Table of Contents
- Introduction to High-Speed Laser Cladding
- Why High-Speed Laser Cladding is Crucial for Disc Brakes
- Euro 7 and BS 7 Standards: Environmental and Performance Requirements
- Scantech Laser’s Innovative High-Speed Laser Cladding Solutions
- The Future of High-Speed Laser Cladding in Automotive Manufacturing
- Conclusion
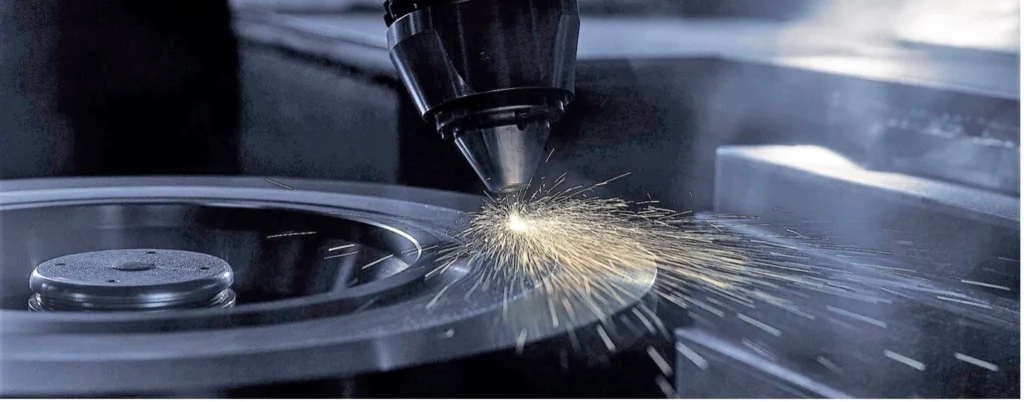
Introduction to High-Speed Laser Cladding
High-speed laser cladding is a cutting-edge additive manufacturing process used to coat substrates like brake discs with specialized materials to enhance their performance. The process uses a high-intensity laser beam to heat and fuse powdered or wire material, which is rapidly deposited onto the surface of the substrate, creating a strong and uniform coating.
This technology is revolutionizing the automotive industry due to its precision, reliability, and ability to produce wear-resistant surfaces with minimal heat distortion. Unlike traditional thermal spray or plating methods, laser cladding provides superior bonding and can achieve micron-precise coatings that greatly extend the life of critical automotive components, such as disc brakes.
For manufacturers, high-speed laser cladding delivers:
- Higher productivity: Faster processing speeds compared to conventional techniques.
- Material versatility: Ability to use various alloys (like nickel and tungsten carbide).
- Cost-efficiency: Reduced material wastage and improved production output.
How It Works:
- Laser Beam Precision: A high-intensity laser melts the cladding material, typically alloys like chromium-based coatings.
- Controlled Deposition: The process ensures minimal heat impact, reducing substrate deformation while enhancing durability.
- Efficiency: High deposition rates make this method highly productive compared to traditional methods like thermal spraying.
Benefits:
- Wear Resistance: The coated layer extends disc lifespan by reducing wear.
- Corrosion Protection: Cladding prevents rusting, crucial for safety and durability.
- Reduced Environmental Impact: Lower particulate emissions align with global environmental regulations.
Laser cladding delivers a unique combination of speed, efficiency, and precision, making it a game-changer in the automotive sector.
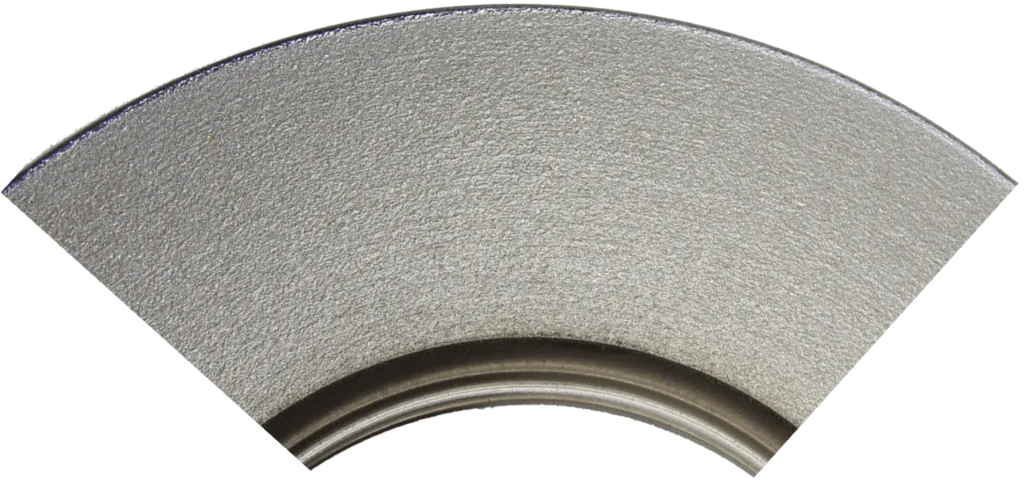
Why High-Speed Laser Cladding is Crucial for Disc Brakes
Disc brakes play an essential role in vehicle safety and performance. Traditional brake discs, often made from cast iron, are prone to wear, corrosion, and thermal stress due to constant friction during braking. Over time, this can degrade braking efficiency and lead to increased maintenance costs.
High-speed laser cladding addresses these limitations by applying specialized, wear-resistant coatings to the disc surface. The key benefits include:
- Improved Wear Resistance: Laser-clad coatings significantly reduce material loss caused by friction.
- Corrosion Protection: Special alloys applied via laser cladding resist oxidation and environmental degradation.
Why This Matters:
With modern vehicles becoming heavier and more performance-oriented, the demand for robust braking systems has never been higher. Additionally, urban driving conditions exacerbate wear and tear on brake discs. Laser cladding ensures disc brakes can meet these challenges without compromising on safety or efficiency.
By investing in Scantech Laser’s high-speed cladding technology, manufacturers achieve enhanced product durability while reducing the total cost of ownership for their customers.
Challenges with Traditional Brake Discs:
- Wear and Tear: High-speed braking generates friction, leading to disc wear and frequent replacements.
- Particulate Emissions: Fine dust particles from brake wear contribute to environmental pollution.
- Limited Performance: Traditional materials are insufficient to meet modern vehicle demands.
Key Improvements Using Laser Cladding:
- Surface Hardness: Clad coatings enhance the disc’s resistance to friction and abrasion.
- Emission Reduction: Studies show up to 90% reduction in fine dust emissions.
- Extended Lifespan: Clad discs last significantly longer, reducing maintenance costs.


Euro 7 and BS 7 Standards: Environmental and Performance Requirements
Environmental sustainability has become a key priority for the automotive industry, driven by increasingly stringent regulations such as Euro 7 and BS 7 standards. These regulations aim to reduce both exhaust emissions and non-exhaust emissions, including particulate matter from brake discs and tires.
The Problem: Brake Dust and Air Quality
Traditional braking systems, especially those using untreated cast iron discs, generate significant amounts of fine particulate matter (PM10 and PM2.5). Friction between the brake pad and disc causes wear, releasing microscopic dust particles into the air. Studies show that brake dust emissions contribute up to 30% of total vehicle-related particulate pollution, a serious concern in urban areas.
Laser Cladding: A Proven Solution for Reducing Brake Dust
Laser cladding technology offers a sustainable solution to this challenge. By applying a durable, wear-resistant coating on brake discs, the process:
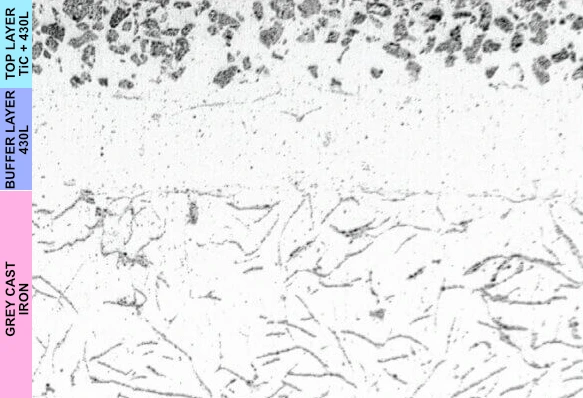
- Minimizes Material Loss: Laser-clad coatings significantly reduce wear on the brake disc surface, cutting down fine dust emissions by up to 90%.
- Improves Wear Resistance: The hard-coated surface withstands high-friction braking forces, dramatically reducing particulate matter generation.
- Enhances Longevity: With slower wear rates, laser-clad discs last significantly longer, requiring fewer replacements and minimizing waste.
Ensuring Compliance with Euro 7 and BS 7
The Euro 7 standard, set to come into effect in 2025, introduces strict limits on non-exhaust emissions, such as brake dust. The BS 7 standard aligns closely, targeting improved air quality by mandating reduced particulate matter emissions from braking systems.
Laser cladding effectively ensures compliance with these standards by achieving:
- Lower Emissions: A substantial reduction in wear-induced particulate matter.
- Eco-Friendly Manufacturing: Longer-lasting brake discs reduce production emissions and material waste.
Scantech Laser’s Innovative High-Speed Laser Cladding Solutions
Scantech Laser is a leading provider of cutting-edge high-speed laser cladding solutions designed specifically to address the challenges of modern disc brake manufacturing. By combining innovation, precision, and sustainability, our systems help manufacturers enhance product quality, improve productivity, and meet stringent environmental regulations such as Euro 7 and BS 7 standards.
Key Features of Scantech Laser Solutions
- High Deposition Rates: Our advanced laser systems enable rapid material deposition, significantly increasing productivity without compromising on coating quality. This makes our technology ideal for high-volume manufacturing environments.
- Precision Control: Scantech’s laser cladding systems deliver unmatched precision, ensuring uniform and defect-free coatings. Even at high deposition rates, our technology maintains consistent coating thickness and quality across the brake disc surface, improving performance and longevity.
- Material Compatibility: Flexibility is at the heart of Scantech’s solutions. Our systems work seamlessly with a variety of materials, including:
- Nickel-Based Alloys: Known for their corrosion resistance and durability.
- Carbide Composites: Offering exceptional hardness and wear resistance.
- Custom Coatings: Tailored to meet specific performance and regulatory requirements.
4. Environmentally Friendly Technology
Scantech Laser’s high-speed cladding technology aligns with global sustainability goals and meets the strict requirements of Euro 7 and BS 7 standards. By drastically reducing brake dust emissions, our solutions:
- Minimize Environmental Impact: Laser-clad discs generate up to 90% fewer particulate emissions, reducing urban air pollution.
- Support Sustainable Manufacturing: Enhanced durability and longer product life cycles mean fewer replacements, reducing material waste and carbon footprint.
Why Choose Scantech Laser?
At Scantech Laser, we combine innovation with reliability to deliver solutions that meet the evolving needs of the automotive industry. Our high-speed laser cladding technology not only enhances brake performance but also ensures compliance with future-ready environmental regulations.
By choosing Scantech Laser, manufacturers gain:
- Improved product quality and reliability.
- Greater operational efficiency and productivity.
- Compliance with global environmental standards like Euro 7 and BS 7.
For manufacturers seeking precision, performance, and sustainability, Scantech Laser provides the ultimate solution for high-speed laser cladding in disc brake manufacturing.
The Future of High-Speed Laser Cladding in Automotive Manufacturing

With rapid advancements in laser cladding processes, the future of this transformative technology looks exceptionally promising. Driven by innovation in material science, faster laser systems, and the integration of robotics and AI, laser cladding is set to play an even more significant role in the automotive industry. As manufacturers focus on sustainable and high-performance solutions, laser-clad brake discs are emerging as the technology of choice.
Innovations on the Horizon
- Automation and AI Integration: The future of laser cladding will see greater integration of Artificial Intelligence (AI) and automation technologies to:
- Enable real-time process monitoring for precision and defect-free coating applications.
- Optimize material usage and deposition parameters for maximum efficiency.Reduce production downtime through predictive maintenance and AI-driven fault detection.
Combining AI with robotic systems will revolutionize high-speed laser cladding, enhancing consistency, throughput, and quality, especially for mass production in automotive manufacturing.
2. Mass Adoption in the Automotive Industry
With the introduction of stricter environmental regulations like Euro 7 and global counterparts like BS 7, laser-clad brake discs are becoming a necessity. Manufacturers who prioritize sustainable transportation and compliance with evolving standards will increasingly adopt laser cladding as a mainstream solution.
- Cost Reduction: Innovations in laser technology will lower production costs, making laser-clad brakes accessible for mass-market vehicles.
- Eco-Friendly Manufacturing: With up to 90% reduction in particulate emissions, laser cladding will align with future mandates for cleaner air and sustainable vehicle production.
- Standardization: Laser cladding processes will become an industry standard, ensuring all vehicles meet stringent emission limits without sacrificing performance.
Driving Towards a Sustainable Future
As the automotive industry embraces cleaner, greener technologies, high-speed laser cladding will be a driving force behind this transformation. Scantech Laser remains committed to leading this evolution by delivering innovative, future-ready solutions that meet the demands of modern manufacturing while ensuring compliance with upcoming Euro 7 and BS 7 standards.
Through advancements in coating materials, AI integration, and automation, laser cladding is not just the solution of today—it is the technology of tomorrow.
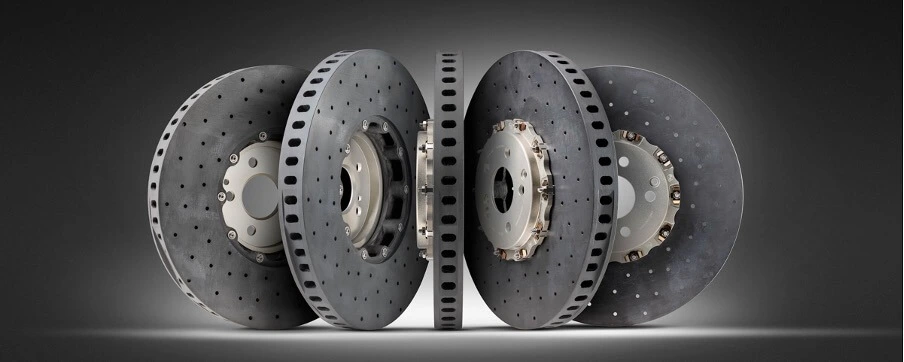
Conclusion
High-speed laser cladding is revolutionizing disc brake manufacturing by providing unmatched performance, durability, and environmental compliance. With the ability to significantly reduce wear-induced particulate emissions—by up to 90%—laser-clad brake discs align perfectly with the stringent Euro 7 and BS 7 standards
Scantech Laser’s cutting-edge solutions enable automotive manufacturers to stay ahead of regulatory changes while delivering cost-effective, high-performance products. By embracing this advanced technology, the industry can move toward a cleaner, more sustainable future without compromising on quality or safety.
For more information about Scantech Laser’s high-speed laser cladding systems and how they can optimize your manufacturing processes, contact us at:
🌐 www.scantechlaser.com