A connecting rod is an engine element that transfers movement from the piston to the crankshaft and features a lever arm. Connecting rods are generally crafted from forged or solid metallic alloys and are designed to face up to dynamic stresses from combustion and piston movement.
HOW DOES A CONNECTING ROD WORK?
A Connecting rod is used to switch the reciprocating movement of the piston into the rotary movement of the crankshaft. As its call implies, it connects the piston to the crankshaft. Connecting rods have ends – the Small End and the Big End. The small quit is hooked up to the piston pin and the huge quit is related to the crank pins. The small quit might also additionally have a strong or cut-up eye (nearly continually strong in automobile engines) however the huge quit is continually cut up (frequently strong in small bike engines).
The cut-up shoulder quit is assembled with a connecting rod cap and connecting rod bolts. An oil hollow is every now and then drilled thru the shank to permit a waft of lubricating oil from the huge quit to the small quit. The oil involves the huge quit thru the crankshaft from the oil pump and is going to the piston pin and piston thru the small quit. The connecting rod in operation is subjected to blended axial and bending stresses. The combustion fuel online strain and inertia forces produce axial stresses at the same time as bending stresses are produced because of centrifugal effects. To decrease those inertia hundreds a connecting rod must be as robust and as mild as possible.
HOW TO CHOOSE THE RIGHT CONNECTING RODS?
Connecting rods are subjected to greater stress than any other engine component. Choosing the strongest crank for a performance goal is absolutely essential. As we all know, if a connecting rod fails, the engine can be scrapped in a split second. How do you get the right connecting rods for your engine?
It’s not as easy as it seems. Which connecting rod you choose is very important when building your engine. Connecting rods play a huge role in your engine’s performance and longevity. And there are a few factors to consider when choosing your cranks. In most cases, you will choose between I-beam and H-beam braces.
- I-BEAMS VS H-BEAMS
- To understand why they are called H- and I-beam braces, you need to look at their cross-section. You have to look at the connecting rod from above like you would look at the cylinder bore from above. Then cut the top half of the rod and get the cross-section. The H-beam cross-section is a capital H, while the I-beam cross-section is a capital I.
Now that we know why they are called I beams and H beams, let’s see which one is better. Which ones should you add to your prized engine? Well, I’ll be honest with you. I beam vs. H beam is a very controversial topic.
There was a common belief for a while that the H-beam design was stronger and the I-beam design was lighter. On this basis, the H-beam design is said to be better suited to the high combustion pressures of turbocharging, and the I-beam design is better suited to high-revving naturally aspirated engines due to its lower weight. This is a general rule of thumb at best. To be honest, it’s not even a general rule because today we have so many exceptions to that rule that it just doesn’t apply.
Never water again.
You can also hear that the I-beam is better at handling normal forces, while the H-beam is better at handling abnormal forces. The H-beam resists bending at the end better. Again, this is a general rule of thumb, and design precautions are key in ensuring the rod handles the normal and abnormal forces in an engine. If the bar is made of the right material and the
the design includes that material in the right places, both the I-beam and H-beam can be made to handle abnormal and normal forces equally well.
So which one should you choose?
If you are a car enthusiast building an engine for the street, some track days, or maybe some amateur racing. It really doesn’t matter at all. Any design will work just fine and you really shouldn’t focus so much on whether the bar is an H-beam or an I-beam but instead focus on what material the bar is made of and how it’s made becomes. STEEL CONNECTING RODS VS. ALUMINUM
When it comes to materials, most cranks are steel, but for drag racing applications, aluminum cranks are also a tempting option. Many manufacturers make steel connecting rods in many different styles, and they can be cast, forged, or machined. Aftermarket steel connecting rods are made from forged steel, and there are different types of forged steel depending on the grade of the material. For highly modified competitive applications, most manufacturers, including us (Scantech Laser), use
4340 steel. We know aluminum is a much weaker material than steel.
While carbon steel typically has a tensile strength of around 200,000 psi, aluminum only achieves around 95,000 psi. So why the heck would you put something twice as weak in an engine and subject it to all the extreme engine loads? Operation? Because aluminum is much lighter than steel!
And when it comes to high-performance engines, light is just the ticket! The lighter your engine’s rotating assembly, the better! Aluminum bars also have the ability to act as shock absorbers. Because they somehow yield under the peak loads present in an engine, they help absorb those loads and transmit less stress to the bearings and crankshaft. But there is a price for all benefits.
Aluminum has a much shorter fatigue life compared to steel and motors with aluminum rods need to warm up slowly and fully before you can hit them, and after you’ve hit them you need to let them cool down a bit. Another thing to consider when installing aluminum bars in your engine is spacing. Sometimes they don’t clean crankcase parts like belts or cylinder heads and need to be trimmed to fit the bars.
WHAT ARE THE SYMPTOMS OF CONNECTING ROD FAILURE ON YOUR VEHICLE?
A connecting rod must be strong and durable for the engine to survive. If it’s too weak to withstand the combustion load, all the pressure will wear it down and deform it. As for the driver, you can tell when this is happening as there are some very noticeable symptoms. Below are the 4 most common symptoms of connecting rod failure.
Low engine oil level:
If you have a bad or defective connecting rod, your engine may be using too much oil. Because of this, your engine can always be low on oil. The oil needs to be changed more frequently than usual. Engine knocking noises When the engine is on and running, you may hear a knock. This is a repeated knocking sound that gets faster as the engine speed increases.
The noise may go away after a while once your oil has a chance to circulate through and lubricate the engine components. Reduced Oil Pressure A failed connecting rod can have a devastating effect on your engine’s oil pressure. Your engine may have an oil pressure gauge that will alert you to low oil pressure. You may also have a warning light on your dashboard letting you know.
If you have low oil pressure, it means the oil is not circulating properly through the engine. This could cause the engine to overheat if the problem is not corrected quickly. Bent or damaged rod If you suspect that you have a bent or damaged connecting rod based on the other symptoms that may be present, you should visually inspect the connecting rod itself to determine its condition. This would require disassembly of the engine, a job that should only be done by a mechanic.
When manufacturing connecting rods the process of creating a crank hole for separation is an important one. But before it can be cracked, a notch has to be scribed on the inner wall of the crank hole. The notch is usually a weak point to dissipate the tension thereby controlling the crank location. Laser Scribing is the technique through which the highest quality notch
for the splitting process can be achieved. This state-of-the-art machine needs a quick setup time. It can run 24×7 in continuous operations without any hassle since this does not require frequent maintenance or consumables change time. Its scribed output is completely ready for the direct fracturing process without any additional process. The machine is diversified in various ranges and features to meet the requirements of customers’ needs. The new introduction of the OEM Module allows customers to explore the possibility to integrate into their existing line or machine.
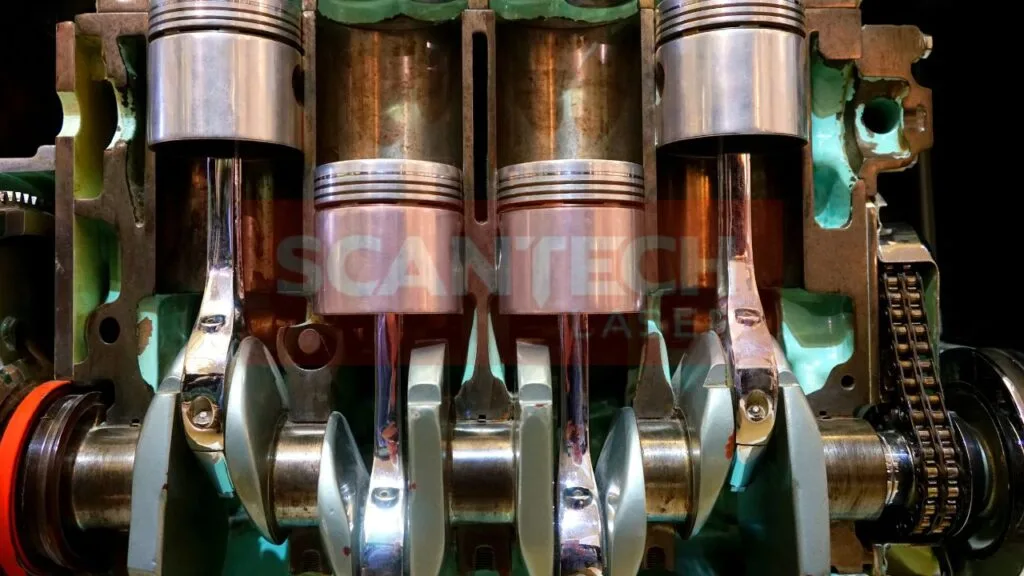
Why buy Laser Scribing Machine From Scantech Laser?
All Scantech Laser connecting rods are precision hot forged and then CNC machined to ensure a perfect fit and finish. All Scantech Laser connecting rods are made of 4340 steel and have multi-stage heat treatment, surface treatment, X-ray, and Magnafluxe treatment. Scantech Laser offers a seamless online shopping experience and the streamlined e-commerce interface makes it easy for you to find the Connecting Rods you want. Scantech Laser offers a variety of cranks in Sports Performance and Street Performance. We provide Scantech Laser-Scribing Machine For Connecting Rods
Key Poka-Yoke Features:
- Tip Touch Sensor: To prevent positional malfunction or wrong data feeding.
- Fixture Detection Sensor: To auto-detect wrong parameters & prevent accidents.
- Job Butting Sensor: To verify the connecting rod is resting at the correct position and side.
- Home Positioning Sensors: To ensure every cycle produces the same positioning results.
Advantages of using Scantech Laser-Scribing Machine?
- Phenomenal Beam Parameter Product (BPP)
- Steady BPP Over Entire Power Range
- Higher Wall-Plug Efficiency
- Maintenance Free Operation
- Easy ‘Plug and Play Design
- Higher Diode MTBF Life
- Allows Processing of Highly Reflective Materials
- High Photon Conversion Efficiency
- Alignment Free Operations