SCANTECH IN Sheet Metal Processing
In the sheet metal processing industry, laser technology has become a cornerstone due to its precision, speed, and versatility. Lasers provide unparalleled accuracy and efficiency in cutting, welding, and marking sheet metal, which are essential for a wide range of applications across various sectors including automotive, aerospace, construction, and consumer electronics. The non-contact nature of laser processing ensures minimal mechanical stress and heat distortion, making it ideal for handling delicate or complex metal sheets.
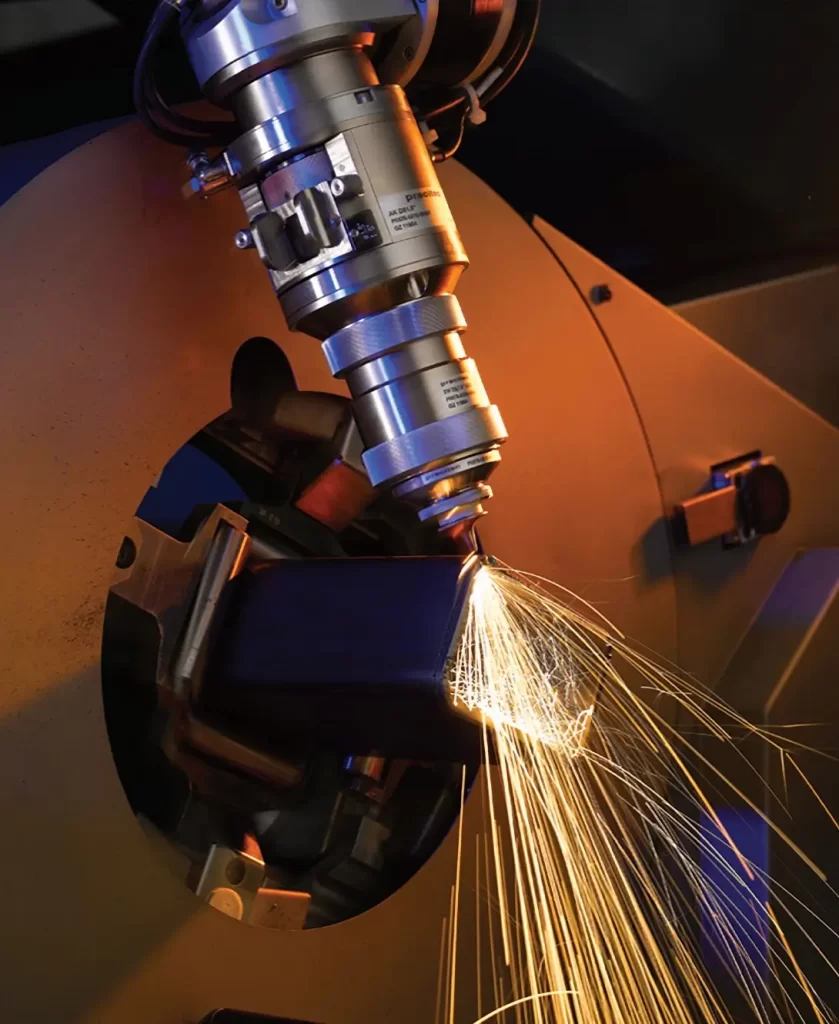
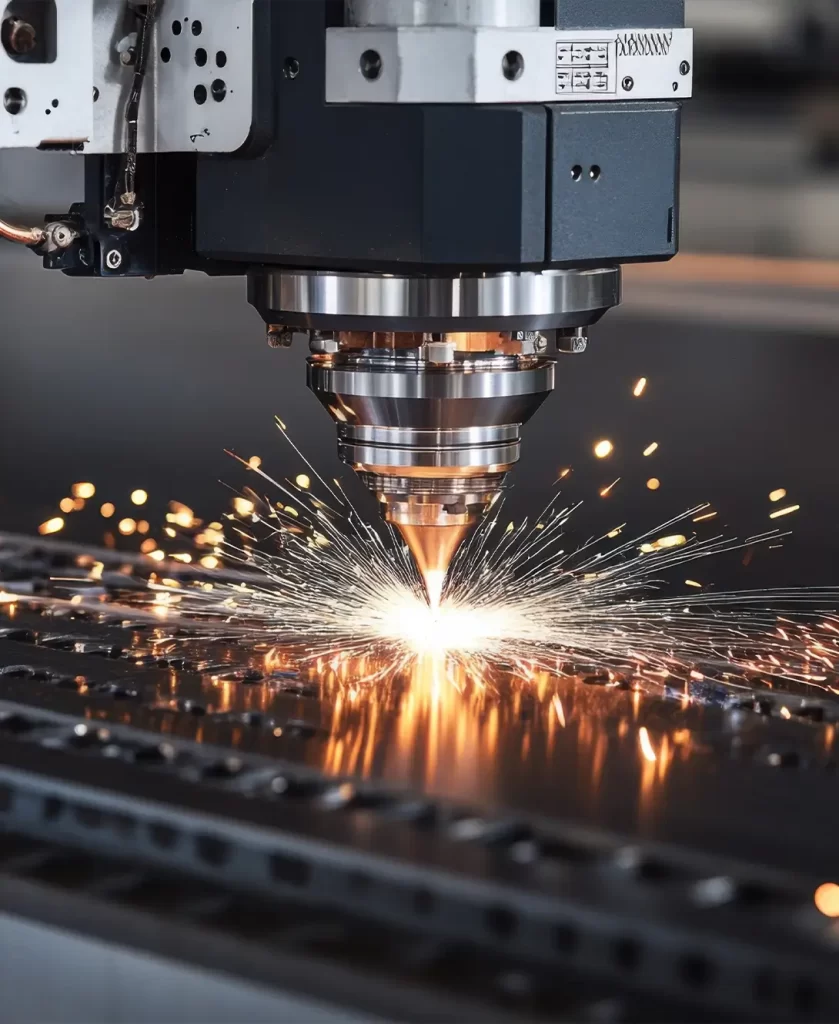
Sheet Metal Processing APPLICATIONS
OVERVIEW
Laser welding stands out as a revolutionary technique in the sheet metal processing industry, offering significant advantages over traditional welding methods. This advanced technology utilizes a high-energy laser beam to fuse metal pieces together, creating strong, high-quality joints with minimal heat input. The precision and speed of laser welding make it ideal for a wide range of applications in industries that demand quick turnaround times and fine, clean finishes, such as automotive, aerospace, and consumer electronics.
APPLICATIONS
Precision Fabrication:
- Application: Laser welding is extensively used in the precision fabrication of complex assemblies where tight tolerances and minimal distortion are required. The precision of laser welding is particularly beneficial for intricate designs commonly found in electronics and aerospace components.
- Benefit: Provides high-quality welds that maintain the integrity and functionality of complex assemblies without compromising structural stability.
Automotive Body Assembly:
- Application: In the automotive industry, laser welding is crucial for assembling various parts of vehicle bodies. This includes welding thin-sheet metals for doors, hoods, and panels. Laser welding’s ability to create strong, continuous seams is essential for the structural integrity and aesthetic quality of automotive parts.
- Benefit: Ensures durable, lightweight vehicle structures that contribute to overall vehicle safety and fuel efficiency.
Tool and Die Repair:
- Application: Laser welding is often used in the repair of high-value tool and die components. It is particularly useful for adding material to worn areas or fixing cracks without the need for completely replacing expensive parts.
- Benefit: Extends the life of tools and dies, reducing costs associated with tool maintenance and downtime.
Stainless Steel Applications:
- Application: The food service and medical equipment industries often require the welding of stainless steel components. Laser welding is ideal for this purpose due to its ability to provide hygienic, corrosion-resistant welds.
- Benefit: Creates clean, smooth welds that meet the hygiene standards required in medical and food processing applications.
Custom Metalwork and Art:
- Application: Artists and designers utilize laser welding for custom metalwork projects that require precise, aesthetic, and structural joins. This can include sculptures, furniture, and decorative items.
- Benefit: Offers the flexibility to execute complex artistic concepts with high precision and minimal post-weld finishing.
Robotics and Automation Integration:
- Application: Laser welding systems are frequently integrated with robotic arms in automated production lines. This is common in mass production environments where consistency, speed, and repeatability are key.
- Benefit: Enhances production efficiency, reduces labor costs, and improves weld consistency across large volumes of work.
Advantages of Laser Welding in Sheet Metal Processing:
- Speed and Efficiency: Laser welding is much faster than traditional welding methods, significantly reducing process times.
- Precision and Quality: Offers greater control over the welding process, resulting in higher-quality joins with minimal heat distortion.
- Versatility: Capable of welding a variety of metals, including mixed materials, with varying thicknesses.
- Reduced Heat Input: Minimizes the thermal damage to surrounding materials, which is crucial for maintaining the properties and appearance of precision components.
- Automation Compatibility: Easily integrates with digital controls and robotic systems, making it suitable for high-volume, automated production settings.
In summary, laser welding is a transformative technology in the sheet metal processing industry, offering unmatched precision, efficiency, and versatility. Its application extends across various sectors, improving product quality, production speed, and cost-effectiveness. As industries continue to innovate and demand more complex metal components, laser welding will remain an essential process in modern manufacturing workflows.
overview
Laser cutting is a pivotal technology in the sheet metal fabrication industry, known for its precision, speed, and versatility. It uses a focused laser beam to cut through metals, allowing for intricate shapes, complex geometries, and high-quality finishes with minimal waste. This technology is essential for industries that require precise and efficient cutting solutions, such as automotive, aerospace, electronics, and construction.
APPLICATIONS
Automotive Parts Manufacturing:
- Application: Laser cutting is used to produce various automotive components, including body panels, brackets, and structural parts. It allows for the precise cutting of high-strength steel and aluminum, which are essential for lightweight and fuel-efficient vehicles.
- Benefit: Ensures high precision and consistency in parts, leading to improved vehicle safety and performance.
Architectural Metalwork:
- Application: In architecture, laser cutting is used to create intricate designs in metal panels, facades, and decorative elements. The ability to produce detailed patterns with clean edges makes it ideal for custom metalwork.
- Benefit: Enables architects and designers to realize complex designs with high aesthetic value and structural integrity.
Aerospace Component Fabrication:
- Application: The aerospace industry relies on laser cutting for the fabrication of lightweight yet durable components, such as airframe structures and engine parts. The technology’s ability to cut complex shapes from advanced alloys is crucial for aerospace applications.
- Benefit: Provides the precision and material integrity needed for critical aerospace components, ensuring safety and performance.
Electrical Enclosures and Panels:
- Application: Laser cutting is used to manufacture electrical enclosures, control panels, and other components that require precise cutouts and detailed features. This includes cutting holes for switches, connectors, and vents.
- Benefit: Offers high precision and repeatability, ensuring that all parts fit together seamlessly in assembly.
Industrial Equipment and Machinery:
- Application: In the industrial sector, laser cutting is utilized for producing machine parts, frames, and supports. The technology is suitable for cutting thick and thin metals with high accuracy, essential for heavy machinery.
- Benefit: Enhances the durability and accuracy of machine components, contributing to the longevity and reliability of industrial equipment.
HVAC Systems:
- Application: Laser cutting is used in the fabrication of HVAC components, such as ducts, vents, and fittings. The precision of laser cutting ensures that these parts fit together perfectly, improving system efficiency.
- Benefit: Improves the energy efficiency and performance of HVAC systems through precise and accurate component fabrication.
Metal Furniture and Fixtures:
- Application: The furniture industry uses laser cutting for creating metal parts for desks, chairs, shelving, and decorative fixtures. The technology allows for the creation of intricate designs and custom pieces.
- Benefit: Enables the production of high-quality, aesthetically pleasing furniture and fixtures with intricate details and robust construction.
Advantages of Laser Cutting in Sheet Metal Fabrication:
- Precision and Accuracy: Laser cutting offers exceptional precision, enabling the production of intricate designs with tight tolerances.
- High Speed and Efficiency: Laser cutting is faster than traditional cutting methods, reducing production times and increasing throughput.
- Versatility: Capable of cutting a wide range of metals, including stainless steel, aluminum, brass, and titanium, in varying thicknesses.
- Minimal Material Waste: The precision of laser cutting reduces the amount of waste material, making it a more cost-effective and environmentally friendly option.
- Clean Cuts and Smooth Edges: Laser cutting produces smooth edges without the need for additional finishing processes, improving the overall quality of the final product.
- Automation Compatibility: Laser cutting systems can be easily integrated into automated production lines, enhancing consistency and reducing labor costs.
Solutions Offered by Scantech Laser:
- Fiber Laser Cutting Systems: Designed for high-speed, precise cutting of various metals, our fiber laser systems offer unmatched efficiency and flexibility in sheet metal fabrication.
- CO2 Laser Cutting Solutions: Ideal for cutting non-metal materials or metals with thicker gauges, our CO2 lasers provide powerful cutting capabilities for a wide range of applications.
- Automation Integration: Our laser cutting systems can be seamlessly integrated with robotic arms, conveyor systems, and other automation technologies to optimize production workflows.
- Custom Laser Cutting Solutions: We offer tailored laser cutting solutions to meet specific industry requirements, whether for prototyping, small batch production, or large-scale manufacturing.
Conclusion:
Laser cutting is a transformative technology in the sheet metal fabrication industry, offering unparalleled precision, speed, and versatility. It is essential for producing high-quality components across various sectors, from automotive to aerospace, and beyond. Scantech Laser’s advanced cutting solutions empower manufacturers to achieve greater efficiency, reduce costs, and meet the evolving demands of their industries.
OVERVIEW
Laser marking is a critical technology in the sheet metal fabrication industry, offering high precision, durability, and versatility for a wide range of applications. This non-contact process uses a focused laser beam to etch or engrave permanent marks on metal surfaces, such as serial numbers, barcodes, logos, and other identifiers. Laser marking is essential for ensuring traceability, compliance with industry regulations, and enhancing brand identity. The technology is valued for its ability to produce high-contrast, long-lasting marks without compromising the integrity of the metal.
APPLICATIONS
Traceability and Compliance:
- Application: Laser marking is extensively used to engrave serial numbers, batch codes, and other critical information on metal parts for traceability throughout the production process and the product lifecycle. This is particularly important in industries where stringent regulations require detailed records of each component.
- Benefit: Ensures that every part can be tracked and traced from manufacturing to end use, which is essential for quality control, recalls, and regulatory compliance.
Branding and Logos:
- Application: Metal fabricators use laser marking to add company logos, product names, and other branding elements to metal components. This application is common in the production of consumer goods, industrial equipment, and automotive parts.
- Benefit: Enhances brand visibility and adds value to the product by ensuring that the branding is clear, durable, and resistant to wear over time.
Barcodes and QR Codes:
- Application: Laser marking is used to engrave barcodes, QR codes, and other machine-readable identifiers on metal parts. These marks are crucial for inventory management, automated assembly processes, and product authentication.
- Benefit: Provides a reliable and scannable means of identification that integrates seamlessly with modern supply chain and inventory management systems.
Part Numbering and Specifications:
- Application: Fabricators often use laser marking to inscribe part numbers, specifications, and assembly instructions directly onto metal components. This is especially useful in industries like aerospace, automotive, and heavy machinery, where precise assembly and maintenance are critical.
- Benefit: Reduces the risk of assembly errors by ensuring that parts are correctly identified and used in the right context, improving overall efficiency and safety.
Safety and Compliance Labels:
- Application: Laser marking is used to create safety warnings, compliance labels, and instructional markings directly on metal surfaces. These are essential for ensuring that equipment is used safely and in accordance with regulations.
- Benefit: Produces clear, permanent marks that remain legible even in harsh environments, ensuring ongoing compliance and safety.
Data Plates and Tags:
- Application: Data plates and tags made of metal often require precise, permanent marking for identification and regulatory information. Laser marking provides the precision needed to create detailed and durable data plates that can withstand extreme conditions.
- Benefit: Delivers high-quality, durable markings that are resistant to environmental factors such as heat, moisture, and abrasion, ensuring the longevity of critical information.
Advantages of Laser Marking in Sheet Metal Fabrication:
- High Precision and Quality: Laser marking provides extremely precise and clean markings with high contrast, making them easily readable and ensuring they meet industry standards.
- Permanent and Durable: The marks created by laser are permanent, resistant to wear, corrosion, and environmental conditions, ensuring that they last for the entire lifecycle of the product.
- Non-Contact Process: Laser marking does not physically touch the metal, reducing the risk of damage or deformation, which is particularly important for thin or delicate metal components.
- Versatility: Laser marking can be applied to a wide range of metals, including stainless steel, aluminum, copper, and titanium, with the ability to mark complex shapes and curved surfaces.
- Speed and Efficiency: Laser marking is a fast process that can be easily integrated into production lines, improving throughput and reducing bottlenecks in manufacturing processes.
Solutions Offered by Scantech Laser:
- Fiber Laser Marking Systems: Designed for high-speed, high-precision marking on various metals, our fiber laser systems deliver sharp, clear, and durable marks, ideal for both large-scale production and custom jobs.
- CO2 Laser Marking Solutions: While primarily used for non-metals, CO2 lasers can also be employed for marking certain coated metals or anodized surfaces, offering versatility in application.
- Deep Engraving Lasers: For applications requiring deeper marks, such as data plates or high-wear components, Scantech offers deep engraving solutions that ensure the longevity and legibility of marks.
- Custom Marking Solutions: We provide tailored laser marking solutions to meet specific industry needs, whether for unique marking requirements, complex surfaces, or integration with existing automation systems.
Conclusion:
Laser marking is an indispensable tool in the sheet metal fabrication industry, offering unmatched precision, durability, and efficiency. It plays a crucial role in ensuring traceability, compliance, and brand visibility, making it a key technology for manufacturers across various sectors. Scantech Laser’s advanced marking solutions empower manufacturers to enhance the quality and reliability of their products, meet regulatory requirements, and strengthen their brand presence in the market.
OVERVIEW
Laser drilling is a critical process in the sheet metal fabrication industry, enabling the creation of precise, high-quality holes in various metal materials. This technology is highly valued for its ability to produce holes with exceptional accuracy, consistency, and minimal thermal distortion. Laser drilling is particularly effective in applications where traditional mechanical drilling methods may fall short, such as when working with hard-to-machine materials or requiring extremely fine holes. The non-contact nature of laser drilling also reduces wear and tear on tools, making it a cost-effective and efficient solution for modern manufacturing needs.
APPLICATIONS
Precision Hole Drilling for Aerospace Components:
- Application: Laser drilling is used to create precise holes in aerospace components, such as turbine blades, engine parts, and structural elements. These components often require small, high-quality holes for cooling, fluid flow, or fastening purposes.
- Benefit: Ensures high precision and consistency, critical for maintaining the performance and safety of aerospace components under extreme conditions.
Micro-Hole Drilling in Electronics and Microelectronics:
- Application: In the electronics industry, laser drilling is employed to produce micro-holes in metal parts for circuit boards, connectors, and microelectromechanical systems (MEMS). These tiny holes are essential for electrical connections, fluid dynamics, and ventilation in miniaturized devices.
- Benefit: Enables the production of extremely fine and accurate holes that are essential for the functionality of modern electronic devices.
Perforation of Metal Sheets for Filtration Systems:
- Application: Laser drilling is used to create perforated metal sheets for use in filtration systems, sieves, and screens. The ability to drill uniform, high-density holes allows for precise control over the flow of liquids or gases through the material.
- Benefit: Provides consistent and high-quality perforations that enhance the efficiency and reliability of filtration systems across various industries.
Cooling Holes in Automotive Components:
- Application: In the automotive industry, laser drilling is utilized to create cooling holes in components such as brake discs, exhaust systems, and turbochargers. These holes are crucial for managing heat and improving the performance of the vehicle’s systems.
- Benefit: Improves the thermal management and durability of automotive components, contributing to overall vehicle safety and performance.
Venting and Pressure Relief Holes in Industrial Equipment:
- Application: Laser drilling is applied to create venting and pressure relief holes in various industrial equipment, including pressure vessels, heat exchangers, and fuel tanks. These holes are designed to regulate pressure and prevent equipment failure.
- Benefit: Ensures the safe operation of industrial equipment by providing reliable and accurately placed venting solutions.
Orifice Plates and Nozzles:
- Application: Laser drilling is used to manufacture orifice plates and nozzles, which require precise hole sizes for controlling fluid or gas flow in various industrial processes.
- Benefit: Delivers highly accurate holes that ensure consistent and reliable performance in flow control applications, such as in the oil and gas, chemical, and food processing industries.
Advantages of Laser Drilling in Sheet Metal Fabrication:
- High Precision and Accuracy: Laser drilling provides unmatched precision, capable of producing holes with diameters as small as a few micrometers and with tight tolerances.
- Minimal Thermal Distortion: The focused nature of the laser beam minimizes heat input, reducing thermal distortion and preserving the integrity of the surrounding material.
- Versatility: Laser drilling is effective on a wide range of metals, including stainless steel, aluminum, titanium, and exotic alloys, making it suitable for diverse applications.
- Non-Contact Process: The non-contact nature of laser drilling reduces mechanical stress on the material and eliminates tool wear, leading to longer service life and reduced maintenance costs.
- High-Speed Production: Laser drilling can be performed at high speeds, increasing production efficiency and allowing for the rapid processing of large volumes of components.
Solutions Offered by Scantech Laser:
- High-Power Laser Drilling Systems: Our systems are designed to handle a variety of metal types and thicknesses, offering high-speed, high-precision drilling capabilities that meet the demanding requirements of the sheet metal fabrication industry.
- Multi-Axis Laser Drilling: For complex parts requiring holes at various angles, our multi-axis laser drilling solutions provide the flexibility needed to achieve precise drilling across different planes.
- Micro-Hole Drilling Solutions: We offer specialized systems for micro-hole drilling, capable of producing extremely small and accurate holes for applications in electronics, aerospace, and medical devices.
- Automated Laser Drilling Solutions: Scantech provides fully automated laser drilling systems that integrate seamlessly into existing production lines, enhancing efficiency and consistency across high-volume manufacturing operations.
Conclusion:
Laser drilling is an essential technology in the sheet metal fabrication industry, offering unparalleled precision, versatility, and efficiency. It is used across a wide range of applications, from aerospace to automotive, where the quality and accuracy of drilled holes are critical to the performance of the final product. Scantech Laser’s advanced drilling solutions empower manufacturers to achieve superior results, improve production speeds, and reduce costs, ensuring they stay competitive in a fast-evolving industry.
OVERVIEW
Laser cleaning is a highly effective, environmentally friendly technology used in the sheet metal fabrication industry to remove contaminants such as rust, paint, oxide layers, grease, and other residues from metal surfaces. This process uses a high-energy laser beam to ablate unwanted materials without damaging the underlying metal. Laser cleaning offers significant advantages over traditional cleaning methods, such as chemical treatments or abrasive blasting, by providing a precise, non-contact, and eco-friendly solution that reduces waste and improves surface preparation quality.
APPLICATIONS
Rust and Oxide Removal:
- Application: Laser cleaning is widely used to remove rust and oxide layers from metal surfaces, particularly in preparation for welding, coating, or painting. The laser effectively ablates the rust, leaving behind a clean, bare metal surface that is ideal for further processing.
- Benefit: Ensures optimal surface quality for subsequent fabrication processes, reducing the risk of defects and improving the durability of the finished product.
Paint and Coating Removal:
- Application: Laser cleaning is employed to strip paint, coatings, or other surface treatments from metal components without using harsh chemicals or abrasive media. This is particularly useful for rework, refurbishment, or maintenance tasks where the original metal surface needs to be preserved.
- Benefit: Provides a clean and controlled method for removing coatings, minimizing environmental impact and preserving the integrity of the metal substrate.
Weld Preparation and Post-Weld Cleaning:
- Application: Prior to welding, laser cleaning is used to remove contaminants such as oil, grease, and rust from the metal surface, ensuring a strong, defect-free weld. Post-weld, laser cleaning can be used to remove oxide layers, discoloration, and other residues resulting from the welding process.
- Benefit: Improves weld quality by ensuring a clean surface before welding and enhances the appearance and corrosion resistance of the weld afterward.
Surface Preparation for Adhesive Bonding:
- Application: Laser cleaning is used to prepare metal surfaces for adhesive bonding by removing contaminants and creating a micro-textured surface that improves adhesion. This is critical in applications where strong, reliable bonds are required.
- Benefit: Enhances the strength and durability of adhesive bonds, reducing the risk of bond failure and improving the overall quality of the assembly.
Mold Cleaning in Metal Forming:
- Application: In the metal forming industry, laser cleaning is used to clean molds and dies by removing residues such as lubricants, carbon deposits, and scale. This process helps maintain the precision and quality of the molds, extending their service life.
- Benefit: Reduces downtime and maintenance costs by providing a non-destructive method for maintaining molds and dies, ensuring consistent production quality.
Historical Restoration and Conservation:
- Application: Laser cleaning is used in the restoration and conservation of historical metal structures and artifacts. The precision of laser cleaning allows for the removal of corrosion, oxidation, and other surface contaminants without damaging the original metalwork.
- Benefit: Preserves the integrity of historical metal objects while effectively removing damaging residues, making it a preferred method for conservation work.
Advantages of Laser Cleaning in Sheet Metal Fabrication:
- Non-Contact Process: Laser cleaning is a non-contact method, meaning there is no physical abrasion or impact on the metal surface, which reduces the risk of damage or distortion, especially on delicate or thin materials.
- Precision and Control: The laser can be precisely controlled to target specific areas, making it ideal for cleaning intricate parts or surfaces with complex geometries.
- Environmentally Friendly: Laser cleaning eliminates the need for chemicals or abrasive media, reducing waste and minimizing environmental impact.
- Cost-Effective: By reducing the need for consumables and minimizing downtime for maintenance, laser cleaning can be more cost-effective than traditional methods in the long run.
- Versatility: Laser cleaning can be used on a wide range of metals and surface conditions, making it a versatile solution for various cleaning and surface preparation needs.
Solutions Offered by Scantech Laser:
- Portable Laser Cleaning Systems: Designed for flexibility and mobility, our portable laser cleaning solutions are ideal for on-site cleaning tasks, maintenance, and refurbishment projects in various industrial settings.
- High-Power Laser Cleaning Systems: Our high-power systems are suited for large-scale industrial applications where fast, efficient cleaning is required, such as in automotive or aerospace manufacturing.
- Precision Laser Cleaning Solutions: For applications requiring detailed cleaning or surface preparation, we offer precision laser cleaning systems capable of targeting small areas with high accuracy.
- Automated Laser Cleaning Systems: Scantech provides fully automated laser cleaning solutions that can be integrated into production lines, ensuring consistent and efficient cleaning as part of the fabrication process.
Conclusion:
Laser cleaning is a game-changer in the sheet metal fabrication industry, offering a precise, efficient, and environmentally friendly alternative to traditional cleaning methods. Its ability to prepare metal surfaces without causing damage makes it invaluable for applications ranging from rust removal to weld preparation. Scantech Laser’s advanced cleaning solutions empower manufacturers to enhance product quality, reduce operational costs, and meet the highest standards of environmental responsibility.
DEDICATED TO INNOVATION
At Scantech Laser, our dedication to the sheet metal processing industry extends far beyond simply meeting customer demands; it’s about leading innovation and shaping the future of metal fabrication. Understanding the crucial role that sheet metal processing plays in various industries, we are committed to delivering customized laser solutions that tackle the unique challenges and opportunities within this sector. Whether it’s enhancing cutting precision, optimizing material usage, or increasing production efficiency, our focus is on driving the advancement of sheet metal processing with state-of-the-art laser technology.
Enhancing Sheet Metal Processing with Laser Precision
In the rapidly evolving sheet metal processing industry, precision, speed, and reliability are essential. Scantech Laser’s advanced laser technologies are tailored to meet these critical demands, providing solutions that significantly improve the efficiency and quality of sheet metal fabrication. From precise laser cutting and welding to accurate marking and drilling, our state-of-the-art systems ensure unmatched precision and consistency. This guarantees that every sheet metal component produced meets the highest standards of quality, driving excellence in sheet metal processing.
Advancing Sheet Metal Processing with Laser Solutions
Our approach to the sheet metal processing industry enables us to envision its long-term future while addressing current growth and development needs. Whether it’s achieving precise cuts through advanced laser cutting techniques, enhancing joint strength with precise laser welding, or improving component traceability with durable laser marking, Scantech Laser’s solutions are at the forefront of sheet metal innovation.
Driving Sheet Metal Processing Forward with Laser Solutions
As the sheet metal processing industry continues to evolve, Scantech Laser remains committed to supporting its growth with innovative, reliable, and efficient laser solutions. We are dedicated to understanding the unique challenges of this industry and providing the technologies that will drive its success in the years to come. Together, we’re not just meeting the needs of today; we’re propelling the sheet metal processing industry into the future.