
- Dosage Information:
- Application: Softgels often need to display dosage information, which can be accurately printed using laser technology. This is particularly important for over-the-counter medications and dietary supplements where correct dosage is critical.
- Benefit: Laser-printed dosage information is permanent and resistant to wear, ensuring that it remains visible to consumers throughout the product’s shelf life, thus aiding in safe and correct usage.
- Anti-Counterfeiting Measures:
- Application: Serialization and unique identifiers can be laser-printed onto each softgel to prevent counterfeiting and ensure product authenticity. This is essential for maintaining consumer safety and protecting brand integrity.
- Benefit: By providing a way to verify the authenticity of softgel products, laser printing helps combat counterfeit products in the pharmaceutical and nutraceutical markets.
- Batch and Lot Numbering:
- Application: Laser printing is used to mark softgels with batch or lot numbers, which are critical for traceability and quality control in the manufacturing process.
- Benefit: This ensures that any issues related to specific batches can be quickly identified and addressed, thereby enhancing product safety and regulatory compliance.
- Customization for Personalized Medicine:
- Application: In cases where personalized medicine is needed, laser printing can be used to customize softgels with patient-specific information, such as names or specific treatment codes.
- Benefit: This capability supports personalized healthcare by ensuring that patients receive the correct medication, tailored to their individual needs.
Importance of Softgel Laser Printing:
- Non-Contact Process: Laser printing is a non-contact method, meaning it does not physically touch the softgel. This is crucial for maintaining the integrity of the capsule and preventing contamination or damage.
- High Precision: Laser technology offers high precision, enabling the printing of detailed and small text or logos on the softgel surface, which is especially important for small-sized capsules.
- Permanence and Durability: The marks created by laser printing are permanent and resistant to environmental factors such as moisture, light, and friction, ensuring that the information remains legible throughout the product’s life.
- Flexibility: Laser printing can be easily adapted to different softgel sizes, shapes, and colors, making it a versatile solution for a wide range of products.
- Regulatory Compliance: The ability to mark softgels with critical information such as batch numbers and expiration dates helps manufacturers comply with stringent regulatory requirements.
Use Cases in Automation:
Softgel laser printing is typically integrated into automated production lines, where softgels are fed through laser printing stations at high speeds. Automated systems ensure precise alignment of each softgel for accurate printing, and inspection systems check the quality of each print in real-time. This automation allows for high-volume production while maintaining consistency and quality, reducing human error, and increasing overall efficiency.
In summary, softgel laser printing is a vital technology in the pharmaceutical and nutraceutical industries, offering a reliable and precise method for marking capsules with essential information. Its non-contact nature, coupled with the durability and clarity of the marks, makes it an indispensable tool for enhancing product safety, compliance, and brand recognition.
OVERVIEW
Blister pack perforation and printing are critical processes in the pharmaceutical and consumer goods industries, primarily used for packaging and labeling individual doses of medications, supplements, or small consumer products. Blister packs provide a secure, tamper-evident, and hygienic way to package products, ensuring that each dose or item is protected from environmental factors such as moisture, light, and contamination. The perforation process involves creating precise lines or holes in the blister pack material, allowing for easy separation of individual units without compromising the integrity of the packaging. Printing on blister packs includes essential information such as product names, dosage instructions, expiration dates, and batch numbers.
APPLICATIONS
- Pharmaceutical Packaging:
- Application: Blister packs are widely used for packaging tablets, capsules, and other solid dose medications. Perforation allows patients to easily separate a single dose from the pack, while printing provides clear information on drug identification and usage.
- Benefit: This ensures both patient safety and convenience, as well as compliance with regulatory requirements for labeling.
- Nutraceuticals and Dietary Supplements:
- Application: Similar to pharmaceuticals, nutraceutical products are often packaged in blister packs for precise dosing and easy access. Perforation facilitates portion control, and printing enhances brand recognition and provides necessary consumption instructions.
- Benefit: Helps consumers maintain a consistent supplement regimen and prevents confusion between different products.
- Consumer Goods Packaging:
- Application: Blister packs are also used for small consumer goods such as batteries, electronic components, or personal care items. Perforation enables easy access to the product, while printing offers branding, instructions, and product information.
- Benefit: Enhances user experience by providing easy-to-open packaging and clear, legible product details.
- Clinical Trials and Sample Packaging:
- Application: In clinical trials, medications are often packaged in perforated blister packs to allow easy distribution of single doses to trial participants. Printing on these packs includes critical information such as trial codes, participant identifiers, and dosage schedules.
- Benefit: Supports accurate dosing and tracking during clinical trials, ensuring the reliability of trial results.
- Child-Resistant and Senior-Friendly Packaging:
- Application: Blister packs can be designed with specific perforation patterns to create child-resistant or senior-friendly packaging. Printing provides clear usage instructions to enhance safety.
- Benefit: Balances safety for children with ease of access for older adults, addressing diverse consumer needs.
Importance of Blister Pack Perforation & Printing:
- Product Integrity: Perforation ensures that individual doses or items can be separated without compromising the protection offered by the blister pack, maintaining product integrity.
- Ease of Use: Perforation allows for easy opening and separation of blister packs, improving user convenience, especially for those with limited dexterity.
- Regulatory Compliance: Printing on blister packs is essential for meeting regulatory requirements, providing necessary information such as drug identification, usage instructions, expiration dates, and batch numbers.
- Branding and Product Differentiation: High-quality printing on blister packs enhances brand recognition and helps differentiate products in a competitive market.
- Safety and Security: Perforation and printing contribute to tamper-evidence, helping to ensure that the product has not been altered or compromised, which is crucial for consumer safety.
Use Cases in Automation:
Blister pack perforation and printing are typically integrated into automated packaging lines, where high-speed machines handle both processes simultaneously. Automated perforation systems ensure precision and consistency, allowing for uniform separation of blister pack units. Automated printing systems can apply variable data, such as batch numbers and expiration dates, in real-time, ensuring accuracy and compliance. Inspection systems are often integrated to verify the quality of both perforation and printing, reducing the risk of defects and ensuring that every package meets strict quality standards.
In summary, blister pack perforation and printing are essential processes in the packaging of pharmaceuticals, nutraceuticals, and consumer goods, providing a combination of product protection, ease of use, and regulatory compliance. Through the use of automation, these processes can be efficiently integrated into high-volume production lines, ensuring consistent quality and enhancing overall packaging performance.
OVERVIEW
Ampoule and vial coding and drilling are crucial processes in the pharmaceutical industry, primarily used to ensure the traceability, identification, and security of injectable drugs and other liquid medications. Ampoules and vials are small glass or plastic containers used to store and preserve sterile drugs, vaccines, and other critical pharmaceutical products. Coding involves marking these containers with essential information such as batch numbers, expiration dates, and product codes, ensuring compliance with regulatory standards and enhancing patient safety. Drilling, or precise perforation, is used in specific applications to create venting holes or to facilitate the easy opening of ampoules.
APPLICATIONS
Pharmaceutical Coding:
- Application: Coding ampoules and vials is essential for the identification and traceability of pharmaceutical products. Information such as drug names, batch numbers, manufacturing dates, and expiration dates are laser-marked on the container.
- Benefit: This process ensures compliance with regulatory standards, supports accurate record-keeping, and enhances patient safety by reducing the risk of medication errors.
Vaccine Serialization:
- Application: For vaccines, serialization involves applying a unique identifier to each vial or ampoule, enabling tracking through the supply chain. This is particularly important in preventing counterfeiting and ensuring that vaccines reach their intended recipients safely.
- Benefit: Serialization enhances the security of vaccine distribution, allowing for real-time tracking and ensuring that only authentic vaccines are administered.
Ampoule Drilling:
- Application: In some cases, ampoules require precise drilling to create small venting holes. This can be necessary for specific drug formulations that need controlled airflow or for facilitating the easy snapping of the ampoule neck during opening.
- Benefit: Drilling ensures the functionality and safety of the ampoule, preventing pressure buildup and making it easier for healthcare professionals to access the medication.
Anti-Counterfeiting Measures:
- Application: Laser coding and drilling are used to apply unique, tamper-evident marks or micro-perforations on ampoules and vials. These features are difficult to replicate, serving as an effective deterrent against counterfeiting.
- Benefit: Protects the integrity of the pharmaceutical supply chain by ensuring that only genuine products reach patients, thereby safeguarding public health.
Cold Chain Compliance:
- Application: For drugs that require cold chain storage, ampoules and vials can be coded with temperature-sensitive indicators that change color or appearance based on exposure to temperatures outside the safe range.
- Benefit: Ensures that temperature-sensitive medications remain potent and effective throughout the distribution process.
Clinical Trials:
- Application: During clinical trials, ampoules and vials are coded with trial-specific information, including participant identifiers and dosage instructions. This ensures the accurate administration and tracking of trial medications.
- Benefit: Supports the integrity of clinical trial data and ensures compliance with regulatory requirements for drug trials.
Importance of Ampoule and Vial Coding & Drilling:
- Regulatory Compliance: Coding ampoules and vials is essential for meeting global regulatory requirements, including those related to drug traceability, serialization, and anti-counterfeiting.
- Patient Safety: Accurate coding and drilling contribute to patient safety by ensuring that drugs are correctly identified, securely sealed, and easily accessible when needed.
- Supply Chain Security: Serialization and anti-counterfeiting measures protect the pharmaceutical supply chain from fraud, ensuring that only authentic, safe products reach patients.
- Ease of Use: Drilling ampoules facilitates easy opening, which is particularly important in clinical settings where quick and safe access to medication is critical.
Use Cases in Automation:
Ampoule and vial coding and drilling are typically integrated into automated production lines in pharmaceutical manufacturing. High-speed laser coding systems can mark thousands of ampoules or vials per hour with precision, applying permanent, non-erasable codes without damaging the container. Automated drilling systems create precise perforations or vent holes in ampoules as part of the filling and sealing process. These automated systems ensure consistent quality, reduce the risk of human error, and increase production efficiency. Vision inspection systems are often used in conjunction with these processes to verify the accuracy of coding and drilling, ensuring that each container meets stringent quality standards.
In summary, ampoule and vial coding and drilling are critical processes in the pharmaceutical industry, supporting product traceability, safety, and security. Through the integration of automation, these processes are executed with high precision and efficiency, ensuring that pharmaceutical products are accurately identified, securely packaged, and ready for safe use by healthcare professionals and patients alike.
DEDICATED TO INNOVATION
The Scantech Pharmaceutical Innovation Center was established with a clear mission: to provide specialized material and application expertise to support our pharmaceutical clients. Armed with state-of-the-art laser technology and backed by decades of experience, our commitment is to assist pharmaceutical researchers and manufacturers in exploring potential applications and tackling the prevailing challenges and opportunities in the industry, such as efficiency improvements, controlled release mechanisms, precision dosing, regulatory compliance, and material safety.
Our center serves as a crucial resource for pharmaceutical professionals looking to enhance drug formulations and optimize production processes. By leveraging our advanced laser technologies, we aim to improve the precision and efficiency of pharmaceutical manufacturing, contributing to the development of safer, more effective medications.
Precision and Innovation in Pharmaceutical Manufacturing
In the dynamic realm of pharmaceutical manufacturing, where precision, efficiency, and compliance are critical, Scantech Laser’s cutting-edge laser technologies are tailored to exceed these stringent demands. Our advanced laser systems provide a spectrum of solutions that enhance the operational efficiency and product quality of pharmaceutical production processes. From precise laser drilling and accurate marking to clean cutting and reliable serialization, our technologies ensure unparalleled precision and consistency. This rigorous attention to detail guarantees that every pharmaceutical product not only meets but surpasses the highest standards of quality and safety.
Pioneering the Future of Pharmaceutical Manufacturing
Our approach to the pharmaceutical sector allows us to anticipate its long-term advancements while addressing the immediate requirements for growth and innovation. Whether it’s facilitating controlled drug release through precision laser drilling, enhancing product safety with accurate laser marking, or ensuring compliance with rigorous serialization standards, Scantech Laser’s solutions are at the forefront of pharmaceutical innovation. Our advanced laser technologies drive the development of more effective and secure pharmaceutical products, meeting both today’s needs and tomorrow’s challenges.
Advancing Pharmaceutical Excellence with Innovations
As the pharmaceutical industry continues to evolve, Scantech Laser remains committed to supporting its growth with innovative, reliable, and efficient laser solutions. We are dedicated to understanding the industry’s unique challenges and providing the technologies that will drive its success in the years to come. Together, we’re not just meeting the needs of today; we’re propelling the pharmaceutical industry into the future.